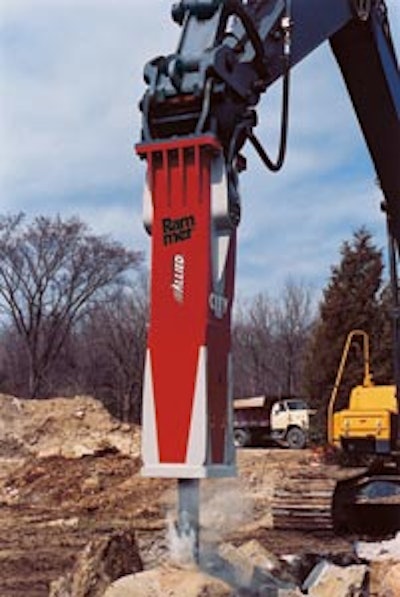
There's been a transformation in hammer design from the inside out that makes these attachments simpler, smarter and easier to maintain, while increasing productivity and longevity. That's good news for contractors who rely on them to handle back-breaking work associated with demolition tasks such as splitting rocks and crushing concrete.
The evolution begins internally, with the advent of fewer moving parts in many new models. In some, you'll find as few as two moving parts. This offers benefits from several perspectives. For one, fewer moving parts mean fewer items that can ultimately fail. "The more moving parts you have, presumably the more seals you have around those parts and the more chances there are for things to go wrong," says Kevin Loomis, hydraulic applications manager at Atlas Copco.
"It also minimizes the high cost of the internal parts and the labor for rebuilding the hammers," adds Roland Jarl at Enterprising Europa, manufacturer of EEI-Socomec hammers.
Plus, moving parts feed off the energy transferred from the carrier. The greater the number of moving parts, the less energy that will be transferred and the less efficient, i.e., productive, the unit will be.
"Every moving part is moved by oil and energy from the carrier," Loomis explains. "Your ultimate goal is to transfer energy through the hammer to break rock. But the hammer will be less efficient when you're moving multiple parts internally."
Reevaluating components
In order to minimize the total number of parts, manufacturers evaluate every component and its function. For example, engineers at Allied Construction Products combined one bolt-on and two pin-on brackets into a single mounting bracket that allows the hammer to be adapted to any carrier or quick coupler. And instead of a series of steel bushings, the company's in-Series hammers feature just one bushing made of composite wear-resistant material, says Al Springer, national sales manager.
Bushings — and their maintenance — factored heavily into Ingersoll Rand's decision to eliminate tie-rods in its light-range hammers. "You have to torque them just right for the hammer to function properly," says Tom Pinchuk, attachments marketing manager at Ingersoll Rand. "And they're difficult to remove and replace."
In many cases, technicians were required to remove the tie rods, disassemble the breaker, pull out the bushing, measure it, replace it if necessary, then reassemble it. "It could take anywhere from four to eight hours to complete the process," Pinchuk says. "We've created a very easy system where technicians just undo a clip that surrounds the breaker and pull out the tool and bushing. The whole procedure takes three to four minutes. And you don't even need to remove the breaker from the carrier, which is especially beneficial if you have a dedicated breaker and carrier."
Many manufacturers are also moving to fully enclosed housings, or cradles, which also eliminate the need for tie rods, tie bolts and side bolts. "The totally enclosed casing eliminates the common bolt problems related to loose side bolts, as well as the wearing of the side plates," says Jarl.
This type of construction also protects the power cell and internal components, as well as reduces the amount of ambient noise created when the internal piston strikes the tool. "With just two side plates, the internal portion of the breaker is exposed to moisture and dust that can seriously impact wear," says Pinchuk. "These hammers are constantly being hit by rocks and flying debris, and they're used in narrow environments where they rub against abrasive surfaces. So it's imperative that we protect the hammer for an extended life."
At Atlas Copco, engineers design components to serve multiple functions whenever possible, says Loomis. For example, most hammers have an internal reciprocating piston that also serves as a battering ram. Typically, some type of control valve moves to direct the oil in the top or bottom of the piston to make the unit function. By removing the control valve and having the piston serve as a battering ram and a gate valve, engineers eliminated one component.
"Reevaluating technology, and taking a look at what actually happens inside the breaker to see how components can be consolidated to serve more than one function, can lower the overall number of components that you need," Loomis adds.
Reducing maintenance
Reducing internal components provides the added benefit of minimizing maintenance, since there are fewer parts that require attention. "Every time you have a threaded fastener, you run the risk of it coming loose or breaking," Loomis notes. "And anywhere a component bolts on, the seal between the two pieces can potentially leak. A more uniform product removes some of the maintenance intensive parts that require servicing and regular inspection or repair at time of rebuild."
Reduced maintenance, especially on smaller units for skid-steer loaders and mini-excavators, is a common theme among many manufacturers. "Through engineering problem-solving capabilities, preventive maintenance has been minimized — and in some cases almost eliminated — which has resulted in lower labor costs," says Springer.
Automatic lubrication systems are becoming more popular as a way to reduce, and often eliminate, daily maintenance associated with keeping the tool steel and bushings well greased. Some models are also sealed to keep lubrication in and contaminants out.
"When there is steel against steel, there is a lot of heat generated. So you need a good lubricant, and a lot of it," says Springer. "Unless you have an automatic lubrication system, operators are required to grease the tool steel every two to three hours. But an automatic lubrication system can take the worry out of lubrication."
Enhancing productivity
In addition to making hammers simpler and easier to maintain, manufacturers have also focused on enhancing productivity and longevity, as well as making hammers "smarter".
Productivity is a function of two factors: impact energy and recycle time. In an effort to optimize both, manufacturers offer features such as AutoControl and energy recovery systems.
Atlas Copco's AutoControl — also known as variable frequency — senses the hardness of the material and adapts breaker output accordingly. This intelligence makes the hammer "smarter" and more productive because it provides only as much power as required for the task. "If you have a very light application and a larger breaker, you probably don't need 100% of the power that the breaker can produce," says Loomis.
Another advantage is less stress on the hammer. "By adjusting the output, you put less wear and tear on the internal components by not exceeding the amount of power needed to physically do the job," Loomis explains. "The breaker will last longer since it isn't getting the physical abuse of running at 100% of its duty cycle all day long."
Energy recovery systems recycle the recoil energy and add it to the next blow. For EEI-Socomec hammers, as much as 15% to 20% of the oil used in a stroke is recovered.
To further enhance longevity, many manufacturers offer blank fire protection to eliminate metal-to-metal contact that can damage a breaker. Additions such as dust shields protect bushings by preventing debris from building up on the tool shaft. And trapezoidal tools are virtually unbreakable and will not get jammed into the material being demolished, according to Allied.
The evolution of hammers has also included a progression away from 100% oil-fired designs. In the case of Atlas Copco, a combination of nitrogen gas and oil are used to fire the piston. "This removes a lot of the burden from the carrier and its hydraulic system," says Loomis. "It increases efficiency because it's not relying completely on the output of the carrier. We can also produce a more powerful unit in a smaller profile, which adds to the overall production."
Ingersoll Rand also utilizes nitrogen in its hammers, but it's contained within an "energy chamber" — a completely sealed chamber with a diaphragm. In its place at the top of the hammer is hydraulic oil that controls the hammer. "Our hammers work completely hydraulically," says Pinchuk. "And with the sealed energy chamber, the hammer won't lose its nitrogen charge, so you'll always have consistent, constant performance and maximum energy.
"Overall, there have been a lot of strides made in hammer design that affect productivity and maintenance," he continues. In the end, they're both related. "By making hammers easier to maintain, the more likely you are to maintain them. That means the hammer will more likely operate at its optimum performance, and will more likely last a longer amount of time."