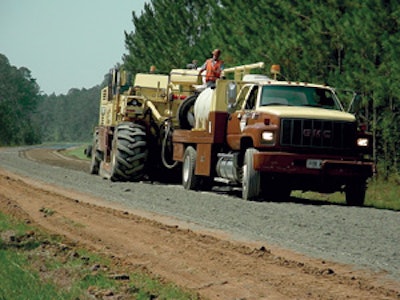
In 2005, The Miller Group Inc., based in Morrow, GA, completed 75 centerline miles of Full Depth Reclamation (FDR) for South Carolina's District 4 Department of Transportation. The northwest district consists of Cherokee, Chester, Chesterfield, Fairfield, Lancaster, Union and York counties. Many of the secondary low-volume roads were beginning to show their wear, with poor subgrade materials and some heavy truck traffic taking its toll on the structures.
FDR is a process that recycles the existing roadway along with a pre-determined depth of subgrade material mixed with an additive to form a new road base. For South Carolina's District 4, FDR provides a cost-effective way to improve and preserve secondary roads, allowing the road agency to address more road miles in less time and at a significant savings over conventional methods used in reconstructing roadways.
The FDR preservation approach also enabled District 4 to make the roads safer by widening many of the roads, some that were only 18-feet wide, to 24 feet — allowing for 10-foot-wide travel lanes and 2-foot-wide shoulders.
During the project, Miller Group processed approximately 450,000 tons of material, while only hauling 25,000 tons of Portland cement additive. Using a conventional reconstruction method, 600,000 tons of material would have been trucked out and into the project. But recycling the material on the project not only saved a considerable amount of money for the road agency, it also helped to improve the overall structural characteristics of the roads treated, with the DOT specifying the cement additive application rate of 48 pounds per square yard. The depth of the new recycle base was specified at 8 inches, but in some areas Miller's crews went deeper to fully blend deeper sections of pavement.
After the FDR based cured for seven days, Everett Dykes Grassing of Cochran, GA applied a chip seal surface treatment to the roads. The paving contractor applied a triple surface treatment — two layers of chip seal using a cationic rapid set emulsion and a final sand sealer coat to hold the aggregate chips in place.
Project scope
With 75 centerline miles (150 lane miles), Miller used two FDR crews to complete the work in five months. Each crew was able to process 1.5 lane miles of material each day. According to Dustin Stokes, a project engineer for Miller, the project presented a variety of existing conditions that FDR crews had to make adjustments to in order to deliver a consistent stabilized base.
"We were working on roads that were 18-feet wide, 20-feet wide and 22-feet wide, and we had to widen all the roads to 24 feet with the material on hand," Stokes says. "The roads were stone base with an asphalt surface that varied from 4-inches thick to 12-inches thick. The reclamation plan called for a recycled depth of 8 inches, but we went to 9 inches to make sure we were achieving a good blend of asphalt and stone base material, and in some cases we went deeper when we came across thicker pavement sections."
The cement additive was spread in front of the reclamation machine, which then blended the stabilizing material with the asphalt and subgrade material in a one-pass process.
Miller used a CMI RS500B and a Wirtgen WR 2500 S reclamation machines in the FDR process. Final compaction of the material was achieved with a Caterpillar pneumatic PS 150 roller and a Hamm 3412 smooth drum roller.
"We had no problem achieving the 95 percent compaction density required by the project specifications," Stokes says.
A good approach
John McCarter, District 4 construction engineer, says the FDR preservation approach makes a lot of sense for maintaining and improving "our farm to market roads."
McCarter, who has been with the District for 16 years, says the FDR preservation approach has been part of the District's road maintenance "toolbox" since 1995 and continues to grow in usage as an economical way to address more roads with limited dollars.
"We do some work on primary state routes (3,500 to 6,000 vehicles a day), but it really is ideal for some of our farm roads that might only carry 50 to 100 vehicles, or even 500 vehicles a day," McCarter says. "On the heavily traveled roads we generally apply a hot mix overlay, but on the rural roads with lighter traffic volumes, the chip seal is a more economical approach, and if increased traffic volume warrants it, we can always come back and apply a hot mix overlay."
While the number of lane miles targeted for FDR varies from year to year, McCarter says that when 15 to 25 percent of a designated road requires full-depth patching, it generally becomes a candidate for the FDR process.
"We have some roads, especially in York County, which is becoming more populated, that are deteriorating rapidly, and we're finding that FDR is a good way to bring those roads back and provide a stronger base for future improvements," McCarter says. "If we can also wait a few years after chip sealing an FDR road, it gives us some time to see if any other structural problems show up, and then we can fix those problems before we apply a hot mix overlay."