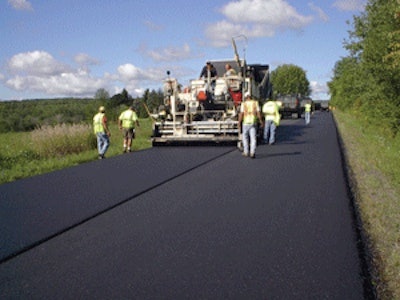
Gernatt Asphalt Products Inc. recently became the first company to use a revolutionary "green" technology in Western New York. This asphalt production technology, known to the industry as Low Emission Asphalt (LEA), is a sequential mixing process that requires up to 50-percent less energy to produce and greatly reduces pollution.
The asphalt was placed on 4.4 miles of Allen Road by Erie County using a Terex 552 paver with a material transfer device rented from Union Concrete & Construction. Compaction was accomplished using two county owned rollers. The mix arrived at 200-210 degrees F and was compacted at 185-195 degrees F.
The project was such a success that Gernatt received an award from the New York Construction Materials Association. The final paragraph of the award reads, "WNY's first warm mix project was truly a GREEN effort. Energy consumption was dramatically reduced, emissions were practically eliminated, the compaction effort needed to get density was reduced and through the efforts of Gernatt and Suit-Kote, it did not cost Erie County anymore GREEN (Money)."
Suit-Kote Corp. provided the chemical additive to Gernatt and installed the necessary plant modification equipment to produce the LEA.
Suit-Kote has been researching, manufacturing, and paving LEA since 2006. Throughout the past few years, Suit-Kote has successfully completed over 40 projects with LEA, including work with the New York State Department of Transportation, and has continually refined and improved the process.
LEA was originally developed by a French company named LEA-CO, and was brought to North America in a 2006 agreement made with Suit-Kote. Under the terms of the contract Suit-Kote Corp. obtained the sole licensing rights in United States and Canada. Gernatt Asphalt Products, Inc. is the first company Suit-Kote has partnered with to produce LEA.
Bill Schmitz, vice president of sales and quality control for Gernatt, was impressed with the ease of production of the new asphalt as well as with its energy savings.
"Even though this was the first time we produced LEA, we noticed that our production capability was not limited in any way and that we burned about 25 percent less fuel than we would making traditional hot mix asphalt," Schmitz says.
Research has shown that an even greater energy savings can be achieved with some small modifications to the plant.
The key factor in making this energy savings possible is the greatly reduced production temperatures needed to produce this product. Traditional hot mix asphalt is produced at temperatures that can exceed 300 degrees F. LEA's final mix temperature is around 205 degrees, thus dramatically reducing the temperature by nearly 100 degrees.
The catalyst of this temperature reduction is a chemical additive that increases adhesion, coating, and workability. These product enhancements are achieved through a sequential mixing process, which foams the asphalt and provides for improved coating of the aggregate stone in the mix.
Allen Road project
After completing a cold in-place recycling of the existing asphalt surface of Allen Road, a 2 1/2-inch 19mm binder course and a 1.25-inch surface course were placed during the recent LEA project in Erie County.
The asphalt applied on Allen Road (8,100 tons of binder and 3,100 tons of surface mix) incorporated reclaimed asphalt pavement (RAP) in quantities up to 13 percent.
"The use of RAP makes the LEA a ‘double-green' technology, because it not only reduces emissions and saves energy costs, but it also combines that with the use of recycled materials," says Professional Engineer Gregory Harder, vice president of McConnaughay Technologies, the engineering and research division of Suit-Kote.
To precisely quantify the emissions reduction, Suit-Kote contracted Upstate New York engineering firm O'Brien and Gere to conduct a comprehensive emissions study. They compared plant emissions from LEA and conventional hot mix asphalt at Suit-Kote's Polkville, NY facility.
The study concluded that LEA reduced particulate matter baghouse exhausts by 51 percent, sulfur dioxide by 46 percent, nitrogen oxide by 21 percent, carbon monoxide by 82 percent, and other air contaminants were reduced by as much as 95 percent.
In addition to reducing air pollution and fuel needed for production, LEA can be used in cooler weather and improves working conditions by reducing smoke and odor.
Reduced aging
The reduced production temperature associated with LEA provides a significant performance benefit known as reduced "aging" or stiffening of the mix. This "aging" reduction is likely to yield a greater lifecycle of the pavement, which leads to reduced costs, thus saving taxpayers money over the long term.
The first North American LEA project was performed in Cortland, NY over two years ago and is performing extremely well. After more than 30,000 heavy truck passes, the pavement looks almost exactly as it did the day the project was completed. To date, over 100,000 tons of warm mix using Suit-Kote's LEA technology has been produced.
In addition to the obvious environmental benefits, this "green" product will not pass along any exorbitant costs to the consumer. Once minor modifications are made to an already existing asphalt plant, the cost of producing LEA will not cost any more than conventional hot mix. Many believe the cost will actually decrease over time as energy efficiencies improve.
Suit-Kote Corp. is a diverse third generation, vertically integrated asphalt company headquartered in Cortland, NY. They have 17 facilities located throughout Upstate New York and Northern Pennsylvania.
Founded in 1921 by Harry Suits, Suit-Kote has evolved into a corporation that employs nearly 700 people and is widely recognized as an industry leader because of its quality road maintenance products and highly skilled work force.
McConnaughay Technologies is a wholly owned subsidiary of Suit-Kote Corp. and functions as its engineering and research division.
For more information on LEA visit www.lowemissionasphalt.com or email [email protected].