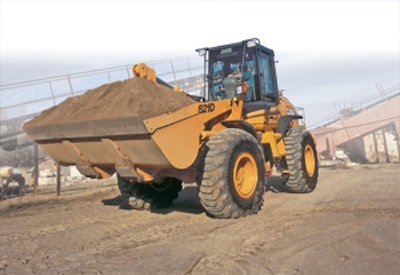
With the recent volatility of diesel fuel prices, increased efficiency takes on a renewed sense of urgency. Advancements in wheel loader designs deserve a close look if you are considering an upgrade.
Manufacturers have made significant advancements in fuel efficiency through a combination of new engine technologies coupled with load-sensing hydraulic systems.
"With the new H Series mid-size wheel loaders (216 to 307 hp), Caterpillar takes a system integration approach to improving fuel economy while improving productivity," says Geoff Perich, product manager for Caterpillar MWL Americas. This includes use of ACERT electronically-controlled engines with multiple-injection fuel delivery, load-sensing hydraulics and a hydraulically driven on-demand (cooling) fan. The result is up to a 5% fuel efficiency gain over the previous models.
This approach carries over to the smaller wheel loaders, as well. Caterpillar's Paul Travaillot estimates the combination of electronically-controlled engines with the load-sensing hydraulics and hydraulic on-demand fan results in a 10% to 15% fuel efficiency advantage vs. a loader without these features. It can even make a difference with novice operators.
"An experienced operator is going to have an advantage," he admits. "But the way our machines are designed, even a novice operator can still realize fuel efficiency."
Volvo also integrates several individual technologies into a complete system. "Two major components of Volvo's wheel loader design combine to create our best in class fuel efficiency — Volvo engines and load-sensing hydraulics," says Volvo's Dan Snedecor. Engines produce high torque at lower rpm than traditional diesel engines. This compliments the load-sensing hydraulics. "Without the load-sensing hydraulic system, our fuel consumption advantage would be minimal. But correctly combining the two yields an extremely fuel efficient design, while still using a conventional-style automatic powershift transmission."
Likewise, Liebherr has developed an integrated systems approach. "All Liebherr wheel loaders feature an advanced hydrostatic driveline system that reduces engine horsepower requirements and increases fuel efficiency," says Tim Doucette, marketing manager, Liebherr Construction Equipment. "The design of the drive system allows the heavy components (engine, hydraulics, etc.) to be placed at the rear of the machine and be utilized as active counterweight. As a result, Liebherr wheel loaders offer less operating weight while maintaining tipping loads."
Case has also optimized the placement of components for maximum efficiency. "On our D Series, we introduced a mid-mount cooling module," says Dave Wolf, marketing manager, Case Construction Equipment. "It moves the engine behind the rear axle, utilizing the weight of the engine as a natural counterweight for more stability. It reduces the weight of the counterweight." In addition, it allows access to the entire engine from the ground.
Engines adapt to the load
The latest round of emissions regulations for off-road engines have actually lowered fuel consumption in most cases. "With the emissions regulations, you start getting into charge air cooling, common rail fuel systems and electronic controls,"
notes Wolf. These technologies enable the engine to react to the load conditions.
Consider the benefit of charge air cooling. According to Wolf, it results in more cool air entering the combustion chamber. "So you get a cleaner burn and better fuel efficiency," he points out.
Engine electronics have also allowed the engine to adapt to any load changes. "The Caterpillar engine with ACERT technology utilizes electronic control and multiple-injection fuel delivery to ensure outstanding engine performance as engine speeds and load demand change," says Perich. Constant Net Horsepower is a feature that allows ACERT engines to maintain consistent working horsepower while compensating for any parasitic loads.
These engines can be coupled to adaptable transmissions. "Variable Shift Control allows the operator to choose either an aggressive, moderate or economy mode to address rimpull, underfoot conditions, shift smoothness and fuel economy," says Perich.
Power on demand
Because it takes energy in the form of fuel to produce power, you want a loader to consume the minimum amount of power required to complete a task. This is one reason Case uses load-sensing hydraulics in its D Series loader. "That has been a big benefit to fuel economy," says Wolf. "It basically supplies the loader function hydraulic power when and where it needs it vs. a continuous drain on the engine trying to supply that power all of the time."
It is essentially power on demand. "Load-sensing hydraulics reduce load on the engine at times when it's not needed," says Travaillot. "In addition, we also have a hydraulic on-demand fan that further decreases parasitic engine loss by consuming power only when needed."
Snedecor adds, "If the pumps in the system are sized correctly and pressures meet the needs of the loader's size and operating load, the machine will be more fuel efficient. The secret is all about the hydraulic load on the engine. Load-sensing systems only place a hydraulic load on the engine when a hydraulic function is actuated.
"Conversely, vane pump and gear pump systems place constant hydraulic loads on the engine regardless of hydraulic function," he continues. "So in the gear or vane pump systems, the engine works harder when the hydraulics are not being used, and when they use roughly the same amount of power to satisfy the hydraulic load."
According to Snedecor, there is no trade-off in fuel efficiency and performance when utilizing a load-sensing system. "In fact, performance is enhanced with more power and control at a wider range of engine rpm," he states. "In other words, a Volvo wheel loader can lift as much at 1,100 rpm as it can at 2,100 rpm with a lot less fuel going through the exhaust stack."
Reduced hydraulic loads on the system can also increase component life. "Load-sensing hydraulic systems result in smooth operation without the sudden movement associated with non-load-sensing systems," says Doucette. "The smooth operation of the machine reduces operator fatigue and increases the machine life cycle."
Reduced work translates into increased service intervals. "Because the system is not constantly pressurized, it does less work than a normal gear-driven hydraulic system," says Travaillot. "This in return reduces the amount of fuel needed and lowers the amount of debris and deposits in the oil, resulting in a cleaner engine. This allows longer time between engine service intervals. Load-sensing hydraulics produce less wear on the engine and hydraulic lines and hoses. The whole system experiences high pressure only when required."
A variable-displacement piston pump is at the heart of the system. "A variable-displacement piston pump cuts the losses experienced by a gear pump by half," says Travaillot. "This contributes to the bottom-line consumption of the machine, lowering annual fuel costs."
The systems also eliminate stalling. "Load-sensing hydraulics will not cause a machine to stall under loading, which is a common complaint for fixed-displacement systems," says Travaillot.
The Caterpillar H Series loaders take this one step further with an M3PC priority proportional pressure compensated section valve. "The new valve can set priority of function and proportionally decrease or increase flow and pressure to the lift and tilt function for simultaneous capabilities, resulting in material retention and ensuring no stalls," says Perich. "With the new load-sensing hydraulic system, operators see improved cycle times and a 20% increase in lift force."
Traction control
sparks debate
As long as there is sufficient traction, rimpull will remain a critical performance measure. "Rimpull not only impacts your ability to penetrate a pile of blasted rock in a quarry, but it is needed to dig a ditch or a basement," says Snedecor. "For dozing or land clearing, rimpull is necessary to complete the task effectively. But don't forget, good rimpull and the wrong tires result in poor performance."
Actually, rimpull can be misleading. "You can have too much rimpull and actually spin your tires," says Wolf. "If you spin your tires, all you are doing is wearing tires out and losing performance. To me, tractive effort is more important."
Manufacturers take different approaches to control wheel spin, with some offering automated traction control devices and others relying more on the operator. There is also some debate over limited-slip differentials vs. standard open differentials or locking differentials.
Volvo favors keeping the operator in control. "Wheel spin is ultimately controlled by the operator and we offer no ‘governor' for wheel spin aside from the throttle pedal," says Snedecor. "Many manufacturers are approaching controlling wheel spin with ‘spin control' devices that actually govern (limit) engine power to a level where wheel spin is less likely to occur. A trained operator can do this himself and will burn much less fuel than an operator who is conditioned to operate at full throttle all of the time via a governing device."
What Volvo does offer is a front differential lock on all models in the mid-size range. "This is a 100% locking differential which the operator controls," says Snedecor. "To compliment the front differential lock in exceptionally tough traction conditions, we do provide a limited-slip rear axle in combination with the locking front axle."
Liebherr offers traction control, which allows the operator to adjust the loader to match underfoot conditions. "Limited-slip differentials and traction control are standard on Liebherr wheel loaders," says Doucette. "The ability to reduce wheel spin and ‘dial in' tractive force results in better ground force, increased penetration and reduced tire wear. Tractive force can be adjusted on the fly to reflect the current ground condition."
The advantage to the limited-slip differential is it requires no operator input. "Case offers limited-slip axles, which automatically transfer power from the wheel that is slipping to the one that is gripping so that you maximize tractive effort," says Wolf. "You will get up to 45% power transfer completed without any operator intervention at all."
Caterpillar offers conventional open, limited-slip and NoSpin differentials. "The advantages to the open differentials are no steering or tracking interference, minimal tire scuffing or wear and low operating cost," says Perich.
Standard open differentials experience less wear, but limited-slip differentials offer better traction for underfoot conditions. "Driveline wear is somewhat increased as the friction material and torque transfer properties in the system create wear over standard (open) differentials," says Travaillot. "However, tire wear is reduced."
In certain applications, limited-slip differentials have the advantage. "Compared to locking differentials, maneuverability — especially while turning — is increased and driveline wear is lower, as well," says Travillot. "We believe that limited-slip differentials provide the traction control and performance customers require without compromising durability or tire life, keeping ownership costs low."
A rear-only NoSpin differential is available on Caterpillar's H Series for specific applications; it is mainly used in very extreme conditions. When locked, the NoSpin differential can transfer 100% of the torque to the tire that is on better footing, improving tractive effort, Perich explains.
Case avoids the use of differential locks. "We do not have locking differentials at all," says Wolf. Tire wear is the primary concern. "You are going to cause drag on your tires when you are turning corners."
Beyond axle configuration, the other items that have a major impact on traction are the tires. "Proper tire maintenance can dramatically affect fuel economy," says Wolf. This includes proper inflation and tread life. "Make sure that you are not running slicks."
In addition, radial tires place a larger footprint on the ground. "In fact, with bias vs. radial, you will see some fuel number changes because of that," says Wolf. The radial tires will be more fuel efficient.