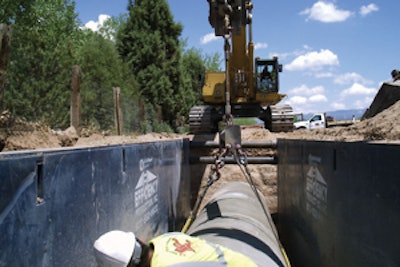
S.J. Lewis Construction, Inc., Waite Park, MN, employs over 400 people and specializes in underground utility work, particularly large-diameter pipe installations. The company was recently awarded a $22 million contract from the City of Albuquerque, NM, to install a new raw water transmission line that will divert water from the Rio Grande to a new state-of-the-art water treatment plant. The plant is scheduled for completion in 2008.
The pipeline portion of the project involves installing 17,500 linear ft. (3.3 miles) of 72-in.-diameter spiral-steel pipe in 40-ft. lengths. Each pipe is cement lined, tape wrapped and mortared. One stick of pipe weighs 32,000 lbs.
In several areas along the route, access is severely limited, especially where it runs along the Paseo Del Norte Highway right of way. In this stretch, the trench needs to be cut vertical mere feet from the road's shoulder and very near adjacent buildings in some spots. With the option of sloping and sheet piling eliminated due to potential vibration damage, a trench shielding system became the preferred option.
"For big pipe lengths, we have frequently used a combination of shorter trench boxes, sometimes abutted with arch spreaders," notes Kenny Zajac, S. J. Lewis' project superintendent. "For this project, however, it's so much faster and easier to have a complete open-span shield in order to lay the 40-ft.-long pipe completely horizontal, with no obstructions, spreaders or arches in the way. Essentially, we don't have to adjust the angle of the pipe when we are laying it, or walk it under arches."
Soil conditions along the trench also proved to be an issue. Trench depths range between 15 and 17 ft. in loose soil. "With the fast-moving, sandy ground, many times a trench box is the only way to get the trench down to grade near adjacent structures, and certainly it keeps all the workers safe," says Kevin Collins of Boyle Engineering, the project's design engineering firm.
To obtain a trench box that would meet the requirements of the project, S.J. Lewis contacted United Rental's Trench Safety Division. United Rentals in turn contacted Efficiency Production, Inc., which is known for its ability to custom engineer and design shoring systems to meet tough project challenges.
Manufacturing a mega-shield
According to Mike West, vice president of engineering at Efficiency Production, the project required "one of the largest, longest steel trench boxes that we have ever designed and manufactured." The end result was a 50-ft.-long, 10-ft.-high steel trench shield with 12-in.-thick sidewalls. To accommodate the 6-ft.-diameter pipe, the box incorporates a five-pipe independent spreader system with 10-ft.-long, 10-in. schedule-120 steel spreader pipe with reinforced side-wall collar oversleeves.
S. J. Lewis is using a Cat 385 excavator to set the pipe and handle the trench shield. A Komatsu PC600 is used on the back end of the box for backfill and compaction.
John Brown, safety director for primary contractor Bradbury Stamm Construction, Albuquerque, notes, "With those 40-ft. joints of pipe, there are spots where they just could not do this without that 50-ft. trench box. It's keeping adjacent buildings and roads from being seriously compromised, and they're moving less dirt, which saves them time and money."
The pipeline installation was started in October 2005, and is scheduled to be completed by December 2006. However, Zajac, is confident the project will be completed ahead of schedule.