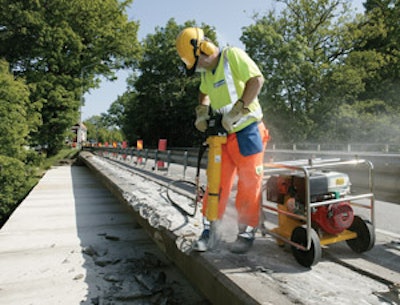
"Ergonomics" has become a common buzzword when it comes to equipment design, and demolition hammers are certainly no exception. In fact, regulations in Europe have mandated a focus on ergonomics for various types of hand-held tools.
"The European market has laws regulating both the amount and duration of vibration that an operator can be exposed to during a working shift," explains John Vogel, vice president of sales - hand-held tools, Atlas Copco Construction Tools LLC. "Because of this legislation, private companies have been forced to conform to the standards."
Although no such standards yet exist in the U.S., the growing concern over the risks of prolonged exposure to vibration is causing many manufacturers to look to the future.
"Some forward-looking companies have sought ergonomic solutions to protect workers from noise and vibration, with the added benefit of increasing productivity from the workforce," says Vogel. "A tool that is less fatiguing helps a worker accomplish more in a single work shift."
The reason for regulation
The primary risk associated with long-term use of hand-held equipment is hand-arm vibration syndrome, an industrial injury triggered by continuous exposure to high levels of vibration. The most common variant is vibration white finger, sometimes called "dead man's hand" due to the white, dead-looking condition of the fingers.
"White finger is what happens when your blood vessels become very narrow," says Rebekah Gallert, product manager - demolition, Wacker Corp. "In a very minor case, you may feel tingling in your fingertips, maybe a loss of feeling at the ends. Worst-case scenario - which I don't think is very common, but could happen - is you will have to lose a finger altogether."
Due to their higher vibration levels, demolition hammers have historically been viewed as a common culprit. "In some severe cases, the vibrations from running these breakers over extended periods of time could actually cause nerve damage and the loss of feeling in the operator's fingers," says Jonathan Cook, key account manager, Chicago Pneumatic Construction Tools.
And the affects are cumulative. "So though you may only work a couple of hours a day or once a week [with the tool], all those affects start to add up," says Gallert.
In 2005, Europe took regulatory steps to mitigate the risks of vibration exposure. The regulations set a limit on the vibration level a worker may be subjected to over an eight-hour period. If a tool's vibration exceeds 5 meters per second squared (m/s2), the employer must limit and document its use.
"For the contractor, it has huge implications because it affects their productivity," says Gallert. "If they're using a tool that is, say, measured at 10 m/s2, they may only be able to work an hour in a day. Then they have to rotate operators, and they have to keep track of all this and document it for the regulations."
The closer the tool is rated to the regulated limit, the better. "If a manufacturer can get a tool down below 5 m/s2, then [contractors] can operate it for eight hours in a day," Gallert states. "If the tool is below 2.5 m/s2, then [contractors] can operate it all day and they don't have to document it."
Getting a handle on vibration
It seems only a matter of time before the U.S. follows Europe's lead. Fortunately, many demolition hammer suppliers are well ahead of the game. Most either market the same hammers here as in Europe, or offer a choice between standard and ergonomic models.
The emphasis has been primarily on handle designs. "For hand-held breakers, the key ergonomic improvement is the introduction of spring-loaded handles that reduce tool vibration for the operator," says Cook.
Nearly all manufacturers offer some form of shock mounting in the handles. However, some companies have taken this a step further. For example, Atlas Copco's LH Series hydraulic hand-held breakers are available in ergonomic versions with a patented four-spring E-handle said to reduce vibration by up to 71%.
Bosch has taken a similar approach with its new 35-lb.-class "JACK" 11335 breaker hammer. When using breaker hammers, operators often use their elbows to brace themselves, notes Randall Coe, head of marketing, North America, Bosch Power Tools and Accessories. This can actually accentuate vibration back to the user.
To counteract this affect, Bosch has introduced the Active Vibration Reduction handle. "It's a handle that moves on a spring mechanism," says Coe. "The tool is going up and down, but the arm is staying steady because there is about 2 or 3 in. of movement in the handle.
"It reduces vibration in your elbows, hands, forearms, so it allows you to use it longer," he states.
The new unit also has a 360° assist handle. "The handle spins around in a circle around the tool on the tube, but it is also adjustable 360° around," says Coe. "There are two levels of adjustment to give you the best comfort based on what you're doing." The combined two-handle design is claimed to reduce vibration by 40% over comparable models.
Internal controls
Some manufacturers have taken vibration control inside the hammer itself.
Consider DeWALT's 68-lb.-class D25980K pavement breaker. Its SHOCKS - Active Vibration Control system combines shock-mounted, rubber-coated handles with a counter-balance mechanism within the barrel of the tool. "We have patented a system that uses two giant torsion springs with a counter-balance mechanism in between," explains Eric Bernstein, group product manager for concrete products.
According to the company, the system reduces vibration by 65% compared to other breakers in the same size class. The result is a vibration measurement of just 6.6 m/s2.
Wacker Corp. chose to isolate the entire upper housing on its 60-lb.-class gas (BH24) and electric (EH27) breaker models. "As the tool goes up and down, the lower percussion system goes up into the housing, but the actual housing is suspended at four points," Gallert explains. "So it's not just the handles that are suspended, it's the whole upper mass."
Isolating the upper housing reduces vibration not only to the hands and arms, but to the entire body. "So even if they lean into [the tool] with their body, which is very common, they're not going to feel much of that vibration back to them," says Gallert.
The breakers also incorporate a heavy-duty spring on the top part of the housing to further minimize vibration.
The payoffs
One of the biggest marketing challenges for demolition hammer suppliers has been getting users to understand that less vibration doesn't mean less power.
"There has always been this correlation, historically, that the more productive I am, the more the tool is going to vibrate," says Bernstein.
Consequently, when low-vibration hammers were first introduced in the U.S., they encountered resistance. "[Users] would complain that the tool doesn't hit as hard as everyone else's only because they didn't feel that vibration back to their bodies, and they have this perception that vibration equals power," says Gallert.
This perception is changing. "It's just within the last year or two that we're starting to get people to realize the benefits," says Gallert. "After they use the [hammer] all day, they see that the tool is working, they're getting the job done and at the end of the day, they feel much better."
Another obstacle has been cost. Vibration-dampening technology does, in some cases, increase the price of the tool. "But it's important to weigh the costs with the benefits you're getting down the road," says Cook. "On the one hand, productivity is immediately increased. And there is certainly a benefit down the road with the workers. Workers' comp incidents or claims shouldn't be as prevalent."
Ironically, when it comes to low-vibration hammer designs, productivity may prove to be the determining factor, not operator comfort.
"A lot of times the guys that are buying the tool aren't the ones using it," Bernstein points out. "What we found is these guys are really paying for productivity all day long. If the tool is more comfortable [to use] because we've taken the vibration out, then the user doesn't have to take as many breaks during the day. So a pretty interesting added benefit of the lower vibration is the added productivity that results. "That," he says, "is something the guy who's buying the tool is willing to pay for."
Getting Size Right
When it comes to ergonomics in demolition hammers, vibration typically receives most of the attention. Yet, there's more to ergonomics than vibration.
"I think that contractors are taking more and more notice of what reduced-vibration hammers could do for them," says Jonathan Cook, Chicago Pneumatic Construction Tools. "And another issue that people are recognizing is the need to use the proper size tools."
Many of today's demolition hammers offer substantially more hitting power than their predecessors. For example, Chicago Pneumatic's new generation 40-lb. CP 1210 delivers 90% of the hitting power of a 60-lb.-class breaker. "So people are noticing that they can use a 40-lb. breaker and still get excellent production - and significantly reduce fatigue in the process," says Cook.
The JACK 11335 breaker hammer has the power of a 68-lb. breaker, asserts Randall Coe at Bosch, yet weighs only 40 lbs. "Because it's about 25 lbs. lighter, this JACK class can be used in a horizontal application, busting up the side of the wall, etc.," he states. "With the assist handle and the weight of the product, it allows it to be a more versatile demolition tool."
Even larger hammers are packing more power into lighter packages. For example, DeWALT's 68-lb.-class D25980K pavement breaker features a bigger, heavier ram that delivers 61 ft.-lbs. of impact energy. According to Eric Bernstein, this means it can deliver the same performance in 7- to 8-in. concrete that comparable models might provide in concrete only 4 to 5 in. thick.
"Our goal on this project was to really bridge the gap between the electric breaker and the pneumatic breaker," he adds.
Ultimately, the benefit is the ability to use a lighter tool to accomplish bigger jobs. "People are getting away from the mentality that you need a 90-lb. breaker every time you have to break up concrete," says Cook. "Ergonomics do wonders for productivity, but simply using the right size tool is also beneficial."