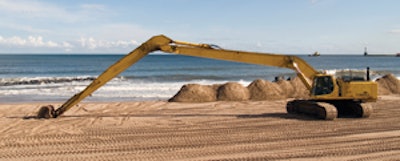
Nine times out of 10, the arm/boom never changes on an excavator," says Michael Boyle, product consultant - excavators, John Deere. Yet, there are situations where added reach is needed, and switching to a larger size class is not an option.
Dredging operations on water are a prime example. Lake Services, Inc., Stafford, VA, is a modest-sized mechanical dredging contractor working off of small sectional barges placed in ponds, lakes, channels and other waterways. Given its typical jobsite, moving to a larger machine is generally out of the question.
"With working on the water, you're faced with a physical constraint," says Martin Firth, owner of Lake Services. As the excavator goes up in size class, a larger barge is needed to carry it. But as barge size increases, any gain in excavator reach is negated. "You really lose a lot of capacity because much of the functional area the machine should work in is actually lost to the deck of the barge.
"The solution is to find an excavator that weighs as much as other machines, but can reach further," he continues. "Therein lies the reason for going to the long reach. It fills the constraint for working on a barge that can't be matched by a conventional, more compact machine."
Advantages of extensions
"Long fronts or super-long fronts can add value for many jobs, including grading over extended surfaces, slope/canal maintenance, barge loading/unloading or light dredging," says Tony den Hoed, marketing communications and product launch specialist - excavators, Volvo Construction Equipment. They are also effective for demolition work at heights, trenching to extended depths, scrap and material-handling operations, etc.
They may also prove more efficient at certain tasks compared to traditional equipment. Again, dredging serves as an example.
"Historically, those applications were handled by a dragline, which was effective, but very inefficient," says Chris Neville, marketing general manager, Doosan Infracore America. "Many customers have said that switching from a dragline to a super-long-reach excavator has reduced the time to clean a retention pond from a week to a day. Moreover, fuel consumption and maintenance are substantially less than a dragline."
Cal Hoffman, co-owner of Kemp & Hoffman, Inc., Denver, CO, began its switch from a dragline to an excavator with a long-reach boom attachment back in 1994. It now owns two Paul Wever Construction Equipment Extendavator attachments, which are typically mounted on a Caterpillar 330L hydraulic excavator. This configuration is used exclusively on drainage projects.
"We clean a lot of ponds and big irrigation canals where you have to have a lot of reach," he explains. "The dragline was getting hard to move around and was pretty big. Some of our jobs are fairly small time-wise, so it was getting inefficient to mobilize it for these smaller jobs."
The excavator with long-reach attachment is now used for sediment removal in small ponds or canals, where the surface of the bank may be too soft to position a machine closer to the work. It also facilitates easier truck loading. "We load trucks a lot because very few of our jobs allow you to stockpile on site," says Hoffman. "So you have the ability to reach not only into the excavation site, but also to the truck, which may not be able to get quite as close without a lot of road work."
Tailor-made alternatives
Specialized long-front configurations are also available tailored to the task. "Material-handling applications may benefit from straight/long fronts, where the working envelope is mostly above ground vs. digging below ground level," says den Hoed. "If a grapple or magnet is used, a special material-handling arm can make for more effective operation."
Two-piece booms (mounted to the stick) are another, more unique alternative. "This configuration is most popular on our wheeled excavators, which are often used in close quarters — highway jobs, high traffic areas or in urban situations," says den Hoed. "It allows the machine to lift, dig or grade in confined areas with minimal movement of the base machine."
This configuration has several advantages. "It can work around tighter vertical limits — under a bridge or telephone wire, for instance. Maximum lift capacity is more usable because the operator can use either boom cylinder, depending on the need," den Hoed explains. "Also, a two-piece boom can increase safety and comfort."
For example, a rubber-tired excavator is often used to carry concrete barriers. The two-piece boom can bring the weight closer to the wheelbase during travel. "This improves center of gravity and reduces ‘loping' down the road," says den Hoed. "Also, the operator can open his range of vision out to the right-side of the cab when traveling without increasing overall height."
Jack L. Massie Contractor, Inc., Williamsburg, VA, is a heavy highway and site development firm using rubber-tired excavators primarily for finish work behind GPS-equipped dozers. However, the addition of a Volvo EW180B wheeled excavator with two-piece boom and integrated Rototilt attachment has opened up a whole new realm of possibilities.
"At first, we never even considered the two-piece boom" says Scott Massie. "All we were considering was the Rototilt attachment."
However, the excavator brought in by Volvo dealer McLung-Logan for a demo featured a two-piece boom configuration. "We started realizing how versatile the Rototilt made the machine, and how well balanced the machine itself was," says Massie. "And then we started picking up heavy loads and we realized we could take that two-piece boom and move our center of gravity more toward the rear and center of the machine, rather than out on the front. That was a tremendous benefit to us — it allows us to pick up heavier items."
Visibility to the right side of the machine is also greatly enhanced. "You can see out of your side window much easier because you can get the boom out of the way," says Massie. This allows for improved safety during operation.
The two-piece boom/Rototilt combination has reduced labor costs, thanks to attachments acquired with the package. These include two buckets, forks, a grapple and an asphalt cutter. "Laborers would have been jackhammering on the ground. Now we're doing it with the asphalt cutter on the Rototilt," says Massie. The forks eliminate the need to manually load materials into a bucket. And the clean-out bucket turns 360°, enabling the excavator operator to "chase" dirt for more efficient bucket loading.
Even the excavator blade reduces labor. "If you can't get something into the bucket, instead of a person shoveling it in, now I just pull it into the blade," says Massie.
The two-piece boom and Rototilt package have expanded the machine's versatility, enabling it to be used for jobs not previously considered. For example, the hydraulic grapple allows for material-handling tasks. "Now we can drive up and down and get brush loaded up without having tracks on the street," Massie states. It also facilitates debris cleanup around buildings.
Overall, the boom/attachment combination has produced a more flexible and versatile tool. "In one machine," says Massie, "we are getting two to three machines out of it."
The trade-offs
Clearly, a long-front configuration can offer benefits for applications requiring extended reach. Yet, there are trade-offs to consider.
"Excavators are multi-faceted tools, and the utility of the machine can be enhanced to suit different operating conditions," says den Hoed. "But changing the boom/arm configuration alters performance, and basic trade-offs occur. The most common trade-off is reach (or working envelope) vs. digging/lifting capacity."
"Generally, you can say the longer the stick, the smaller the bucket," adds Boyle. "The smaller bucket keeps the machine stable without adding additional counterweight."
When adding reach, the size of the bucket must be reduced to maintain the balance, or stability, of the excavator at full extension, Wever points out. "If you lower the capacity of the bucket, you can maintain the same load rating of the machine," he states.
On the surface, this may seem as though you're sacrificing productivity. But this is deceiving. "If the size of the bucket is too big," notes Paul Wever, Paul Wever Construction Equipment, "it will slow the cycle times and you will move less material at the end of the day. There is a ratio you have to take into consideration."
Still, cycle times are likely to be slower compared to a standard boom/stick configuration. "The balance of the machine is changed by moving the bucket/load further out," den Hoed explains. "Cycle time can increase due to lower digging forces and because the bucket travels a longer distance."
There can also be an impact on machine longevity. For example, additional counterweight may be required with some configurations. The added weight can place more stress on the excavator swing motor and other components.
There are further stresses placed on the arm, as well. "A longer boom or arm will see higher bending forces and torsion loading," says den Hoed. "A manufacturer can try to combat this in the design of the long arm. But at some point, the added weight and cost will outweigh the gains."
Of course, purchase price is also a consideration. A purpose-built long-reach machine will require a higher investment compared to a standard excavator. Even long-reach attachments — which tend to be a fraction of the cost of a new machine — require a fairly significant investment above and beyond the cost of the carrier. There can also be long lead times if customized configurations are required.
When determining whether a long-reach arm is appropriate for your applications, it's important to weigh these trade-offs against the capabilities you can gain. Your local equipment dealer can work with you to determine the most reasonable and cost-effective option for your particular situation.