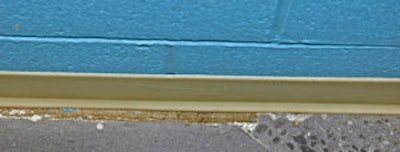
The success of a polished concrete surface doesn't rest solely with the concrete processing steps. Careful planning of the project from mix design through final protection will help a contractor achieve a successful end.
Processed concrete, whether honed to 800 grit or polished to 3,000 grit, is a growing area of decorative concrete. Over the last decade or so, the concrete processing industry has experienced a learning curve, but finally architects, designers and engineers are giving concrete processing the green light on an increasing number of projects. This is an exciting opportunity for concrete polishing contractors and manufacturers of equipment and supplies to prove what they have been saying for a long time - there is no other flooring option currently available that is as durable, has as low a maintenance and life-cycle cost, and can be renewed on site as easily as concrete. Every day I see more and more plans that specify polished concrete over VCT, carpet, epoxy and other flooring materials.
Although concrete processing technology has made great strides in the last few years, I see two problems still facing the industry. First, almost all specifications I see are vague in respect to the installation process, i.e., the actual steps and techniques a contractor uses in polishing a floor. Second, if the concrete has yet to be poured most current specifications do not take into consideration other factors that affect the installation process and final appearance of the floor, such as mix design, placement, finishing, curing, joint placement and protection. Final results of a polished concrete floor are largely dependent on the quality of the concrete a contractor is given to work with. When there is an opportunity to specify these other factors, a floor will turn out significantly better than if only the processing procedure is specified.
Specifying a polished floor
When a designer or architect is specifying a processed concrete floor, the first step is to determine the desired finish. Considerations need to be made for the surface cut, clarity of reflection and decorative applications such as coloring, saw cuts, engraving, seeded decorative aggregate, etc.
After the desired look has been determined, specifications for completion need to be written. For new concrete the specifications start in "Division 3 - Concrete." Within this section you will find the specifications for mix design, finishing, curing, control joint placement, protection and sometimes the processing process. If the processing process is not listed in Division 3 it will most likely be found in "Division 9 - Finishes." Following are some brief points to take into consideration when specifying a "Polished Concrete System."
Mix Design
- Mix design varies from one geographic region to the next as a result of available aggregates and weather conditions.
- If possible, do not air-entrain; if entrainment is necessary do not exceed 3 percent.
- Keep fly ash to a minimum, not to exceed 20 percent of the cement weight.
- Do not use calcium chloride-based accelerators.
- Use a 3,500 - 5,000 psi at 28 days mix.
- When exposing aggregate, understand how the aggregates will look when polished and how well that polish will hold up compared to the concrete's finished surface.
- Final color of dried mix if the floor does not receive stain.
- Final color of dried mix will affect the overall color of stains.
Finishing
- Floor Flatness (FF) above 40 will minimize a wavy appearance in a floor when finished.
- Mechanically trowel the surface to the point right before burning and do not allow the power trowel to run dry.
- In areas that receive hand troweling, make sure the concrete has been well consolidated and troweled as tight as possible.
- If a fine aggregate finish with minimum aggregate has been specified, thoroughly floating and tamping will help bring more cream to the surface.
Curing
- Hardeners/densifiers react with calcium hydroxide to form additional calcium silicate hydrate (CSH). CSH is the material that bonds the cement to the aggregate.
- If a curing agent has to be used, ensure it is water based and UV dissipative. Remember, the hardener/densifier and stains must be able to penetrate the surface for a successful installation. A cream finish cannot be obtained if a cure and seal or tilt-up wall mold release agent has to be ground off.
- If possible, water cure to reduce edge and joint curling. Curled edges and joints will have more exposed aggregate then the rest of the floor when the surface is processed.
- Concrete must be cured for a minimum of 28 days before processing.
Control Joint Placement
- Control joints should be placed so they are not running down the middle of hallways or in highly visible areas if possible.
Installation Process
- At no time should any consecutive grits be skipped following the starting grit abrasive.
- The Installer will drop back one girt resin abrasive from the last metal grit abrasive used. A separation in grit designation size must be a minimum of 50 when transitioning from metal to resin.
- The Installer will refine the concrete surface with each grit abrasive to its maximum potential before moving on to the next consecutively finer grit. The Installer must refine the concrete surface further than replacing the scratch pattern from the previous grit abrasive with the next grit abrasive.
- Application of a densifier will be dictated by the concrete but will not be applied any later than 200-grit resin unless circumstances present themselves and are approved by the architect.
- The surface must be free from any random scratch patterns throughout the process and in the final product.
- The floor must be cleaned between each grit until any particulate grit larger in size than what the next grit cut will produce has been removed from the floor before continuing to the next progressively finer grit.
- All edges must be uniformly cut and processed when compared to the rest of the floor.
- Corrections should be made before application of Impregnating Micro Filming Stain Inhibitor.
Protection
- Diaper all equipment.
- Vehicles and lifts are not permitted on surface if possible.
- Do not allow acids to contact surface.
- Do not place any material onto surface that may cause staining, etching or scratching.
- For concrete that has been processed without satin or any type of sealer, a guard or impregnator, it can be covered with rosin paper, masonite, drywall and plastic in any combination as long as there is no vapor transmission. If the concrete is still curing make sure all joints are taped.
- For concrete that has stain, sealer, a guard or impregnator, it is imperative that it be 100 percent cured before being covered with any material that will not allow it to breath.
Working with the trades
It is important that as soon as a job has been awarded to a general contractor that the GC award the concrete processing to a subcontractor and set up a meeting with the architect, on-site superintendent and concrete processing contractor. If it is new construction the meeting should also include the contractor placing and finishing the concrete, concrete supplier and anyone else who may affect the concrete work.
Currently architects and general contractors have little or no understanding of the processing contractor's requirements for an efficient and successful installation. Processing concrete requires large areas to be clear of debris and free of other trades. It is important to determine when the processing work will be performed so other trades are correctly scheduled. Equipment that runs on electric power often has large power requirements that need to be planed for. On new commercial jobs, temporary power is rarely sufficient.
When processing new concrete the concrete supplier must understand the importance of strictly adhering to mix design specifications. The placement contractor needs to realize the concrete he is pouring and finishing is not a subfloor but the final flooring surface. There has to be a clear understanding of how to finish the concrete to get the best possible results from the polishing process.
There are other intricacies the concrete processing contractor understands that the GC will not be aware of. For example, if the building is block construction the thickness of the felt between the block and pour needs to be considered. In addition, to achieve the best possible finish along edges the processing should be performed before millwork, including door jambs.
Concrete processing should also be performed before painting since the equipment is run tight along walls. The most desirable time for the processor is before any interior walls have been placed although this is not always possible. A word of caution for processing contractors when pricing work - don't assume you will be given the area before walls are placed. As we are all aware, working around walls and tight areas increases time. If the building is block construction you will have to work in hallways, small rooms and tight areas.
Regardless of whether the concrete exists or if it is new, all trades need to be reminded that the concrete will be used as the finished floor and should be treated accordingly.
The time has come for every contractor processing concrete to learn their trade beyond simply going through the motions. We must understand the technicalities of what we do and be able to convey these technicalities to all those who affect the outcome of the processed surface. For those who are specifying processed concrete surfaces it is crucial that you understand what you are specifying. Will your and the customer's expectations be met? General contractors must listen and be willing to work with the concrete processor's needs for an efficient and successful installation.