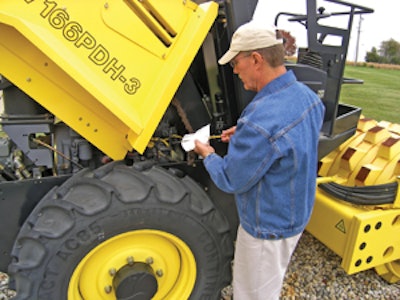
There's no doubt ride-on rollers are tough machines. It's not unheard of to find units 30 years old (or more) still active in construction fleets.
Yet, even these hearty workhorses can be beaten over time due to lack of attention and/or improper operation. It's up to you and your operators to ensure you get maximum life from these machines throughout their duration in your fleet.
Maintain for maximum life
"The primary influence on the service life of the machine is maintenance," says Charlie Detrich, product support manager, Ingersoll Rand. This includes following the recommended service intervals, having trained technicians within your organization, as well as relying on authorized dealers.
Dave Dennison, heavy equipment product manager for BOMAG Americas, Inc., advises following manufacturer guidelines for service to the letter. "This allows the equipment to operate as it was engineered and results in optimum component life," he states.
It's also important to monitor the machine for signs of wear. "Periodic machine inspections should be made to identify needed repairs in their earliest stages," says Dennison. "This will ensure that minor problems do not develop into major issues that lengthen downtime."
Rollers essentially consist of three major systems: the engine, the ground drive system and, in the case of vibratory models, the vibratory system. "The ground drive system is relatively easy. The drum will either turn or it won't," notes Bruce Monical, marketing manager, HAMM Compaction. "If you check your hydraulic reservoir and you have hydraulic fluid and the filter is clean, you're fine."
The vibratory system is a bit more complex. "It is a sealed chamber. It has special grease oil that lubricates the bearings," Monical explains. "As manufacturers, most of us make sure it's a relatively easy check to ensure you have the right amount of fluid to keep it lubricated. Then all you really have to do is change the fluid when the manufacturer suggests you do so."
While this sounds simple enough, you need to be sure to adhere to the recommended fluid levels. "The worst danger to a vibratory system is that you put too much oil in it," says Monical. "The systems are designed to have a little bit of oil vibrating around to lubricate the bearings on the shaft that turns the weight (eccentric). Most of the time, if we have a service inquiry about a vibratory system, it turns out they put too much fluid in it."
Overfilling the system prevents proper cooling. "It builds up too much heat, and heat creates damage," says Monical. "Too little is bad, but too much is also very bad."
Additional areas to monitor on rollers include:
- the condition and level of all fluids;
- any grease points;
- engine oil, air and fuel filters;
- engine and hydraulic oil coolers;
- V-belts, hoses and fittings;
- vibration drum isolators;
- drum scrapers or cocoa mats;
- tire inflation (if applicable);
- any critical safety components, such as the emergency stop button, seat belts, ROPS/FOPS, etc.
Detrich also suggests periodic oil sampling of rollers. "A lot of contractors today use oil analysis as part of their maintenance schedule," he says. "They pull oil samples to make sure their pumps and motors are running at optimum performance. If they can catch [changes] in particulate levels for contaminants up front, it could prevent a costly repair."
Under operator influence
An experienced, well-trained operator can have a positive impact on roller service life. "A trained operator knows the roller well, as well as the materials being compacted," notes Ricardo Perez, regional manager, Southeast Region, DYNAPAC. "An experienced operator can also detect a mechanical problem on the roller and alert the service department before a failure can occur."
A poorly trained or inexperienced operator can have the opposite affect. "Improper operation or abuse can significantly decrease a roller's longevity and is one of the most important factors in influencing a roller's life span," says Perez. "Abusive operation will, over time, result in potential premature failures." For example, repeated misuse of the emergency stop functions will rapidly increase wear on brake and engine components.
Failing to recognize when material has achieved density is perhaps the most common contributor to premature vibratory roller failure. As Monical explains, a vibratory compactor is intrinsically designed to "jump" up and down on material. Material that is not yet compacted has sufficient "give" to absorb some of the shock wave produced. However, once the material has achieved density, all of the shock wave is transferred back into the machine. Continued over compaction of the surface not only wastes fuel, it accelerates wear on the roller.
"When you have energy transferred back to the roller, it's going to cause more fatigue and stress on the structural integrity of the machine," Detrich points out.
Operating the roller at the improper setting can have similar repercussions. In this case, the drum can often serve as a visual indicator of whether the roller has been misapplied.
"A sign of bad practice is when you see uneven wear on the drum," says Anand Chaturvedi, marketing manager for soil compactors, Ingersoll Rand. "Average wear occurs uniformly across the circumference of the drum over a period of time. But if there is something abnormal or uncommon, that will tell you something about how the machine has been used or abused."
Large indentations in the drum can indicate the machine is being used at the wrong frequency or amplitude setting. "Say you're compacting a base material and you really need to be on amplitude setting 2 and you're in amplitude setting 4," says Detrich. "If you continue to beat the same area over and over, you could consequently create damage to that drum — not just externally, but internally, as well."
Indentations can also be a sign the roller is being used for the wrong application. "You might see a smaller size machine on a rock fill application. That might not be the right machine for the task," notes Chaturvedi. "You might need a heavier machine or a larger horsepower machine."
"Probably the worst-case scenario," says Monical, "would be a tandem drum asphalt compactor that accidentally — or on purpose — is used in a rock environment. The drum conceivably could be pitted, and then it's taken back onto an asphalt job. The pits or impressions in the drum will be transferred into that asphalt material."
Crews need to avoid the temptation to make do with a machine not intended for the particular application. "Bear in mind that there is a tradeoff if you are trying to achieve something from a machine that it is not made for," Chaturvedi stresses.
Spot problems early
A daily walkaround inspection of the roller prior to use should be a required part of an operator's job. Monical advises checking to ensure the engine has sufficient oil; the air filter is clean; the machine is fueled and the fuel filter is clean; and the hydraulic filter does not require changing. "It takes five minutes or less to just make sure everything is okay," he states.
The daily walkaround is also a good time to check for signs of oil or hydraulic leaks, as well as any damage to the roller.
In addition, the operator should be trained to recognize signs of trouble during operation. Examples include engine draw down, reduced steering response or low vpm. "The operator needs to have some technical expertise to know if the machine is operating properly," says Detrich. "Has he noticed a lack of performance? If he has, what could be causing it?"
The ability to recognize a decline in performance will allow the operator to report the situation and have the problem checked out before it turns into a much larger problem, Detrich points out.
Dennison adds, "An operator who will recognize and report any machine damage or operational deficiencies found in the course of daily machine inspections performs a vital and valuable function for the contractor."
When to replace?
No machine can last forever. As with other equipment, there comes a point when the repair costs for a roller start to creep up, and you need to evaluate whether its residual value justifies keeping it in the fleet.
"If a roller keeps breaking down on the job and the repair costs are escalating, it is generally a sign," notes Perez.
When an engine or ground drive system fails, weigh the cost of repair vs. replacement. For example, say the ground drive pump will cost roughly $10,000 to replace. "If you put in a $10,000 pump, are you still okay from an asset standpoint?" Monical asks. "If the roller is two or three years old, you might elect to put a $10,000 ground drive pump in and run it another 2, 5 or 10 years. If it's 10 to 15 years old, you may elect not to touch it."
The same holds true if the vibratory system starts to go. "If it was designed to run at 3,000 vpm and it only goes 2,500 or 2,000 vpm," notes Monical, "or if the effective amplitude was .03 and now it's .01 — so the impact force is not as great — do you repair the components because the drum shell thickness is fine, or has it gotten to the point where it's done?"
With vibratory rollers, this question is a little more complicated, since many of these machines are relegated to use as static or secondary rollers once the vibratory system starts to fail. The question then becomes whether the machine is more valuable in this role, or as a trade-in on a new, more productive model.
"You may be able to trade it in and somebody else can repair the pump and use it because they don't use it as often as you would," says Monical. "Then you can take the money and buy a new machine."