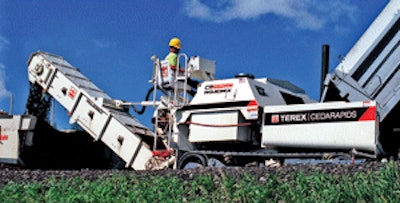
Temperatures soaring into the upper 90s with dew points reaching the oppressive 70-degree range mean it is just another typical Midwest day during the height of paving season. While the corn that stretches as far as the eye can see relishes the thick, moist air, the conditions are barely fit for the crew or beastly paving equipment. And it’s certainly not the conditions that a company would purposely select for a new material transfer vehicle’s (MTV) first field test.
But this was just the application that Terex/Cedarapids chose for field testing conditions of its CR662RM RoadMix MTV (now marketed by Bomag, March 26, 2013).
Bomag (Fayat Group) To Acquire Terex Roadbuilding Assets
“We want to make sure it performs in all conditions, so why not start with extreme heat?“ comments Mark Hunt, general manager of Terex Roadbuilding’s Asphalt Mobile Equipment Group. During this first field test, the RoadMix kept its cool and a consistent pace on a county highway project in Eastern Iowa.
Feel the heat
The Benton County Highway W26 application coincided with a heat wave that saw record temperatures in Iowa. Six-and-a-half miles of roadway were milled at 1/2-inch depths at the headers and 1 1/2-inch depths at the ends. The road’s poor conditions also required two-inch thick milling depths in certain sections.
“The surface was in pretty rough shape from years of patching,“ says Jack Robinson paving foreman for North Liberty, IA-based LL Pelling Co., the contractor on the Highway W26 project. “Parts of the road were patched over the years, which forced us to go a little deeper in those areas.“
Surface milling took place over three days and the millings were recycled and used to strengthen the shoulders. The highway’s new surface was laid in two 1 1/2-inch-thick lifts. Both the leveling and surface courses consisted of a half-inch minus aggregate with a PG64-22 asphalt binder. LL Pelling’s J Street plant, located nearly 20 miles from and an average 40-minute one-way haul time to the site, supplied the 13,000 tons of mix for the job.
This mix was laid at approximately 290 degrees Fahrenheit with the breakdown roller immediately compacting the mat after being laid. “We tarp our loads to reduce temperature loss during transit,“ says Brett Finnegan, vice president of LL Pelling.
The CR662RM RoadMix MTV led the paving train and consistently channeled material to a Terex/Cedarapids CR561R paver with Stretch 20 diesel screed, which laid the mat and delivered initial densities. Following the paver were the I-R tandem vibratory breakdown and finish rollers and a Dynapac rubber-tire roller.
The MTV’s primary objective was to establish a continuous paving process that matched the plant’s target production capacities for the job. According to Finnegan, the RoadMix “did its job.“ Beyond continuous, non-contact paving, the MTV’s in-hopper reblending augers helped to improve mat uniformity and quality.
“When working on other projects without the MTV, we would occasionally see little chunks of asphalt slip through the paver and into the mat,“ says Robinson. “The RoadMix breaks up those chunks and gives us a more consistent mat.“
Familiar design
The new MTV’s design is based on the Terex/Cedarapids patented Remix Anti-Segregation System, which explains LL Pelling’s improvement in mat uniformity. In-hopper augers reblend asphalt from the truck to provide a more homogeneous mix to the screed. The two sets of two counter-rotating auger design is field proven to reduce both thermal and material segregation.
The RoadMix’s reblending system differs slightly from the Remix paver’s auger design. Auger diameter on the RoadMix has been increased to 12 inches, delivering an additional 42 percent auger face area and material carrying capacity.
“Increasing the diameter allows the augers to turn slower while still carrying the same amount of material as with the Remix design, which helps to reduce wear,“ explains Hunt.
The chromium carbide hardened augers are dropped further into the hopper frame, so the tops are at or below wing level. The auger troughs are completely filled by the auger sets to reduce material slippage.
A 3-inch, front-to-rear slope design - a 4-inch inset at the hopper’s front and 7-inch inset at the rear-hardened steel feed tunnel - increases channeling capabilities of the auger sets. The 7-inch recess at rear increases the volume of area to reduce material build-up. “All the design changes result in less wear and increased throughput,“ adds Hunt.
Another design change from Remix to RoadMix puts the auger drives at the front of the hopper. A single hydraulic motor powers each set of counter-rotating augers. This design ensures the auger sets rotate in-synch.
This drive change was necessary to accommodate the MTV’s conveyors. A short fixed-position conveyor accepts asphalt from the augers and delivers it to a long swiveling conveyor, which rotates 55 degrees left or right of center to allow for offset paving. The delivery conveyor’s height can be adjusted from 72 to 116 inches.
Continuous savings
Even though this was LL Pelling’s first experience with the CR662RM and the MTV’s inaugural field test, the contractor was quickly able to establish a continuous paving process. Designed similar to and capable of converting to a paver (see “MTV double duty“), the MTV required minimal time for the operator to learn the control panel layout and machine operation.
Since the MTV is not connected to the paver, it delivers non-contact paving. This allowed the paving crew to eliminate any “bumping“ of the paver during truck exchanges and any potential mat marking.
LL Pelling significantly reduced the number of trucks required for the 13,000-ton Benton County application. For the 40-minute haul, the contractor required only 14 trucks to ensure a continuous flow of material to the MTV. “If we would have delivered directly to the paver, we would have needed approximately 20 trucks,” says Finnegan.
At peak paving production, the contractor set daily goals of 2,200 to 2,400 tons per day. At this rate, the paving crew laid more than four miles of asphalt at the 1.5-inch depth. This also allowed the contractor enough room to produce additional asphalt mixes from the J Street plant for local commercial paving applications. “With traffic flow concerns on a county highway, paving at 250 tons per hour is a good clip,“ says Finnegan.
Mat quality was just as important as establishing a continuous paving speed matched to plant production on the Benton County Highway project. Uniformly-spaced aggregate and uniform mat temperatures allow the rollers to more easily achieve spec densities.
The CR662RM helped LL Pelling to achieve this as well. “Mat uniformity was great,“ says Finnegan. “The RoadMix helped us to lay one beautiful mat.“