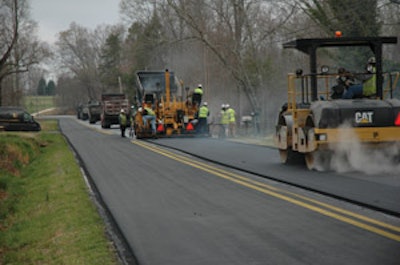
During the week, State Road 9 north of Dahlonega, GA handles average traffic levels for a rural state road, but on weekends this scenic windy road takes a pounding as motorists head for mountain vacation homes.
The increased traffic levels have taken its toll on the asphalt structure, causing surface stresses compounded by more severe full-depth structural problems. Georgia Department of Transportation felt it was time to correct the structural problems and also improve the overall road integrity and ride earlier this year when it contracted with C.W. Matthews Contracting Co. to repair and improve a 10-mile section of the road from Dahlonega north across the Chestatee River.
"It's a two-lane rural state road with an average width of 22 feet, and it's wider on some of the curves," notes Marty Booker, general superintendent in charge of Matthews' interstate and other major highway paving projects. "Our biggest challenge on this project is maintaining safe traffic flow since there are a lot of hills and curves to navigate for our paving crews, the truckers supplying the asphalt and the motoring public that rely on the road."
To prepare the road for its new surface, Matthews, a 60-year-old contracting firmed headquartered in Marietta that specializes in road construction, bridge construction and commercial site work, contracted with the Miller Group to address the full-depth patch work required to fix some of the structural problems identified during the DOT's road analysis.
"We use a pavement evaluation system to visually inspect our roads on a regular basis," notes Chuck Davis, GDOT Area 4 engineer. "On this particular stretch of SR 9 we were beginning to see some load cracking, transverse cracking and edge distress. It's a road that has experienced increase traffic levels, with approximately 10-percent truck traffic. The road receives increased usage during the summer from tourists and recreational campers. It was just time to correct some of the structural problems, as well as the cross slope and rutting."
"We were required to mill out a full four inches of the original asphalt, and in some places that took us down to the subbase material to correct some of the pavement failures the DOT identified," Booker says. "Our milling crew was tied up so we subcontracted that work with another contractor. It took four days to complete the patching work and we used 3,600 tons of asphalt to reconstruct those areas before applying a leveling course."
Booker's paving crew was then able to take over and apply 3,000 tons of 9.5mm Type 1 mix with a PG 67-22 binder to level the road in preparation for a final surface course.
"Most of the leveling had to be done around the full-depth patching areas, with some additional spot leveling as specified by the DOT," Booker says. "The contract called for 45 pounds of leveling course per square yard, which is a little less than a half-inch-thick mat."
Placing the leveling course required three days to complete and then work began immediately on placing the 1 1/4-inch surface course.
"We used a Type 2 conventional F mix design constructed of 9.5mm aggregate with some 89 stone (able to pass through a ½ inch screen) along with the same PG 67-22 binder," Booker says. "It took us three days to complete the northbound lane and we expect it to take another three days to complete the southbound lane. It will take another three to four days to complete all the driveway approaches along the 10-mile stretch."
All 11,000 tons of surface mix, along with the patch and leveling asphalt, was produced at the contractor's Dahlonega Astec Double Drum plant.
Matthews maintained its tight completion schedule, as well as the quality of the final pavement on the SR 9 project, by using a Blaw-Knox paver, a Cat 634 breakdown roller, a Cat pneumatic roller and a Cat 534 finish roller. The $2.5-million project specifications call for a compaction density of 7 percent air voids, as well as ride smoothness requirements.
"We were given 60 days to complete this project from the time we started it," Booker says. "We also have three days to cover any milled portion, 30 days to complete the shoulder work and 15 days to complete striping once the pavement work is done. The contract also calls for milling any portion of the project that does not meet required smoothness specifications."
The Matthews' difference
Matthews has a strong 60-year tradition as a leading road contractor in Georgia, placing more than 5.5-million tons of asphalt annually. The company has received numerous awards for quality pavements.
Matthews has a long and successful history of performing roadway reconstruction in congested urban area. The demands of adding high occupancy vehicle lanes, with the majority of the work performed at night requires a high-level of experience and coordination to safely execute projects in a cost-effective and timely fashion. Maintaining multiple lanes of traffic at interstate speeds while construction progresses requires experience in advanced traffic control techniques. Preplanning, job knowledge and a dedication to safety are trademarks of the Matthew's approach to urban road rehabilitation.
Delivering a smooth and safe ride for the traveling public is paramount for every project the contractor bids on and is awarded. Adherence to exact tolerances, proper design of paving material, and consistent quality control are essential for meeting the ride standards motorists and taxpayers demand.
The company's asphalt construction division performs numerous types of asphalt milling and placement operations throughout Georgia. Its internal quality control measures insure that all 27 plants continue to produce quality hot mix asphalt at the lowest possible price.
The company's production and quality capabilities are further bolstered by the fact that it maintains a fleet of more than 800 pieces of construction equipment. Matthews maintains a technological edge by upgrading equipment every four years and keeping its fleet in top running order with a staff of professionally trained mechanics and 25,000 square feet of maintenance facilities.