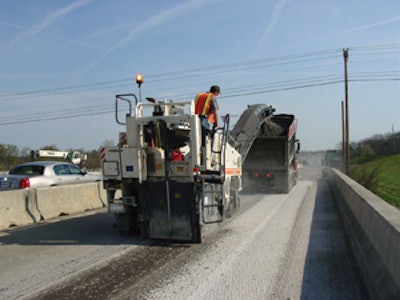
It's hard to imagine a piece of equipment that works harder in tougher conditions than a pavement mill. These tireless machines grind away all day long under load, at times removing more than a foot of asphalt as they trudge ever forward. In the process, they're generating debilitating heat and abrasive silicon dust, all potential roadblocks to performance and productivity.
So how does one maintain a machine that cost anywhere from $300,000 or more for intermediate models to upwards of $500,000 and beyond for high-production models? How does a pavement contractor optimize its performance so a project stays on schedule? The answers lie within a rigorous preventive maintenance program and daily inspections.
"We recommend that contractors clean, lubricate, and inspect their machines at the end of every day," says John Hood, manager of product development and sales for Bomag Americas paving products located in Kewanee, IL. Bomag manufactures five pavement milling machines on 300- and 600-hp platforms. The 300-hp platform features models with 24-, 40-, and 48-inch drums.
Hood notes that by completing daily maintenance at day's end, most any repair issue discovered during inspection can be rectified prior to starting the project the next morning. The evening maintenance regimen, he adds, should begin with a thorough washing – with special attention given to the cutter drum and both the top and bottom conveyors. "The drum works like a garden tiller, except instead of cutting through soil it is cutting through asphalt," Hood says. "Maintenance personnel should check the cutting tools to make sure that none are broken and that they're wearing evenly and then inspect the spray bars to make sure the tips are not plugged. The spray bars both lubricate and cool the tools and if they're plugged, operators will likely burn up cutting tools."
After pressure washing the conveyors, he advises contractors to slowly turn the belts to inspect them for tears or other imperfections. "It takes anywhere from four to six hours to replace a belt," he adds. "Again, contractors would rather take the time to make the repairs at the end of the day rather than be forced to replace the belts when they should be milling."
Lubricating up to 30 grease points follows a complete wash-down and visual inspection of the machine and provides an opportunity to check all seals and bearings for leaks and possible failure. Tracks should also be inspected to ensure that pads are in place, and then adjusted once a week. This, of course, is above and beyond checking the oil and following the manufacturer's recommendation for cleaning and changing filters, Hood emphasizes.
"Pavement milling machines are very simple to run, but hard to maintain," he adds. "A pavement contractor can invest $350,000 for our 4-foot commercial mill and rental rates can vary from $3,500 a day to upwards of $5,000. These machines get tough jobs done in a hurry, but they need daily maintenance to ensure top performance."
The heart of the machine
"There's no question that the number one maintenance item on any size pavement milling machine is the cutter drum, says Jeff Wiley, vice president of sales and marketing for Wirtgen America Inc., Nashville. "Giving the cutter drum and its tools a spot check throughout the day and during the daily maintenance regimen is paramount to keeping the milling machine in top performance. Improperly maintained drums may also cause excessive vibration and machine wear."
Wirtgen manufactures 17 pavement mill models that range in drum size from 14 inches wide on the cut to 14.6 feet. Wiley explains that the company's 4-foot drum has 115 cutting tools that on average will last anywhere from one to three days depending on the application. The tools have a carbide tip and steel body that absorbs the shock, and are secured in a holder that allows them to rotate to wear evenly and retain their sharpness. "Tools should be checked at the end of the day, after the drum has been washed, and replaced if one breaks during the milling operation," he says. "If one breaks while milling, operators will notice a white line or high ridge in the pattern of the cut," adding that this is just one reason to be observant during the milling operation.
Enhancing tool life
Individual cutting tools cost from $3.00 to $6.00 per tool. If a drum has between 150 to 180 tools or more, it doesn't take long for a tool set change to add up to some real dollars. If tools are not changed in a timely fashion, though, and the holder receives excessive wear, the cost suddenly shoots up another $15.00 to $25.00 per tool (the cost of a replacement holder).
Sandvik Mining and Construction manufactures a complete line of cutting tools for pavement milling machines. As product specialist Rick Kant points out, the company offers six different carbide tips and various body types to match the application.
To maximize tool wear, he advises operators to first match the tool to the machine and application. "For example, you probably wouldn't use the same tool on a 900-hp machine that you would on a 450-hp machine," Kant says. "The 450-hp difference would require a more durable tool on the larger machine, and too large a tip diameter on the lower horsepower machine would reduce forward speed and production."
The material being milled makes a huge difference, too, he adds. "Abrasive material accentuates steel body wear on the tool whereas harder material deteriorates carbide tips more quickly. I've seen pavement contractors go through three sets of tools in a day and I've seen sets last up to five days. It just depends on the material and making sure the proper tools match it."
Kant points out that excessive heat generated from cutting causes the carbide to wear faster, so keeping the tools cool with the water spray is critical. "Nothing wears tools faster than running the machine with no water, even for relatively short distances."
One of Sandvik's most recent tool introductions is its Tri-Spec tool that features a carbide ring brazed into the body of the tool. Kant explains that the ring protects the body from washing out, thus allowing the tool to wear until the carbide tip is fully worn. Tri-Spec tools may cost about 50% more than conventional tools, but in the right application they will outlast them by two to four times.
Kant also emphasizes how important it is for the tools to rotate in their holders. "Worn-out holders, a collection of fine powder in a holder, or milling, especially ‘gummy' asphalt, can inhibit self-rotation. In addition to cooling and lubricating tools, a properly operating water system also removes lose material from holders, allowing the tools to rotate. All of the above put a premium on inspecting the cutter drum not only at the end of the day but during the day whenever possible. If flat spotting on the carbide tips, caused by poor rotation, is caught early enough, it's possible to loosen up and extend the life of those tools."
Kant has another tool-saving tip. "Bits or tools wear differently. Milled asphalt moves to the center of the drum, and tools in the middle third of the drum naturally receive more wear, especially on the tool body, than their counterparts on the outside. When replacing complete tool sets, save some tools that exhibit less wear than others on the cutting drum. Then, if a tool breaks and the gauge lengths of the other tools on the drum are worn down by ¼-inch or more, consider replacing the broken tool with a used one. The move will keep a better pattern and is obviously more cost-effective than popping in a new tool."
Other maintenance tips
Intermediate pavement milling machines, those with 4- to 7-foot cutter drums, are especially popular among paving contractors for repairing and renovating parking lots and bridge decks and performing maintenance cuts in residential areas where machine size and maneuverability are important considerations. As Bomag's Hood notes, a 4-foot commercial mill is also widely used to excavate a 4-foot shoulder to grade, and other intermediate mills are ideal for excavation projects where a simple plunge cut and milling operation will do two jobs – excavate and remove the debris in one operation.
He says that even though intermediate machines are smaller than their large "highway" counterparts, they are still very productive (milling up to 100 feet per minute) and require the same high level of maintenance to ensure optimum performance.
Wiley agrees. "The lower conveyor belt on our mills will generally last a season whereas the upper belt is good for two, under normal wear conditions. But conveyor belts run at 350 rpm and are susceptible to tearing. Operators simply cannot see beneath the pavement surface. It's even more challenging on equipment when milling in concrete where a hard surface is compounded by picking up rebar that can damage a belt or drum among other parts."
He continues by noting that ongoing daily inspection and monitoring is just as critical to performance as is allocating an hour at the end of each day to clean, lubricate and inspect the machine. In fact, many pavement mills operate with a driver and a down person whose job it is to monitor for leaks, adjust the grade, and overall observe a mill's performance.
Adds Hood, continuously inspecting a milling machine, following a daily maintenance regimen, and replacing torn belts, track pads, and broken tools is costly, but not nearly as costly as being broken down on a job for a day. "Maintenance does cost, but it pays back dividends, too."