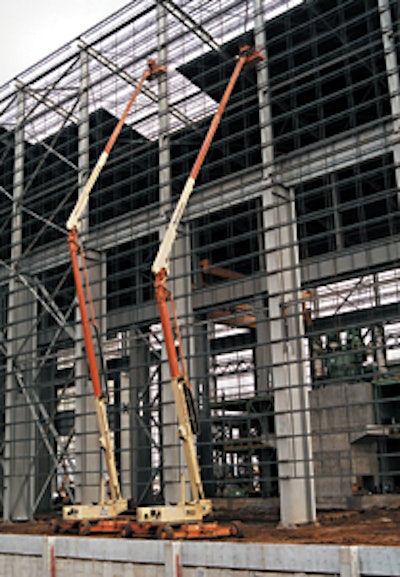
Boom lift safety starts long before a lift on a jobsite ever occurs. It begins with the manufacturers building safety mechanisms into their machines, and continues through to operators, who must take the responsibility to be trained in proper operating procedures.
"Safety is a partnership between the design and function of the machine and the familiarity of the equipment by the operator," says Phil Harvey, product manager, boom products, Genie.
Manufacturer role
Safety on the manufacturers' part involves incorporating safety features into the equipment, ranging from emergency stops (e-stops) to sophisticated electronic control systems.
E-stops, as their name implies, stop all functions upon engagement.
Electronic controls ramp lift functions up and down, from full speed to no speed, by automatically slowing down and easing the operator into the final part of the movement.
"As lifts continue to get higher and higher, operator comfort is a key safety feature," says Harvey. "It's important that we create a level of confidence. These machines are designed to meet all the standards for stability, etc. That's a given. But we want to convince operators that these machines are safe, and to make them comfortable doing their job."
Despite higher lift heights, there isn't necessarily a difference in safety measures that should be taken, says Harvey. "The message we promote is no matter what height you're at, you take on a serious responsibility to do that safely," he states. "In reality, safety is important for a lift that goes up 18 ft. or 135 ft. The basis for safety is still the same."
Many safety features built into lifts perform their intended duty behind the scenes, without ever being evident to operators, notes Tom Hickey, safety training program manager, JLG Industries. In general, ANSI and OSHA require that each cylinder on the machine that supports an elevated load has to be equipped with a holding valve. Although it's hidden from view, it traps oil in the cylinder and prevents the unit from collapsing and coming down in the event of a total hydraulic failure. "Oftentimes, people worry that a hydraulic line blowout would bring down the lift catastrophically," he says. "But with the holding valve, that won't happen."
Other safety features integrated into lifts include foot switches and secondary hand switches that require the operator to depress them in order to activate any of the controls. These comply with a recent revision to the ANSI standards for boom lifts, which mandates certain controls be a two-handed operation to eliminate accidental movement if an operator should fall against a control panel.
Some machines also include detents on the directional controls and boom lift/swing functions to prevent accidental movement, as well as audible alarms that alert operators to dangerous slopes and unlevel ground.
"ANSI requires stability testing and audible warning at 5°," says Richard Hoffelmeyer, vice president, engineering, Snorkel.
Operator role
While manufacturers incorporate safety mechanisms into their lifts, most stress that the main safety "feature" of the machine is an operator who has learned, and implements, safe operating procedures on the job.
"There is no hidden factor that causes accidents," says Hickey. "The basic fundamentals keep operators safe. Safety is about making people aware. The number one safety feature is training."
Operator training is typically available through your local dealer/distributor, or through the manufacturer. Independent associations are another good source of training information and classes.
"According to ANSI, every operator shall be trained in the operation of the machine before he or she operates it," Hoffelmeyer stresses. "It's important to be trained on the basics as well as the specifics of any unit you operate."
Understanding of basic operating procedures starts with reading both the operator's manual and the ANSI Manual of Responsibilities. "If you don't read the manuals, you put yourself, and others, at risk," says Hoffelmeyer.
Manufacturers also stress the importance of performing a walkaround inspection of the machine and an inspection of the work area prior to operation.
The walkaround inspection will enable you to visually identify potential problems with the lift. The operator's manual and the ANSI Manual of Responsibilities offer specifics for each model. But in general, look for any physical damage to the machine, loose or missing parts and any decals that are no longer legible. Check the tires and ensure the lug nuts are secure. Also check fittings and welds, and look for any hydraulic leaks.
The work site hazard inspection allows you to identify potential problems in and around the work area. Check the slope and grade of the ground, as well as ground conditions. Take note if soil conditions are muddy and if there any holes, depressions or puddles. Also look for manhole covers, grills, grates, etc. "Then look around," Hickey advises. "Anytime you see a doorway, sidewalk or stairway, think people. Do the same with trash receptacles and other equipment working on site."
Don't forget to look up for any obstructions, power lines or items that could fall on top of you from a building.
"A common mistake operator's make is they don't look in the direction they're traveling," says Hickey. "It's not usually a problem when they're going forward. But when they go backwards, they don't turn their head to look back. And when they're going up, they tend to look down to see how high they're getting instead of looking up in the direction they're traveling."
In addition to these inspections, a function test, or pre-operation inspection, should be conducted on the lift prior to use. The test should start on the ground. Check to ensure the auxiliary power works in case of a total power failure. Then check all the controls from the platform.
"All machines act differently, so you want to know how your machine stops and starts, and how its ramping reacts," says Hickey. "You want to come to a gradual stop. If you're in a boom that's extended and you're doing a boom swing motion toward a building, you need to know if your ramp will gradually stop you."
Following these steps will significantly increase your chances for safe boom lift operation. Yet, the majority of operators don't. "We estimate that less than 5% of the operators do these four steps," says Hickey. "If more operators would do them, they could eliminate most, if not all, accidents."