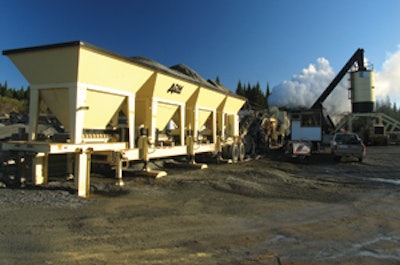
In the asphalt industry, as in most endeavors, good business decisions are almost always the result of solid research. Knowing what equipment to purchase — and when — can dramatically impact a firm's overall productivity and success.
For Conway, SC-based Palmetto Paving Corp., research into which geographic areas were being overlooked by both their company and their competitors, led to the purchase of a new 325 tons per hour (tph) asphalt plant from ADM. While still in its early stages of production, indications are that the new plant will positively impact service and product availability in the area for decades to come, solidifying the company's position as a regional leader in asphalt production.
Increasing capabilities
Established in 1987, Palmetto Paving is today one of the Carolina Coast's busiest asphalt contractors and suppliers. According to Shawn Godwin, vice president and son of company founder Marshall Godwin, the firm has grown steadily, broadening both its range of services and its capabilities.
"We started out with 10 trucks and a single 350-tph plant in Conway," he says. "In 1999, we added a second 350-tph facility in Florence to meet the area's growing demand. This part of the state has seen a huge upswing in development to accommodate the steady rise in population. We've met those demands with a workforce that has increased almost yearly; today we have over 300 employees and operate a fleet of nearly 80 trucks."
With the first two plants, Palmetto's annual volume was approximately 400,000 tons in support of services that include some work for private contractors, but is focused primarily on paving for DOT projects.
Spotting the gap
According to Godwin, their company generally tries to work within a 60-mile radius around each of its plants — initially those in Conway and Florence.
"While looking at sites for possible expansion, we saw an area that had several things going for it: proximity to a good aggregate source, central location for the best coverage and no local production-capable competition. That area, Bishopville, eventually became the site for our third plant."
Palmetto's penchant for research didn't stop with the site selection process but carried over into the decision of which manufacturer's plant could best suit their needs. That research ultimately led to the purchase of the ADM plant (Asphalt Drum Mixers, Huntertown, IN).
"There were several other asphalt producers in the area who already owned ADM asphalt plants and had great things to say about their plants' performance, reliability and consistency. We looked at what other manufacturers had to offer but felt that the ADM plant best met our needs at the time, both in terms of performance and cost. It turns out to have been a very good decision."
Programming production
Palmetto's Bishopville plant, an ADM Milemaker 325, is, by choice, fairly straightforward in design. According to Ted Jacques, plant superintendent; however, it differs from many other plants in the way it handles the processing and loadout functions.
"This plant is fully automated in every sense of the word. What we specified in the programming, however, was that the plant operation and the loadout be treated as separate systems. With those two functions separated, if we experience a problem with the plant, we can continue loading from the silos. If both functions were treated as one, we would be shut down completely. This is a far better way to go."
In addition to separating out the functions, Jacques says they had ADM make an additional modification to the operating program. "In many states — South Carolina being one of them — an asphalt plant can operate in a manual mode if the material produced is used for private work. So we felt it was important to have a system available that would allow us, if the processing program is down for any reason, to override the computer on the plant side, do our private work in manual mode and remain productive."
Going with the flow
Palmetto's plant is equipped with a pair of 200-ton silos for good product availability. The silos feature AR steel-reinforced cone liners to minimize wear and a pneumatically-operated 6,000-pound capacity discharge batcher with anti-segregation dual clamshell gates. High and low material level indicators with silo inventory signal alarms also help improve the loadout process.
Six 30-ton cold-feed aggregate bins allow for easy change of mix designs, which, Jacques says, eliminates the headache of cleaning out bins between mixes. "Each of the cold-feed bins also has a flow sensor on it," he says. "If the flow from any bin stops, we have 60 seconds — and that time frame is adjustable through the program — before the entire plant is automatically shut down, minimizing the risk of running a bad mix."
At the heart of the Milemaker system is a dual-drum configuration, which provides separate drums for drying and mixing. According to Jacques, the system in place at Bishopville has consistently passed emissions tests, primarily because of that configuration.
"In plants that rely on a single drum, the liquid AC (asphalt cement) is injected directly into the rotary dryer with the aggregate and then the entire mixture is heated," he says. "Exposing the AC to both the higher aggregate temperatures and the open flame of the dryer can often result in a ‘blue smoke' situation. We heat stone and sand in the dryer drum, while the mixing drum handles the liquid, fines and other additives.
"As a result, we get the moisture out before any high temperatures hit the asphalt," he continues. "The system we have actually provides the same benefits as the old batch plants; the only gas in the air is the fuel we burn. Everything else is just dust, which the baghouse easily catches.
"We've had days in which as many as 25 state-mandated tests were conducted throughout the day and we've passed with flying colors," he says. "It's been excellent."
Ramping up for growth
According to Godwin, the Bishopville plant is designed for flexibility and versatility to address the 15 or so mix designs SCDOT has in its specs. "While we don't often get involved in that many designs, SCDOT easily can have us alternating between a half dozen or so. This plant makes changing between designs as easy as bringing it up on a touch-screen and making the selection. Our operators really like its ease of use."
Because Palmetto is currently wrapped up in smaller repair projects on some of the major area Interstates, the Bishopville plant has yet to see its first high-production run. However, Jacques says they've had private jobs with runs of 1,200 to 1,300 tons per day (tpd), and they have work on the books for outputs in the 3,000-tpd range within the next few weeks.
"Having the Bishopville location has allowed us to bid on projects that we wouldn't have otherwise been able to bid on in this area," says Jacques. "There's no doubt this plant was built here in anticipation of the larger volume projects. This is a nice opportunity to fine-tune things and as soon as we finish the repair work, we'll be ready to roll."