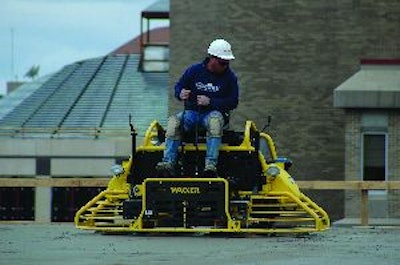
As part of its master plan to redevelop downtown Madison, Wis., the University of Wisconsin-Madison, along with private businesses, has embarked on the 11-story, 1.1 million-square-foot University Square project. The project will consolidate several existing services and businesses at one location. The result is a private-public partnership between Executive Management Inc. of Madison and the university. The new $100 million complex will include 350 apartments, 250,000 square feet of University Health Service offices (known as University Tower), 140,000 square feet of retail space and 420 parking spaces.
Started in 2006, the retail and housing segments are scheduled to be completed in May of this year, with the University Tower portion set to open in December. In all, the project is expected to consume 58,000 cubic yards of concrete.
Given the tight timeline, J.H. Findorff & Sons Inc., the general building contractor, stepped in as soon as the site had been excavated and the retention system was in place. In business since 1890, J.H. Findorff operates offices in Madison and Milwaukee, employs over 500 workers and completes roughly $275 million of construction annually. It specializes in building construction, including educational facilities, municipal and governmental buildings, convention centers, health care facilities and more.
The company started the construction process by using Peri USA SKYDECK for the first three floors then Aluma flying tables for the remaining eight floors.
The SKYDECK system, which can be used on slabs up to 95 centimeters, has stripping that allows you to strike after only one day, depending on the slab depth and concrete strength. The main beam and formwork panels are available for use on the next cycle after two days. “It’s a new technique out for building high-rise structures,” explains Chad Eschler, assistant yard superintendent, J.H. Findorff. “It’s used in Chicago and places like that, but it’s the first time we’ve ever used it [on a structure like this].”
The system was selected for this project because of its ability to facilitate faster completion of concrete structures. “We had a pretty tight schedule, so we needed anything to improve that,” Eschler comments.
Starting to finish
When it came time to finish the concrete floor slabs, J.H. Findorff brought in walk-behind trowels and edgers, as well as two of its 8-foot Multiquip Whiteman diesel concrete trowels.
Although the walk-behinds usually get on the slab first due to their lighter weight, the concrete crews actually prefer to use the larger ride-ons whenever feasible. “The trowels get on the concrete a little bit later, but [the crews] feel they get a better finish doing it that way,” says Eschler. “Or if the concrete starts to get away from them, the heavier machine helps, as well.”
In addition to its existing units, J.H. Findorff had an opportunity to demo Wacker’s newest 8-foot ride-on diesel trowel during the project. The CRT 48-35L was officially introduced at the World of Concrete in January.
Wacker has worked previously with J.H. Findorff to get feedback on new models. “That’s something Wacker has been pretty good about,” says Eschler. “They come to us to demo equipment.”
The CRT 48-35L was kept on the job for over a month. Wacker had hoped to get 10 to 12 hours on it as part of the test. At the time of our visit, it had already acquired 15 hours, and was currently in use on a 500-yard, 14,000-square-foot pour. The largest slab on which it was used, at that point, was roughly 17,000 square feet.
“The guys just love this demo,” Eschler asserts. “[We’ve had] good feedback on it, definitely.”
Easy steering, plus more power
One of the features the operators seemed to appreciate most on the CRT 48-35L is the patent-pending torsion-assist steering system. This system reduces the amount of pounds of force needed to operate the trowel by as much as 75 percent compared to previous models.
“The new torsion bar they put in it makes it easier to operate,” acknowledges Dave Pehl, concrete foreman, J.H. Findorff. “It makes it more like a hydraulic machine.”
“The steering on it is night and day,” he continues. “Our [older units], you have to strong arm them all the time. This one, you can operate almost with one hand.”
The ergonomically designed twin-lever control enables improved maneuverability and feedback from the concrete conditions. Other machine features include a newly engineered clutch and belt, center engine design for better visibility and heavy-duty frame that allows for easy access to the slab edges.
Power for the CRT 48-35L is supplied by a 35-hp four-cylinder, liquid-cooled diesel engine. Rotor speeds ranging from 20 to 165 rpm enable improved panning and burnishing of concrete plus allow for higher production and overall better surface finishing.
“As far as panning goes, it has more power,” Pehl asserts. “It’s easier to operate, and there’s definitely more power there. You don’t bog down when you go to double pan.”
The demo at the university jobsite has proven so successful, Pehl and his crew are encouraging J.H. Findorff to invest in the new models. “We’re trying to get them to buy a bunch of them,” says. Pehl. “The reaction time is just a lot quicker. You can stop it on a dime.”