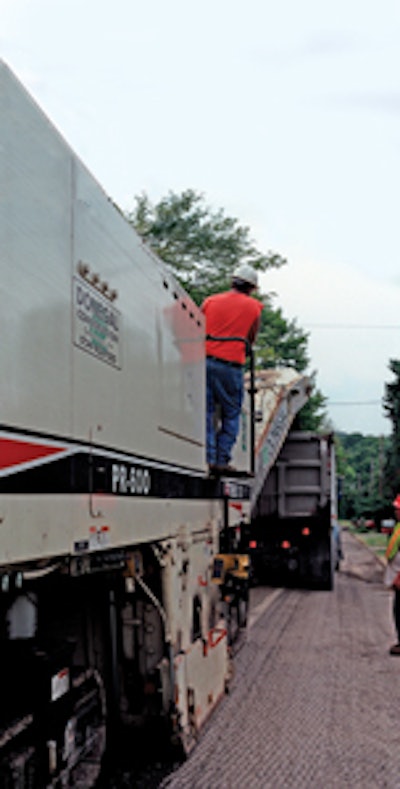
The bulk of the milling machine market consists of half-lane machines weighing from 60,000 to 90,000 pounds and typically equipped with roughly 7-foot-wide cutting drums, which are powered by 600- to 800-hp engines. These machines are productive, efficient, relatively maneuverable and transportable and can chew up a lot of asphalt in a short amount of time. But how do you know if this size unit is right for your application?
Milling machines — or cold planers, as officially designated by the AEM and ARRA — generally fall into three categories: full-lane, half-lane and smaller commercial machines.
Full-lane units typically cut 12- to 12.5-foot swaths, but can grind a path as wide as 14.5 feet. Twin engines routinely power these high-horsepower machines, which can weigh upwards of 110,000 pounds or more. Their niche is sheer production — milling road surfaces as quickly as possible.
Commercial mills fall at the opposite end of the spectrum. Their forte is parking lots, driveways, bridge decks and maintenance work such as asphalt patching and repair, or any job where size and weight can be a restriction. Plus, they are a good match for milling around manhole covers. These units typically weigh less than 40,000 pounds and are equipped with drums 4 foot and less in width.
Half-lane units fill the expanse in between. Their maneuverability and productivity make them a good choice for the bulk of milling jobs, thus explaining their stronghold on the market. They can mill long, wide stretches of side streets and interstates, yet are deft enough to move around many larger parking lots and cul de sacs. For added versatility, some half-lane models can accept drum cutters as narrow as 2 feet or as wide as 12.5 feet.
Evaluate your support system
Knowing when and where to use a full-lane machine is fairly clear cut. "This size unit is basically a big engine driving a big grinding wheel," says John Hood, sales manager for paving and milling products at BOMAG Americas. "It's a good fit when your main consideration is production."
These bigger machines can cut a full lane up to 14 inches deep in a single pass. But because they are so productive, you need to have a support system that can keep up with them, such as sufficient trucks to haul away ground-up asphalt in a timely fashion.
"For optimum productivity, you want to keep the machine cutting at least 40 to 45 minutes out of an hour," says Jeff Wiley, vice president of sales and marketing at Wirtgen. "If you don't have enough trucks to haul the material away, your milling machine will spend valuable time waiting to unload. Some of our larger machines can load 18 to 20 tons of asphalt into a truck in just one to three minutes. If you have a machine that is this productive, and only have three or four trucks to haul material 20 to 30 minutes away, your machine's productivity will be limited."
Also take into account whether you are in charge of those trucks, adds Larry Jack, director of marketing at Terex. "A contractor who doesn't own his own trucks doesn't control their movement," he says. "If you don't have enough trucks to take advantage of the capacity of a particular milling machine, you might want to consider a smaller unit and save money on upfront costs and fuel."
Can you move when you want to?
Another factor to consider when sizing the machine is weight. While the heaviest units are the most productive, some states have very stringent weight laws that can make it difficult to transport the largest machines, especially at night or in colder climates during certain Spring months.
"Weight plays a role because different states have different rules about hauling equipment," says Don Lamb, North American sales manager at Roadtec. "Sometimes the heavier machines require a super-load permit."
"Some of those permits don't allow you to move at night," adds Jack. "That can become a real issue when you're milling all day long and you want to move across town after dark so you're ready for a new job the next morning."
That's when mobility becomes important. Half-lane machines that weigh less than 55,000 pounds are not typically a permitted load, says Lamb. "A contractor can move it day or night, so we see them working a lot of different jobs," he says.
For contractors in northern states, frost laws can affect equipment size, even for larger half-lane units. When the ground is frozen, there is a firm base on which to haul heavy equipment. But in the spring — typically March and April — the weather starts to warm up, creating a thaw/freeze cycle where the ground thaws during the day, then refreezes at night.
"There's a good chance that the frost laws mean you can't move machines, even half-lane millers that weigh 70,000 or 75,000 pounds," Jack notes. "For example, for a Michigan contractor, the optimum machine as defined by weight, horsepower and width of cut might be a larger 75,000-pound unit with a 700- or 800-hp engine and a 7-foot 2-inch-wide cutter. But since he has transportation issues during the spring, his optimum machine might only weigh 50,000 pounds and be equipped with a 500-hp engine and 6.5-foot cutter drum. The smaller unit might not be the most efficient and most productive, but it's the only one he can go to work with and generate revenue with at certain times of the year."
Weight is also a factor when you're milling parking lots, indicates Hood. "There are several half-lane machines that are well-suited for commercial work such as parking lots," he says. "But some lots might only have 2.5 to 3 inches of hot-mix asphalt. A machine that weighs more than 80,000 pounds can do some damage and break through existing asphalt. So the lighter, smaller machines are better suited for this situation."
Important features, options
When you evaluate a particular machine for a job, you will want to consider the four C's: crawlers (track configuration), conveyors, cutter systems and grade controls.
Crawlers: Many milling machines are configured with either three or four tracks. "The difference between the two is essentially preference," says Lamb.
However, Jack identifies one situation where a three-track system can be beneficial. "A four-track system with coordinated steering can run right up over the curb when making a sharp turn in a cul de sac," he says. "This is really the only situation where a three-track machine can be a better choice. Otherwise, it's primarily whatever the contractor feels comfortable with."
Conveyors: Many discussions about conveyors center around machine transport. The option for fold-up systems typically makes more sense on smaller commercial machines rather than larger half-lane units.
"Transport of the half-lane machines is done by trucks with specialized trailers that have a large cradle for the conveyor to rest in," Hood says. "But on the smaller machines, transportation and maneuverability are such huge factors that we strongly recommend a folding conveyor so they can still easily jump on and off a trailer, which they tend to do several times a day."
Cutter systems: Half-lane mills typically have more options for customization of the cutter systems than smaller commercial mills, says Hood. "With our larger mills, you can choose different types of rotating or grinding heads," he says. "There are also profiling drums, which can be useful when the road will be exposed for a relatively long period of time. In this situation, a profiling head — which has up to double the amount of teeth pitched at a slightly different angle — will provide for a much smoother finish. In some cases, transportation departments specify the use of this type of drum."
Grade controls: Contractors have the options of contact and non-contact grade control systems. The introduction of averaging systems is fine tuning both options.
"An averaging system becomes important when the reference point of a contact or non-contact system picks up bumps in the road," says Jack. "The averaging system includes additional sensors — one in front and back in addition to the center — that will average the ups and downs in the road and take out the highs and lows. Some states are beginning to mandate the use of these systems."
Additional features to consider include onboard air compressors to operate tools for changing teeth, generators for powering lights for nighttime work and high-pressure washers to simplify cleanup and maintenance.
"There are a lot of different features on these milling machines," says Wiley. "It's important that they all match for the machine to be its most productive."