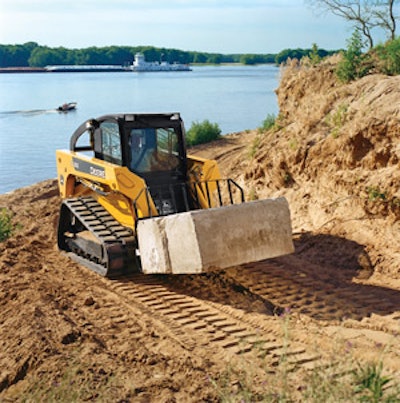
Today's skid-steer and compact track loader operators may be able to take a page from excavator operator manuals when it comes to driving, steering and operating their loaders. That's because the joystick controls found in most excavators are migrating to many of these machines.
Joystick controls are also referred to as pilot controls, pilot joysticks and even hydraulic assist. But whatever the terminology used, the end result is the same - increased comfort and reduced fatigue. "They have greatly limited the amount of physical energy an operator is required to expend," says Tom Green, marketing director, New Holland Construction.
An added bonus is often increased productivity. "The onset of the joystick control has made it easier, simpler, less fatiguing and just more ergonomically pleasing to an operator," says Kelly Moore, Mustang Mfg. Reduced wrist and arm force and minimal hand and wrist movement enable operators to use a loader for longer periods. "They're not tired and worn out at the end of the day from pushing manual levers. There's a benefit in the ease of operation and minimizing of fatigue when compared to older styles. It gives operators fingertip control with very low effort."
"Whether it's precision grading or other functions, hydraulic pilot controls give operators smooth control," Green agrees. "Our low-effort joysticks provide instant control response with minimum movement, resulting in precise control, superior comfort and less fatigue. Operators experience a good hand-to-power control ratio that is easy to anticipate and has a 'good feel'. This translates to controls that are easily mastered, and inspires operator's confidence in performance."
Control at your fingertips
A typical skid-steer joystick is hydraulically controlled, and features drive/steering functions in the left handle, while the right handle controls loader arm functions, such as raising and lowering a bucket or tilting it forward or rearward.
Some manufacturers offer variations of controls, such as Bobcat's Advanced Control System (ACS) and Selectable Joystick Control (SJC) system. ACS gives operators the ability to switch between using hand actuators or foot pedals to activate the hydraulics. SJC features an electric joystick and provides the ability to change between ISO and H patterns by simply pressing a switch in the cab. "These systems allow an operator to operate a machine in their most learned method," says Mike Fitzgerald, product representative, Bobcat.
Oftentimes, buttons and toggle switches are embedded into the joystick handles, providing even greater control and finesse over a given task.
For Mustang machines, two-speed control can be achieved via a button in the left handle, so operators can engage a higher ground speed when moving around a jobsite. The right joystick offers float and ride control buttons, as well as proportional auxiliary control.
"With float control, anytime a customer wants to back grade and do some leveling, he pushes the button and the weight of the arm drops it to the ground where it follows the terrain of the ground," Moore says. "Ride control allows the load arm to float when it's carrying a load with a bucket or pallet fork, so the machine can operate much smoother. And instead of using your feet for pushing a lever, there's a simple toggle switch for your right thumb, so you can power the attachment with infinite control. Whether you're running an auger slowly or full speed, you have fingertip control."
The speed management feature on Bobcat machines provides the ability to run an attachment at a specific travel speed. "If you're frequently running an attachment such as a mower, you don't want the machine traveling full speed because it won't cut properly," says Fitzgerald.
The feature enables you to set the machine to whatever the conditions allow. "You can move the joystick to the full forward position, but you're only traveling at 40%, 50% or 60% of the machine speed," Fitzgerald notes.
Being able to maintain a steady speed makes attachment operation more efficient, especially when using attachments such as mowers, trenchers, planers and rototillers, Fitzgerald adds. "You can set it so you don't overload the attachment and run the hydraulics over relief," he explains. "Once you have it set to the proper speed, you don't have to be 'on task' all the time trying to watch your speed and keep the lever in the proper position. You can place the lever in the full forward or backward position, and the machine's maximum speed is set to the load on the attachment. It adds to the efficiency and comfort for the operator."
Horsepower management is another benefit gained with joystick controls in Bobcat models. "When you dig into a pile, the electrical system will help manage the power of the machine and the drive system," Fitzgerald states. "It's more efficient at digging, and the operator doesn't need to work quite so hard to keep the machine in its highest performance zone."
An operator attraction
Joystick controls have the added value of being easier to maintain. "Joystick handles that are running hydraulic controllers are all completely sealed," says Moore. "There's no maintenance, no servicing involved. You don't have any adjustments or greasing."
They can also offer an indirect benefit by enabling you to attract and retain those difficult to find employees, especially younger operators who may be familiar with joysticks used to control video games. "They usually have more experience with joystick controls," says Moore. "They can get acclimated to these types of controls in a skid-steer loader more quickly compared to an operator who has run a machine with traditional controls for a lot of years."
Operators familiar with traditional-style controls may find it more difficult to get used to joysticks, and may opt for the original control style. "That's why we build skid steers with both types of controls," Moore points out. "We have not abandoned the original style. We're just making joystick controls an added feature for those customers who want it."
The percentage of contractors opting for joystick controls is trending upward every year. They are especially gaining popularity in larger, higher-horsepower models. "The larger the machine, the more likely it is to have a joystick," says Moore. "In the smaller size machines, it doesn't seem to be as predominate."
In part, this is because joystick controls are typically an option that will add about $2,000 to $3,000 to the overall cost of the machine.
"The cost of our selectable joystick control is the same no matter what size machine you purchase," says Fitzgerald. "But it has less impact on the overall purchase price of a larger, more expensive machine compared to a smaller one. Also, on a more expensive machine, contractors are more willing to spend the extra money because these machines tend to be utilized in more of a production-based environment. A contractor may get 8, 10, 12 hours of work done in a day. A smaller unit may be used as more of a utility machine, where workers only utilize the loader in between doing different tasks.
"Larger machines also have more weight and horsepower," he continues. "A machine equipped with joystick controls will be less fatiguing to an operator over a long period of time, and that operator is more comfortable."
"It gets down to comfort - to ergonomics," Moore agrees. "When a machine is equipped with a joystick, it's easier to operate. It's less fatiguing. That's the big factor. A customer/operator can be in the machine for more hours. It takes a lot more effort manually pushing levers a longer distance, plus using foot pedals simultaneously. Yes, there is an additional cost [for joystick control], but it's an investment for higher productivity."
Adapting to the market
Even with the growing popularity of joystick controls, production of skid-steer loaders with traditional mechanical controls isn't being abandoned. And manufacturers continue to provide enhancements to these models, as well. Features such as low-effort servo hydrostatic controls are now standard on most machines equipped with mechanical levers.
Servo controls in a skid steer act similar to power steering in a car, says Gregg Zupancic, product marketing manager, John Deere. "Without power steering, turning the wheel would be very difficult," he notes. "Servo controls in a skid steer allow fingertip operation to drive a machine that would otherwise be much more physical to operate due to the weight of the machine, application or load."
The payoff is increased operator productivity. "They reduce the effort needed from the operator so he can be in the machine for longer periods of time to be more productive throughout the day," Zupancic points out. "And they increase controllability to make novice operators good and good operators better."
Servo controls are particularly beneficial in larger, heavier skid-steer models. "On smaller machines that are lighter and more compact, you may be able to utilize purely mechanical levers. They are less expensive, and contractors who are price-conscious may be willing to sacrifice comfort," Zupancic comments. "But as the machines get larger, manufacturers offer servo assist to make it easier to operate. When you get a skid-steer or track loader in muddy conditions, it's a lot harder to turn the machine. With mechanical linkage, a contractor would be straining in that application. The machine becomes heavier with mud that comes around the wheel wells.
"The heavier a machine gets, the harder it is to steer," he adds, "so you have to offer some assistance."
The industry is continuing to move forward with different setups for owners and operators to utilize, Fitzgerald indicates. "Contractors state that finding and keeping operators is more and more of a challenge," he says. "That's what has driven us as a manufacturer to develop different controls. We're trying to adapt to the market to make their operations more efficient."
Even More Control in Future Looking down the road, the implementation of joystick controls on skid-steer loaders has the potential to bring a host of other benefits. Take Bobcat's new remote control option, for example. It's available as a kit that can be added to all-wheel-steer models, and also skid-steer and compact loaders equipped with joystick controls. As it relates to construction applications, Gregg Zupancic, John Deere, expects joystick controls will open the door to even more performance-enhancing features. "Long term, you may be able to push a button and have an attachment such as a bucket automatically lift to a certain height," he says. "For example, you could set the height of the arms for unloading pallets. This is something that would be more difficult to do with a mechanical system. "Your only limitation is your mind," he continues. "You can integrate push-button technology so all an operator has to do is push a button and have the boom and bucket return to the dig position that you have preset. These are some features that are offered in excavators and larger equipment. But now they have the potential to migrate into skid-steer and track loaders. Joysticks become more of an enabler for productivity features than mechanical levers." |