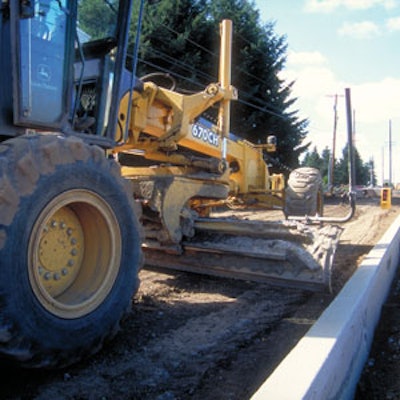
GPS technology is transforming management of earthmoving operations by increasing productivity and compressing time schedules, while cutting production costs. Three contractors who have experience with these systems explain how it changed their earthmoving operations and how the technology generates a return.
In-house staking saves resources
Slusarski Excavating and Paving is a site work contractor. "We do earthwork, underground utility work and asphalt paving, as well as general contracting" says Mary Christie, project manager. The company is currently using Topcon GPS with automated machine controls on a Volvo 726B grader and Topcon GPS on four Caterpillar dozers, as well as a field controller unit.
The Topcon GPS allows Slusarski Excavating and Paving to handle most of their required staking in house. This reduces the time and money spent waiting on outside surveyors. "You save money by reducing the amount of stakes that you need as well as reducing equipment downtime if you lose layout stakes and need to replace them," Christie says.
Outside surveyors are not eliminated. "We still need surveyors to come in and set up survey control points. From there, we localize the project using the field controller, and that localization is what the equipment systems run on," says Christie. Surveyors are also used when a high degree of precision is required, and to occasionally double check work done with the GPS system.
The GPS system can be accurate to within a quarter of an inch. "When doing spot checks for grade, you want to get it as close as possible," says Christie. "If I am doing layout stakes, I'll usually give myself between 1/2 in. to a tenth of a foot. You always have a little variation when using the field controller."
In many applications, a tenth of a foot is close enough. "On the job we just finished, we did the majority of our grade stakes and utility stakes," says Christie. However, an engineering company was brought in to lay out the roughly 2,800 ft. of curb and gutter. "As far as curb and gutter, you have to make sure that the grades are perfect and we didn't think we had the resources available for the time it would have required to do that," says Christie.
Engineering companies are also used during peak demand. "If we get backed up where we can't handle all of the staking that needs to be generated, we definitely do use them," says Christie.
The savings in terms of staking are significant. "The staking costs have definitely gone down now that we've eliminated the grade stakes and have the ability to do the layout staking in house," says Christie. On a $1.5 million project, traditional staking costs could run between $50,000 to $150,000. By reducing this cost, the GPS system quickly pays for itself. "If you did two jobs that were between $1.5 to $2 million, I think it would recoup the cost in staking."
The Topcon GPS system had a major impact on Christie's job duties. "It put more responsibility on me and the other supervisors to be able to manage our time and get everything laid out," she says. "The grading files also require a lot of prep work in the office prior to the information hitting the field and our engineer handles that for all of our projects. Last winter, I handled probably 80% to 85% of the staking and layout. I would be staking all day, and then working on everything else I had to do in the evening. We have looked into hiring someone full time whose main responsibility would be to do all of the layout and staking."
There is a learning curve. "There's a lot of ways to screw things up really fast in the field controller and the equipment setup if you don't know exactly what you are doing," Christie points out. "But we managed to get a good grasp on it and we have been able to utilize it to our best advantage. Looking back, I think both the management and the operators acclimated themselves to the system fairly quickly. As you understand how the system works more and more each day, it cuts down on human error. It does cut down a lot of the re-work."
Christie advises those interested in this technology to look at all of their options. "Research it thoroughly. Have people come out and demonstrate it on site," she advises. "It's a great tool to increase your productivity and efficiency, and the savings you get out of the system are relative to the effort you put into understanding how it works."
Reduced staking equals productivity
River View Construction is an earthmoving contractor with typical projects consisting of parking lots, building sites and road work.
"We were doing all of our own staking for our projects and it got to a point where we could not keep up, so we looked into other ways to reduce the staking," says John Stone, registered land surveyor.
In 2001, the company invested in the Trimble SiteVision GPS system to reduce staking. The results have met the desired goal. "We can get a lot more done in a short amount of time," says Stone. The technology quickly proved itself and the company now has eight SiteVision GPS systems.
Stone is in charge of most of the staking on the company's projects. "We do have a surveying company that does work with us. We hire them to do the curb staking and some of the things that take more time," he notes. "We have the accuracy, it is just that we do not have the time and the personnel to do some of the staking."
The Trimble systems pay for themselves quickly with the reduced staking costs. "One-third of the staking cost is saved by using this equipment," says Stone. In addition, use of the SiteVision GPS system on the equipment compresses the time it takes to complete projects. "Some jobs we used to wear out the material before we got it in place. It seems now we know where the cuts and fills are. We put the dirt where it is supposed to go and move on."
This allows machines to work more efficiently. "We can take on bigger jobs with less equipment," says Stone. "What we used to get done in 10 or 12 hours, we can get done in an eight-hour day."
The Trimble GPS-based 3D grade control system also changes the way River View Construction approaches jobsites. "There is a lot more initial setup than there was before," says Stone. "We have to get the plans ahead of time and have at least two weeks of setup time with site initialization and setting up the design so we can put it on a card. We hired Chadd Hamman who just graduated from engineering school. He has been starting on our designs and has been doing a real good job."
The advantage to this initial setup is that errors in the design are typically caught earlier. "We used to get a paper plan out, lay it on the hood of a pickup and build the job. Now we have to go more in depth because we have to load it into the computer," says Stone. "We are a little more in tune with what is happening on the job. So if there is a problem, we can look at it and figure out how to fix it before somebody is upset."
The Trimble SiteVision GPS System has proven a valuable asset. "I think our initial investment was in excess of $100,000 above the dozer we put it on," recalls Stone. "But once you are into it, the initial cost doesn't mean much because you make it back so soon. We get the job done much quicker than we had in the past and it has saved a lot of time. Since we started with [the Trimble GPS system], we have doubled the volume of earth that we move in a season. We can handle so many more jobs and move so much more material in a year's time because we can get it done more quickly."
Eliminate rough staking
Kerr Construction performs earthwork and underground utilities. "It is pretty much a 50/50 mix of public work and private development," says Brent Kerr, president. "We do road construction, dam construction, commercial site work and subdivisions. We are licensed in seven western states, but we primarily work in Oregon and Southwest Washington."
The company has used GPS systems for four years. "We use it for both surveying and machine automation," says Kerr. An Ashtec system was the first, followed by the addition of a Topcon system. They both allow Kerr Construction to start moving earth very shortly after transporting equipment to a site. "We have a grading permit and we are instantly starting to move more earth, rather than waiting two days to a week to get a surveyor out there and get enough grade control to get started."
Kerr Construction uses the technology to eliminate rough grade stakes. A Caterpillar D6R dozer with an automated system is used to mark grade for other equipment on the site. "We cut grade holes everywhere so the scraper hands can see them," says Kerr. "They do not have to interpret stakes anymore. We cut the grade hole and mark that as grade or push up grade in the fill area. We will go in and make those on a grid."
This technique has saved Kerr Construction the expense of rough grade stakes. Consider the company's current project. "On this 100-acre site, it is probably a $50,000 to $100,000 savings," says Kerr.
Kerr uses the elimination of rough staking as a marketing tool. "When we get down to negotiating the project, we say, ‘We have GPS. You don't have to spend $50,000 to $100,000 on the rough grade'," he explains. "That is just another savings for the owner, but it helps us get $15 million projects. I don't even blink when I think about the $120,000 we spent on the Topcon system."
But rough grading is only one aspect where the GPS system benefits Kerr Construction. "We feel there is a production gain of 40% to 50% just on finish grading," says Kerr. It minimizes the re-work. "When you set the blade down, you know where grade is. It does not matter if it is in between 50-ft. staking or 20-ft. staking." This really helps in the grade transition areas where you would traditionally cut and fill, maybe overfill by a couple of tenths, then have to come back in to clean it up.
By creating topos and working with electronic files, Kerr Construction has also been able to resolve design problems earlier in the process. "If there is an issue in the design, it is better to find it early than late," says Kerr.
One such problem became apparent when a topo was performed for the 100-acre site Kerr Construction is currently on. "From a value-engineering standpoint, the first thing we do is a topo, just to check the topo with the engineer," says Kerr. When the topo was performed, it did not match the engineering data. "It was from half a foot to a foot high everywhere. We went to the owner and said, ‘We think there is a problem; we need your engineer to check with us.' They figured out they had made mistakes on the topo. We went back and adjusted all of the design elevations and solved the problem before we ever started. That saved us from having an 80,000-yd. stockpile a year later. You save that whole discussion with the client about the pile that costs $400,000 to haul away."
All of these benefits make it difficult to pinpoint exactly how long it takes to make a return on your investment. "It depends on how you are looking at things," says Kerr. Consider the potential $400,000 pile above. "In that case, it has paid for itself three times over already because we did not get stuck hauling that pile away. That was the first week we had it on the jobsite."
Manage the Site
GPS systems simplify your ability to manage your jobsite. "A topo of the site can be done rapidly with GPS and one person," says Fred Rogers, segment market manager, machine automation, Leica Geosystems. "That can be printed out and it will tell you the volume of dirt moved. You can get an estimate of what the cuts and fills are and where you are in your production."
The GPS performs this task much quicker and more accurately than the traditional method of creating a topo. "When you do a topo conventionally to calculate volumes, you do it in a grid," says Rogers. "That could be a 25-ft. grid. It could be a 50-ft. grid." Blue tops are driven into the ground to grade on a grid. You know you are correct at the blue top, but between the blue tops, you are not really sure.
The GPS can solve this problem by quickly checking the grade at more closely spaced intervals. "The surveyor can topo the site quicker and take shots at whatever intervals he programs it to - every 2 ft., every 10 seconds, every 2 seconds, etc.," says Rogers. "They will have a tighter topo map of the site." This data can be captured to create a model, which can be compared to a previous model to determine the volume moved.
The typical accuracy of the GPS systems is a tenth of a foot. But the ability to record data points in a tighter grid pattern increases accuracy over traditional topo methods. "Even if you have an error of 1.2 in., a 2-ft. grid pattern would be more accurate than a 50-ft. grid. Between the 50-ft. [data points], you don't know what is happening," says Rogers.
But the main advantage to supervisors is the ability to manage cuts and fills on the jobsite. Leica Geosystems offers a Foreman's Package that uses a data collector to display the cut and fill information. "Anywhere they go on the jobsite, they can see material that is needed and material that was hauled away," says Rogers. This allows the supervisor to accurately manage the borrow pit, pull material out and place it to grade on the site. "Once the information is located on the data collector as far as the site, there are routine functions to check elevations and see if there is a cut or fill."
Another advantage of this system is the ability to create as-builts. "You can do an as-built to see how your model compares to where you have to be at finish grade," says Rogers. "There are spread sheets that can be printed out as proof you moved a certain amount of material. You have proof that the work was done."