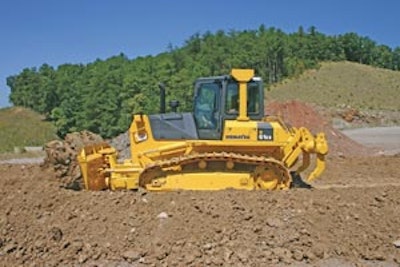
New-to-the-trade dozer operators may not be able to fully appreciate the level of operating efficiency and comfort experienced when stepping into the cab of today's modern machines. But more seasoned veterans know full well when someone references the "good old days," they aren't reminiscing about the comfort associated with operating dozers from years past.
"I operated my first bulldozer 40 years ago," says Ed Warner, product manager for dozers, Komatsu. "They used to take a lot of effort, and the seats often felt like you were sitting on nothing more than a crate. Now, being in a dozer is more like being in an SUV, with suspension and air ride seats, armrests and AM/FM radio/cassette players. They're very comfortable and easy to operate."
Shane Thompson, owner of Thompson Grading, Inc., is also more than happy to leave those old models behind. He owns seven dozers — five Komatsu and two Cat units — that he uses in his residential and commercial grading business near Woodruff, SC. Even the progression from machines he purchased as recently as 1999 is significant. "They've gotten a whole lot quicker and a lot less fatiguing on the operators," he says.
Moving toward hydrostatics
Some of the changes to dozers have been relatively minor, such as moving the seat position. However, Thompson believes even this small change is a benefit, since many jobs require operators to turn around and monitor what's happening behind the machine.
Other changes have been more significant, such as the transition to hydrostatic drive. This feature is what Thompson appreciates most about the newer models. "It allows the machine to turn in a lot tighter radius," he says. "And steering is a lot faster."
Hydrostatic drives are becoming increasingly common on many new dozers. According to Brett Errthum, product marketing manager at John Deere, the advantages are twofold: ease of operation and efficiency. "Hydrostatic transmissions are easy to operate because the operator can doze at wide-open throttle at any track speed," he explains. "This enables new operators to gradually increase their speed as their skills improve. The hydrostatics automatically adjust to eliminate the need for the operator to choose the optimum gear for the job at hand. On slopes, the dynamic braking of the hydrostatics allows for predictable control at all times."
The hydrostatic powertrain also achieves maximum efficiency at working speeds when loaded. "At those same low speeds, a torque converter generates heat," Errthum relates. "This heat is a byproduct of lost power. Deere's Total Machine Control (TMC) constantly monitors engine performance and alters pump ratios to maintain peak engine power and efficiency. Performance testing a variety of applications shows the fuel consumption savings compared to a torque converter machine can be as much as 20%, without any compromise in productivity."
New Holland Construction also utilizes a hydrostatic drive system in its DC75, DC85 and DC95 machines. "The answer to which system is more productive — mechanical or hydrostatic — can be debated," says Jorge DeHoyos, brand marketing manager, New Holland Construction. "However, the question of efficiency is not." He notes that hydrostatic components can be sized for the proper track and blade force. "By using over-sized hydrostatic components, our small dozers can out-push and out-pull their respective competitive models."
Ergonomic directional controls
Directional controls have also been updated in many new models.
"In the past, mechanical linkage controls required a good deal of arm strength, and you had to move the controls a great distance," says Warner. "With advanced hydraulics, all that is needed is a very light touch with very short movements."
Many within the industry — manufacturers and contractors alike — compare modern dozer controls to joysticks used for video games. "All that is needed is a very slight movement to control the machine," Warner points out.
Komatsu's Palm Command Control System (PCCS) joystick controls all directional movements, including forward, reverse, left, right and counter-rotation. "From our smallest to our largest machines, steering and blade control are common," says Warner. "The PCCS joysticks are ergonomically designed to fit the typical operator's hand. The handle is at an angle so when the operator sits in the seat with his arm on the armrest, the control fits very naturally into his hand."
Thumb push buttons are incorporated into the joystick of Komatsu's larger, torque converter machines for transmission gear shifting. Thompson welcomes this feature on his D61. "With the older machines, a gear pattern was controlled with your whole arm," he recalls. "Now, all I have to do is hold my hand still and press the button with my thumb."
In the case of Deere machines, one joystick operates the transmission (steering, speed and direction), while another controls the blade. A single pedal combines the decelerator and brake function. "Pilot pressure hydraulics and electronic transmission control have dramatically reduced lever efforts," Errthum says. "As a result, the operator can work longer stretches without a break, and feels better going home at night."
Improved blade control
Blade controls have received a facelift similar to that of directional controls.
For example, engineers for New Holland machines have designed an ergonomic palm grip for ease of effort and multiple settings. "The new grip gives the operator a better feel for the blade's movement," says DeHoyos. "Having the ability to move the blade in a variety of positions is popular, as well. Six-way blades used to fit the bill . . . But today, more [manufacturers] are also including variable blade pitch adjusters, which allow the operator to adjust the pitch of the blade for better finish grading or excavation."
Deere has introduced new valve profiles to allow for consistent performance on hot or cold hydraulics, notes Errthum, and load-sensing hydraulics ensure consistent blade response regardless of the load. "All of these combine to make the blade an intuitive tool for the operator," he says. "The vehicle becomes less of a complex machine and more similar to a mason's trowel."
Thompson and his employees appreciate the ease of operation in both directional and blade controls. "Controls have changed dramatically, even since the late 1980s and 1990s," he says. "Those machines had a single control lever that was bulky and about 24 to 30 in. With the joystick controls, the machine responds instantly with just a touch. To get full blade control, you only have to move about 3 in. It's a whole lot faster response time. It's also smooth movement of the machine instead of a jerking motion."
Controlling speed
Features incorporated into today's dozers also provide for better control of operating speed.
New Holland models delivers multiple ground speed settings that are adjustable through the use of the control lever. In addition, a reverse ratio control allows operators to adjust reverse speed in contrast to forward speed. "Since a typical application requires a dozer to move in reverse 50% of the time, the reverse ratio control comes in handy when you're maximizing production and extending the life of your undercarriage," says DeHoyos.
Deere dozers feature sensitivity settings for steering, direction changes and engine lugging. The machines also allow the operator to select whether the decelerator slows the engine and transmission or transmission only, where the operator can maintain full power to the tracks and implements while slowing the tracks with the decelerator.
Ultimately, the changes in dozer designs have helped to improve production and the quality of work, says Thompson. "We get a lot smoother finish with a lot less time spent on fine grading work," he asserts. "We don't have to redo it with another application to get a finished product. These changes have helped speed up our entire process."