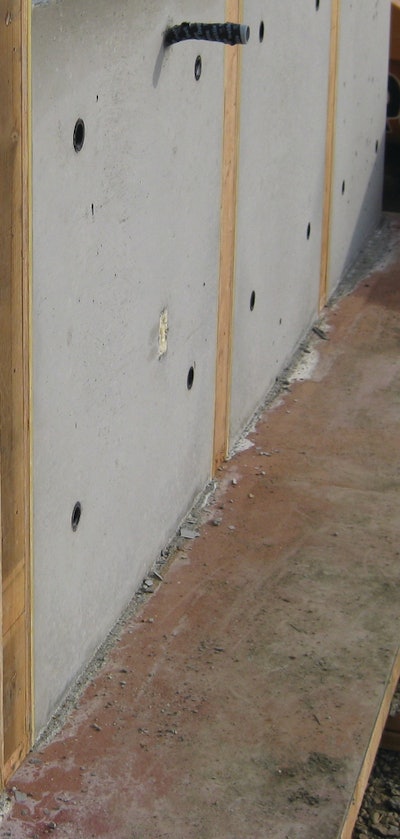
Many specifications require mockups for vertical concrete formed surfaces, regardless of whether or not for structural or architectural concrete. For instance, Section 5.3.3.3 of ACI 301-10, "Specifications for Structural Concrete," contains a requirement for providing a mockup of structural concrete surface appearance and texture. For both an SF-2.0 and SF-3.0 surface finish, a mockup is specified. The ACI 301-10 requirements for SF-2.0 and SF-3.0 are as follows:
5.3.3.3.b Surface finish-2.0 (SF-2.0):
- Patch voids larger than 3/4 in. wide or 1/2 in. deep
- Remove projections larger than 1/4 in.
- Patch tie holes
- Surface tolerance Class B as specified in ACI 117
- Unless otherwise specified, provide mockup of concrete surface appearance and texture
5.3.3.3.c Surface finish-3.0 (SF-3.0):
- Patch voids larger than 3/4 in. wide or 1/2 in. deep
- Remove projections larger than 1/8 in.
- Patch tie holes
- Surface tolerance Class A as specified in ACI 117
- Provide mockup of concrete surface appearance and texture
We applaud the current specification because it gives objective means for evaluating the mockup prior to the start of construction. If the void sizes, projection heights, and surface tolerance requirements are met, the mockup demonstrates a contractor's ability to produce the required surface appearance and texture before work starts. There are no other requirements within ACI 301-10 for final acceptance with regard to the mockup.
Architectural concrete mockups
ACI 301-10 supplies detailed requirements for architectural concrete mockups. However, ACI 310 does not require the mockup but leaves that up to each project specifier. The following requirements in Sections 6.1.3.4 and 6.3.13 dictate a careful approach:
"6.1.3.4.a When required, construct field mockups using same procedures, equipment, and materials that will be used for production of cast-in-place architectural concrete. Field mockups shall be used as a sample of acceptable quality of finished product. Construct field mockups at an acceptable location on site. Provide a simulated repair area to determine an acceptable repair procedure. Repair procedure shall be suitable to provide an acceptable color and texture match. Maintain and protect the mockups until final acceptance of architectural concrete.
6.1.3.4.b For walls, include vertical, horizontal, and rustication joints. Demonstrate methods of repair, curing, aggregate exposure, sealers, and coating. Construct mockup to include a minimum of two lifts having heights planned for placement of architectural concrete."
"6.3.13 Final acceptance of architectural concrete — Upon completion of architectural concrete, final acceptance is based upon matching the architectural cast-in-place concrete with the accepted field mockup when viewed at 20 feet in daylight. Defective Work, including repair areas not accepted, shall be removed and replaced."
The section on acceptance is challenging to contractors because matching the mockup is based on a subjective decision of acceptable quality, with no objective measurements as used for structural concrete. So how should the contractor proceed when building the mockup?
Use the same crew and production procedures for building both the mockup and the structure. If you use a hand-picked crew of your best workers, then tell them to take extra care on the mockup, you're setting yourself up for trouble. There's an old saying that "Most anyone can build a structure that stands up, but it takes an engineer to build one so economically that it barely stands up." That philosophy applies as well to producing a mockup. Given enough skills, time and money, most contractors can build an outstanding mockup. But the goal is to achieve the desired appearance, and nothing more.
If you use new form materials for the mockup, will all new form materials be required for each pour, or can the forms be reused? Constructing the mockup with used forms is more realistic. Even if the mockup is small, always use concrete from two truckloads to provide a batch-to-batch color variation in the approval process. If possible, include one truckload at the lowest slump and longest delivery time (3 inches and 1 1/2 hour) and one truckload at the highest slump and shortest delivery time (6 inches and 1/2 hour). Make sure to repair part of the mockup and get repair procedures and materials approved prior to starting the project.
Finally, don't take mockup approval on a section by section basis. Sometimes architects or owners circle parts of the mockup as acceptable and the rest is not. Get acceptance of the entire mockup or build a new mockup. If only parts of the mockup are accepted, it's likely that only parts of the finished structure will be accepted.
The contractor is first introduced to the specifier's reality after mockup approval: Specifications did not adequately describe what was wanted because the specifier was waiting for the mockup results to decide what was wanted. That’s when the contractor realizes there isn't enough money in the bid to duplicate the specifier’s desired mockup results for the structure. Even if the specifier’s desires were not described in the project specifications, however, acceptance of a request for a change order is unlikely. Too many specifiers, and owners, take advantage of a fixed-price contact after mockup approval to increase the value-added.
Building a nearly flawless mockup, but with efforts that are impractical for consistent replication in a production situation, just gives the owner, architect or engineer a bigger stick to beat you with during mockup approval and final acceptance. That’s the foul up.