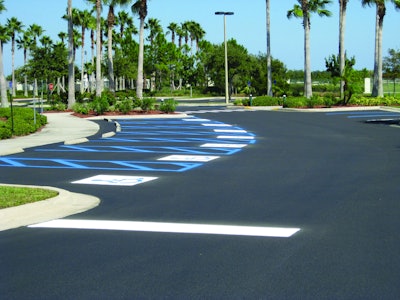
It isn't every day that a contractor encounters an equipment inspection or background check before winning the bid for a project; however, husband and wife team, Robert and Michelle Hornor, went through just that — and more — before winning the bid for a recent project. The Hornor's, owners of Reliable Pavement Maintenance, Inc. located in Orlando, FL, went through several unique steps before stepping foot on the property to begin the government project.
RPM completed a 292,200-square-foot sealcoating and striping of the Viera Outpatient Clinic, a clinic for veterans, located in Melbourne, FL. It was a standard pavement maintenance project that suffered from oxidation and a little water damage.
Meeting Government Standards
Unlike most pavement maintenance projects, contractors must be aware of several requirements when bidding and completing government jobs. "It truly depends on the security levels you are working on with the government, and each job has different requirements," Michelle says. "We went in as a subcontractor under another contractor who we are very familiar with, and they are familiar with the bid process and all of the paperwork entailed."
After the paperwork was submitted, Robert was brought to the site for an interview and a walk around the property. In order to have proof everything was in working order, an equipment inspection to meet the requirements was completed. RPM also had to submit all products being used as well as samples, per request, of sealcoat and paint spray outs to meet millage for verification. A background screening and drug test were also completed.
Within two weeks of completing the tests and inspections, RPM was awarded the job. The Viera VA was the third VA hospital that Reliable Pavement Maintenance, Inc worked on. Completing other VA hospital projects is only of several benefits RPM has received after finishing the paperwork and interviews. "Now, any job our contractor has at one of the VA hospitals with parking lots they call Rob directly," Michelle says.
A One Man Show
What typically might take a four to six man crew, Robert was able to prep, sealcoat, and stripe without any other crew members. Robert made several modifications to his Neal 200 squeegee machine in order to increase production and make the equipment more versatile for RPM. "It had a small spray pump, so I increased the size of the spray pump," Robert says. "I made a spray bar for it and attached it to the machine so we had something that would do as a spray rig."
Robert used SealMaster products, a Seal-Rite 700 as a bulk tanker, a Graco 3900, and a Titan 4900 on the job.
He worked the project on the weekends completing it in four weekends, two weekends ahead of schedule. "That was the only time the VA would close, and the place was so busy there was no way to do work out there during the week," Robert says.
The hospital had four different parking lots. Robert would work on one parking lot each weekend going out on Friday night to close the parking lot down. A locked gate surrounded Robert, and a guard sat out front watching him to make sure all of the work was finished.
Each weekend, he would clean the lot and prep the area Friday night, sealcoat the pavement Saturday, and stripe it Sunday. The biggest challenge Robert faced with the project was the weather. "The biggest thing was getting the sealer down in between thunder showers because we didn't have any makeup dates," he says.
One interesting encounter with this project was the handicap stalls. The 30 handicap stalls had several different markings, some with white backgrounds and blue symbols while others had only blue symbols. "The VA was built in stages and the handicap stalls all had different symbols," Robert says. "Being government spec, you have to replace what you took out exactly because they don't like changes." In order to ensure he painted all of the markings as they were originally, Robert photo documented the project as he went along.
Bidding and working government jobs can have several other requirements and standards that need to be met unlike most pavement maintenance projects. Michelle offers several tips for contractors looking to bid government work. "Make sure if you are working a government property that your bid is entire as requested," she says. "There are no change orders. Make sure you have the proper insurance and the proper equipment, and that you meet all of the standards required."
Enhancing Customer Service
While taking pictures of this project were necessary for Robert to make sure he completed the job as it was originally, photo documentation is something that RPM does for every project.
When they first began the company, Michelle realized that most contractors don't document their jobs with photographs. So, she and her husband began taking photos of all of their jobs from start to finish.
As a result, Michelle would compile these photos onto a CD and send it to the client once the job was completed. "We give them CD's with photos so they know exactly the process we are taking to refurbish their parking lot, and it lets them see the before and after on it," Robert says.
"Most people like it because they can refer back to something if they have an issue or further questions and to show others the protected asphalt and curb appeal they had completed on their property," Michelle says.
Not only do the photos give their clients a look into the process, but it also helps Robert guarantee his work. It has also increased business as clients show what they have had completed. Michelle says, “It’s one more business card stamp for Reliable Pavement Maintenance in our profession.”