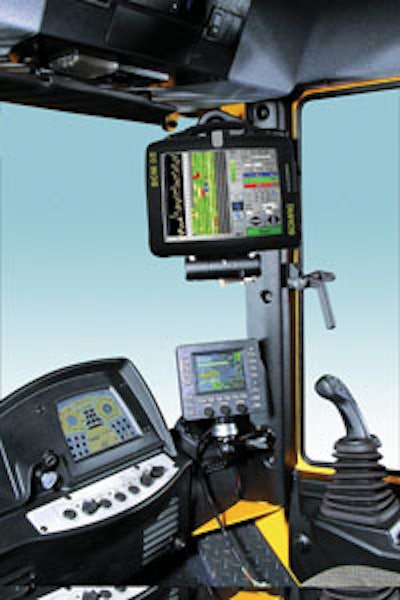
When it comes to compaction — whether it’s soil or asphalt — many contractors rely on past experience with similar materials to set amplitude and frequency, the number of passes and roller speed. Yet, a range of factors can affect how quickly and efficiently density is achieved on a particular surface, including changes in ambient temperature or weather, moisture content in soil, mat temperature for asphalt, mix quality, experience of the roller operator, etc.
Manufacturers of large rollers have recently introduced drum and onboard control technologies designed to minimize the effect of such variables. The goal is to transform the compaction process into less of an art and more of a science.
Greater frequency plus a smart drum
High-frequency asphalt rollers have grown dramatically in popularity. Dale Starry, product manager at Ingersoll-Rand, attributes this to an increase in average paving speeds. Higher frequencies (3,800 to 4,000 vpm) enable the rollers to maintain the same impacts per foot at faster rolling speeds. This in turn speeds up the entire paving process and, in some cases, may eliminate an extra roller on the job.
One of the challenges associated with higher frequency has been the potential for increased bearing wear in the drum. “The life of the eccentric bearings that support the unbalanced weight inside the drum is reduced by the factor of the speed of rotation,” Starry explains. “If it spins at 2,500 vpm, bearing life might be 10,000 hours. If it spins at 4,000 vpm, the life might be 2,000 hours.”
In order to achieve acceptable bearing life, some manufacturers have been forced to reduce the load on the bearings by reducing amplitude. “That means that the high-frequency compactor can’t compact layers as thick as a standard compactor of five years ago,” says Starry.
Ingersoll-Rand has addressed this problem with the introduction of SMART drum technology, a system that automatically adjusts roller frequency to the amplitude setting. “In the lowest frequencies, it has the ability to have very high amplitude like we used to have,” says Starry. “But at the highest frequencies, we limit the amplitude and the machine does it without the operator’s attention.”
Currently, this feature is available on the DD-118HFA, DD-138HFA and DD-158HFA (high frequency and amplitude) models, with a fourth model to be added later this year. Other SMART technologies include a propulsion system for automatic control of rolling speed; a water system with automatic shutoff and regulation of water flow; and a start system that prevents vibration of the trailing drum on cold or hard pavement surfaces.
New vibrations
Another recent advancement in drum design is oscillation. Available on the Hamm HD O90V and HD O120V rollers, oscillation compaction works by “massaging” asphalt in a forward/backward motion.
“In a standard vibratory drum, you have a center-mounted eccentric shaft. That out of weight eccentric spins and causes the drum, in essence, to bounce up and down,” explains Bruce Monical, marketing manager for the Hamm Compaction Division of Wirtgen America. “Oscillation uses two eccentric shafts with the eccentrics turning in the same direction, but they are 180 degrees out of phase with each other. Instead of the drum bouncing up and down, it rocks back and forth.”
Because the drum never leaves the mat, there are no vertical shear forces that could break the aggregate, asserts Monical. “It allows the operator to compact continually without a concern of over compaction or breaking the aggregate,” he states. He also contends that asphalt temperature is less of a concern due to the elimination of the “hammering” movement of the drum.
“As the temperature starts to cool, traditionally, in North America, we’ll use either a pneumatic rubber-tire compactor or a tandem steel roller with the vibration off,” says Monical. “In the case of oscillation, you can run the tandem steel, but you can still oscillate and run those vibratory horizontal shear forces. This should be able to draw your densities up quicker because you have a vibratory effect in the asphalt.”
This is also proving effective for joining hot and cold longitudinal joints. “We have discovered that oscillation can bond those joints more efficiently because you don’t have to worry about running static on the cold side,” says Monical. “You don’t run the danger of breaking the rock that you’ve already compacted.”
The more gentle action of the roller is also better suited for laying asphalt on concrete bridge decks, Monical adds. “With oscillation, you can compact asphalt much quicker than just running a static machine, and you don’t run the danger of putting vibratory forces into that concrete,” he states.
Getting onboard
Perhaps the most intriguing advancements in large soil and asphalt rollers are onboard systems designed to monitor and/or help control density during the compaction process.
Systems vary in terms of their cost and complexity. Following is a look at some of the available offerings.
Onboard density testing
Ingersoll-Rand offers an optional TransTech Pavement Quality Indicator (PQI) for its HFA models. Listing at about $15,000, the PQI operates like a hand-held density meter, but incorporates the sensors and readout directly onto the roller.
“By having the density measuring device mounted on the break-down roller in a paving train, a contractor can adjust his rolling pattern to assure he will receive 100-percent payment for the pavement,” says Starry. “This compares to having a hand-held device used by a quality control technician generally behind the finish roller when it is too late to change the result.”
The PQI option does not control roller functions. Rather, it acts as a quality assurance device during the compaction process.
“We recognize that by keeping our design simpler, the overall life-cycle cost of the compactor is going to be lower, as well,” says Starry. “We’ve done it through the installation of an accessory option and we’ve kept the compactor effectively unchanged.”
Intelligent compaction
Bomag America has taken density control a step further by incorporating Variocontrol Intelligent Compaction on its larger soil compactors.
“Intelligent Compaction monitors stiffness gain and it will tell the operator when he has achieved maximum density,” says Steve Wilson, manager of marketing services/product manager, Bomag America. “It controls the number of passes, ensuring just the number required to achieve optimum bearing load or stiffness.”
This reduces the risk of over or under compaction. “The operator is not going to spend more time than he should in a given area and possibly break down the material and start losing density,” says Wilson. “It defines the exact rolling parameters.”
The Asphalt Manager system performs a comparable function on larger asphalt rollers. “It’s even more beneficial on asphalt,” says Wilson. “Intelligent Compaction doesn’t allow over compaction. It prevents the roller from hitting harder than the material needs to be hit.”
Intelligent Compaction is available on most rollers above a 66-inch drum width. The system features a directed exciter mechanism that automatically adjusts the position of the eccentric weight in the drum according to the amount of force required to achieve density.
“In our systems, the drum doesn’t necessarily change the amount of energy it produces. What we do is change the direction the force is being directed into the material,” says Wilson. “It’s more of a glancing blow at an ever-increasing angle.”
As material stiffens, the system automatically re-indexes the impact force at more of an angle, directing less energy into the material. Once compaction is achieved, force is directed horizontal to the material.
“As it develops more compaction from the bottom up, the top portion gets less and less energy,” says Wilson. “It’s all done through a microprocessor-based system, so it’s very fast and automatic. It can shift from straight vertical to horizontal in milliseconds.”
Global positioning
For its larger soil rollers, Ammann America offers the Ammann Compaction Expert (ACE), an electronic measuring and regulating system that measures stiffness of the compacted layer and indicates the value to the operator. Each pass of the machine provides full reporting of compaction measurements and automatically adjusts operating parameters. The system also indicates the optimum roller speed to ensure constant impact spacing.
Transducers mounted on the drum and frame measure how the drum reacts to the material. As the roller encounters harder or softer material, an electromechanical servo system varies the relationship of the opposing weights in the drum.
“Not only is the amplitude and frequency adjusted, but also the mass applied to the drum to make it vibrate,” explains Jeff Fox, product/marketing manager for Ammann.
“It allows the system to react within milliseconds of encountering compacted material.”
ACEplus incorporates the ACE system, plus adds GPS mapping and tracking capability. The GPS component uses an overlay of a jobsite map to track positioning of the roller on the site. By using satellite navigation to determine roller position, it is able to gather compaction data with an accuracy of just a few centimeters.
“As you roll over [points on] the map, [the onboard display] actually shows where you are on the job and it shows the densities that have been obtained on that strip,” Fox explains. “You can look at the whole project, or you can just look at the next 100 feet in front of your machine.”
Information can be downloaded to a PC, transmitted to a receiver on the jobsite or sent back to a home office via wireless Internet.
Complete machine control
Hamm soil compactors are also available with a choice of systems. The basic onboard system consists of a drum-mounted sensor that registers feedback from the drum, then informs the operator, via an onboard monitor, when target compaction has been achieved in a specific area.
The Hammtronic computerized management system, on the other hand, takes compaction to a whole new level, providing more complete control of the machine. “It electronically adjusts the engine rpms, traction control, travel speed, frequency and amplitude of the drum, and it can be pre-programmed to stop and start at a certain location,” explains Monical. “For all intents and purposes, it requires the operator to do only one thing — drive in a straight line.”
Hamm also offers GPS satellite location and mapping software, which monitors roller location and compaction performance. “It not only indicates where [material] was or was not compacted, but you can include that onto a map of your jobsite,” says Monical. “Your mapping indication is actually within [centimeters] of where you are.”
According to Monical, the combination of the computerized management system with a compaction meter and GPS mapping software completely eliminates the guesswork from the operator. “You know exactly what your machine has done, where it has done it and where it needs to do it again if necessary,” he adds.
Justifying the cost
Admittedly, the costs of more complex onboard systems can be significant. They range anywhere from $20,000 up to $80,000, depending on system features and roller size. That can equate to roughly 33 to 50 percent of the cost of a base machine.
As such, onboard systems aren’t for everyone. “If you’re the type of contractor that spends 80 percent of your time doing small projects that don’t encompass large areas, and there’s not any major demand for the end result, it’s a little bit harder to justify,” says Wilson.
However, on larger projects with tighter timelines, stricter specifications and even warranty requirements, onboard technology may be worth considering.
“People today are being held more accountable for their work,” notes Monical. “We’re seeing more warranty jobs on roads and part of that has to do with what’s underneath the road, as well.”
Monical also foresees more sensitive projects, such as airports and race tracks or those involving construction on landfills or in reclaimed areas, eventually demanding proof of bottom layer compaction. Most onboard systems can provide documentation to show densities were, in fact, achieved.
“Most systems have the ability to create some form of electronic or paper trail to use long term,” adds Wilson.
Should state and federal governments come to accept this documentation as proof of performance, contractors working on such jobs may be forced to look at onboard systems as a way to more effectively meet density specs, reduce testing costs and, ultimately, minimize liability should a structure prematurely fail.
High frequency speeds paving With the advent of more complex asphalt mixes, the demands placed on contractors for compaction specs have become increasingly difficult to meet. “Back 10 years ago, the state of Maryland started getting tougher on some of the density requirements we had to obtain to get payment. The mixes were more challenging, and Superpave was coming of age,” says George Bartholomew, job superintendent at David A. Bramble Inc., Chestertown, MD. The general contractor performs a variety of heavy highway and road construction and utility work throughout the Eastern Shore area. “We found it tougher with our traditional rollers to try to get the compaction that we needed.” The solution came in the form of Ingersoll-Rand’s high-frequency rollers. “When they introduced the high-frequency technology about 10 years ago, we got one of the first ones,” says Bartholomew. “They let us demo the technology on a job in Easton. We were very enthusiastic about it at that time and so we went ahead and invested in it.” The company owns 10 large Ingersoll-Rand asphalt compactors ranging from 10 to 15 tons. The high-frequency models have enabled the contractor to speed up the paving process. “With the higher frequency, we can keep the production rates of our crews up where we want to without suffering because of compaction,” says Bartholomew. “You’re not getting anymore downward pressure on the mix, but you’re able to cover more ground with the same roller.” The rollers also offer an eight-amplitude eccentric design that enables amplitude to be adjusted to the material and lift thickness. The flexibility to adjust the rollers to the mix proved instrumental on Maryland Route 311, says Bill Wetmore, paving superintendent. “We were having trouble with our mixes — the tender zone was much longer than we had ever had before,” he says. Maryland state specs did not permit compaction on the mix after it reached 185 degrees. “Our front rollers were making as many passes as allowable and if they tried to make any more, they were in the tender zone.” Using the high-frequency rollers, the compaction crew determined it was possible to use vibratory compaction at 150 degrees and still achieve required densities. “We could still get our compaction bumped up enough at 150 degrees to get our cores to pass,” says Wetmore. “Without the Ingersoll-Rand high-frequency rollers, the production would have been cut right down. We would have had to slow up the whole operation — and you don’t make any money.” |