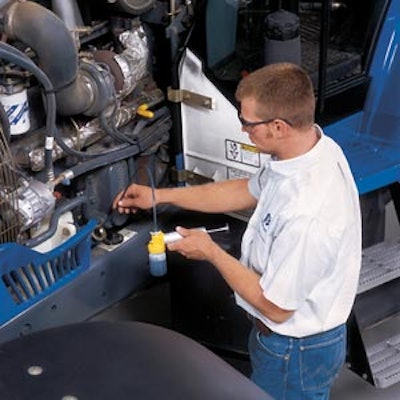
Like any tool, fluid analysis is only as good as the person who uses it. To really take advantage of what it has to offer, you must understand what you are trying to accomplish, be able to interpret the results you are given and be able to act on those results.
"Oil analysis is a tool and it can be used many different ways," says Shawn Ewing, technical coordinator, ConocoPhillips Lubricants. Define what you are trying to achieve. Are you trying to eliminate unplanned downtime? Are you having certain types of component failures, such as engines, transmissions or hydraulic systems? Is it being used as a preventive maintenance tool? Are you evaluating different types of oils? Do you want to extend oil drain intervals? The answers to these questions will help you tailor an oil analysis program to best fit your needs.
"Establishing program goals will drive the proper testing," says Brett Minges, POLARIS Laboratories. Consider extended oil drain intervals. "A test package that monitors contamination and wear wouldn't include the base number and oxidation/nitration test necessary to extending drain intervals. Knowing your program's purpose, and always keeping in mind what you're trying to accomplish, identifies the testing that should be done."
You also need to understand that different goals come with different levels of complexity. Evaluate the goals based on where you are currently. You may have to take a stepped approach to get where you eventually want to be. "If you've never done fluid analysis, start slowly," says Minges. "Let your goals and your current program, or lack thereof, dictate where to begin and at what level. Good analysis programs should help discipline maintenance practices, so be sure to get a good handle on what preventive maintenance means to you first."
Then you have to measure the results to determine the success of the program. "Whether your goals are financial in nature or performance-oriented, you have to establish some benchmarks by which you can measure your effectiveness at reaching them," says Minges. "The good thing about fluid analysis is that it generates data. But how well you manage that data is key to measuring program performance."
If you are new to oil analysis, it's not necessary to do everything at once. "I would not jump in with both feet," says Ewing. "I would pick out some critical equipment and get my feet on the ground."
Junk in, junk out
We have all heard the adage "junk in, junk out". This also holds true with a lubricant analysis program.
"When you are setting up the program, accuracy in documenting the type of equipment, the component and the product being used is all very important," says Dan Arcy, Shell Lubricants. "We have seen samples come in and it will just say Cat. It will not say what engine it is, it will not say the number of hours. It makes it very difficult to give a good evaluation of the oil sample."
The more detailed the information you provide the better. "Engine make and model, hours/miles on the engine, hours on the oil, amount of top-off oil added and the oil name/grade are all vital data points to provide to the laboratory," says Donnie Thweatt, off-highway sales, Chevron Products Co.
Consider the case of a new engine vs. an engine that has a few hours. "If you had a unit come in, and it only had 100 hours on it and iron is at 100 ppm, there would be a concern," says Arcy. "But if it has 400 hours on it and there is 100 ppm, that may be normal." Without proper documentation, you could not distinguish between the two samples.
Identification of the make and model of the engine can be very useful to an oil analysis lab. For example, some Caterpillar engines use copper oil coolers. "If all of a sudden copper spikes at 300 ppm, [our lab] is going to get excited about it," says Arcy. But the lab will know to ask if a new oil cooler was put in. "Copper oil coolers sometimes show extremely high levels of copper for the first couple drain intervals."
It is important to provide the lab with a clean sample of the fluids you are using. "Different oils have different signatures and they use different additive-type chemistry," says Arcy. "Unless you know the signature and the initial viscosity grade of that fluid, you are not going to be able to do as good a job on the analysis."
Consistency adds value
"Consistency in sample collection is critical to success," says Thweatt. "Using the same method for each sample removes variables, making comparisons more informative."
Arcy adds, "With used oil analysis, you are looking for trend changes. You want to be consistent. That consistency needs to carry all the way from the number of hours that you have on it to how you take the sample. You always want to take the sample the same way. The reason it is important is there can be slight variations by going with different methods."
Develop an action plan
Once you receive sample data, you need to be willing and able to take the next step. "One pitfall many new programs have is they go in with great enthusiasm and then all of this data comes in," notes Arcy. "They don't have the system set up to where they can respond to it, or they have the wrong tests, or they have not structured the right program."
This is an area where selecting the right oil analysis partner can be a great benefit. "So you've set attainable goals, taken good samples at timely intervals and provided your lab with all the right information," says Minges. "Now you need the tools to manage what you get in return. Identifying trends that pinpoint small problems before they become catastrophic failures, and using the laboratory's recommendations to affect change in your maintenance practices to avoid those failures, is truly where the rubber meets the road. Your oil analysis laboratory should be able to provide those tools."
Someone in your company must also manage the program. "Responsibility and accountability for the program must be assigned within the organization," says Thweatt. Several key questions must be addressed. "Who will be performing the sampling procedures? Who will be responsible for shipping and handling of the samples after they are taken? Who will manage and enter the data, and what system will be used to store and evaluate the data? Who will make the decision to react to the sample results?"
Make sure the analysis program gets the emphasis it deserves by sending in samples as soon as possible after they are collected. "I have seen where guys will pull samples and they will get put on a shelf and sit there for two or three weeks," says Ewing. "Say for instance that there is a critical condition that arises. The machine has been running two more weeks and nobody knew about it. If it was sent in within a week, you get a little more handle on stopping catastrophic failures."
Some labs today offer turnaround in less than 24 hours from the time they receive the samples, and results can often be instantly accessed online. "Most of the labs have pretty good, easy to follow reporting systems now," says Ewing. "There are various ways they can report results to you, but most people are using the online reporting system right now. The contractor just has to decide who is going to be getting this information and who is responsible for getting it out to the shop if there is a problem."
It's all about trends
"An effective oil analysis program is a long-term approach," says Ewing. Sometimes people tend to over analyze the data when they first start with a lubricant analysis program. They think they see failures that simply are not there.
"Get some kind of trend and baseline started before you start making any rash decision," Ewing emphasizes. "Unless you see a catastrophe — and what I mean by that is samples with extreme contamination from dirt or coolant — you really just need to use caution until you get a good trend line of your wear metals."
Thweatt agrees that customers should not over-react based on a single oil sample. "If you receive a ‘critical', resample to ensure that the initial oil sample was correct," he advises. "Do not use one oil analysis instead of trending to make a large decision, i.e., prematurely overhauling equipment or shutting down a vital piece of equipment for inspection with a false negative lab result."
It's also important to keep in mind that no two pieces of equipment will show the exact same analysis results, even though they may be the same make and model. "A guy might say he has three D9 Caterpillars and when the oil analysis comes in, [the results] are all different," says Ewing. "Yes, they are all D9 Caterpillars, but they are all different machines. Don't try to say that because machine No. 1 is doing this it is going to happen to the other two."
With the amount of data an oil analysis program can generate, computerized data management tools can simplify record keeping. "It is the easiest and the most productive way to use the data," says Minges. "There are all kinds of statistical analyses that you can do with these kinds of products."
The historical data collected helps put your current results in context. "With an ongoing oil analysis program that enables you to use current and historical data to compare trends, you can maintain the life and value of your equipment more effectively," says Thweatt. "Looking at historical data will also help you make more informed equipment purchases in the future. By evaluating equipment performance over time, you will know which models and manufacturers provide the best service under specific work conditions. The cost of oil analysis is a small price to pay for advanced warning that can prevent expensive and disastrous failures and downtime."