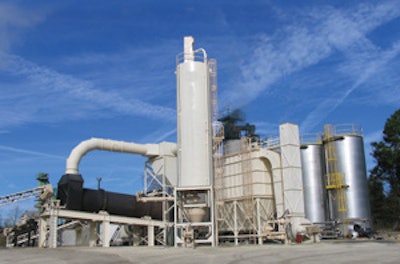
Since their inception in 1975, John C. Hipp Construction Equipment Co. has seen development in Alachua County, FL — and all of north central Florida for that matter — proceed at a breakneck pace.
In that time, the company has grown from a general contractor doing driveways, parking lots and subdivisions into a turnkey heavy highway firm regularly tackling large-scale private, municipal and state projects. While that growth has proven challenging overall, it has really impacted the company's asphalt production capability.
Faced with aging equipment incapable of meeting the ever-growing demand for asphalt, company president Virginia Johns recently made the most sizeable capital equipment investment in the company's history. The resultant purchase — a Milemaker 325 asphalt plant from Asphalt Drum Mixers Inc. has, in turn, made a positive impact upon both the company's capabilities and its long-term outlook.
Meeting the demand
The daughter of company founder John C. Hipp, Virginia Johns has seen the changes coming to North Central Florida for some time. The growth which has consumed the southern part of the state has been slowly working its way up I-75, driving property values up and making ever-larger demands on Hipp Construction's business.
"Until last year we were able to make do with what we had — but just barely," Johns says. "The demand for asphalt was steadily increasing, and meeting that demand was getting more and more difficult. Our plant was really showing signs of age and stress and though we briefly considered adding on to increase capacities, deep down we knew the route to take. We felt a new plant would give us the added capacity we needed, but also would provide additional benefits as well, including cleaner emissions, better consistency and lower maintenance, among others. We also saw that upping our capacities would enhance our ability to bid bigger projects; so we made the move."
Johns adds that their research into the right plant was fairly extensive. Eventually — based on both reputation and feedback from existing customers — they chose ADM to provide the new system.
"ADM invited us to visit several existing plants to see the equipment at work firsthand and to talk to users of their systems. We took them up on their offer, often politely asking the ADM salesman to leave us alone with the plant operators so we could get their input," she says. "Many of them had run several plants from different manufacturers and felt that the ADM plant was the easiest to operate and offered the best product control. We also met with lab technicians and plant managers, reviewed their process results and were impressed with the level of consistency they were getting. That coupled with the choice of high-quality components ADM offered as part of the system more or less did it for us."
More than volume
Situated just outside Gainesville, FL, the plant in place at Hipp's Alachua location — the ADM Milemaker — is state-of-the-art, built for versatility and designed with future expansion in mind. With a rated capacity of 325 tons per hour, it more than meets the company's current volume needs. Even though they've handled some extensive projects since installation, they've yet to max out the capacity of the new plant.
"In this area, we are hindered more often by the availability of trucks than anything else," she says. "So even when we've had a big project, we've never been able to see the full potential of the system. Even so, we are doing between 10,000 and 14,000 tons a month which is easily twice what we were producing before and that's been nice. But it's not just the volumes we are getting but the quality of the product that has really pleased us."
Johns says certain aspects of the Milemaker's controls, like its ease of calibration have already shown benefits.
"With some systems, calibration can be a time-consuming process which causes it to be seen as a chore and, as a result, performed less often. That's not the case here," Johns says. "Calibration for us is fast and easy, lessening the risk of our drifting out of spec even when dealing with Superpave. And that's been huge for us since it gives us a level of confidence that we never had before in bidding Superpave jobs."
Solutions in the drums
Hipp's geographic location lends itself to aggregates with a high moisture content being introduced into the system. To both alleviate that concern and maximize fuel efficiency, the Milemaker utilizes a dual drum configuration for separate drying and mixing. This serves to increase production while eliminating the hydrocarbon pollution source common with today's drum mix plants.
A sealed-in burner, counterflow drying drum ensures the lowest possible aggregate moisture levels prior to exiting the drum, while a separate mixing drum enables other additives, including RAP, to be introduced into an area completely isolated from the drying and combustion zones. This yields higher temperatures without unfavorable emissions in the exhaust gases.
And efficiency is also evident: Milemaker counterflow plants have been shown to require about 15 percent less fuel per ton to operate than standard drum mix plants — critical in light of steadily-rising natural gas costs.
"Improving our emissions was certainly one of our primary concerns in purchasing a new plant," says Johns. "And we have not been disappointed. This is an extremely clean system and we are having no trouble meeting regulations. In addition, the plant burns so cleanly that the bags in our baghouse have stayed clean and oil-free which will no doubt extend their life."
The baghouse — ADM's Model BH690 — is rated to supply 55,000 ACFM of required air volume. Like the rest of the system, it is designed to meet and exceed environmental compliance regulations. And like the system's other components, it is designed for ease of maintenance with easily-accessible bag changeout doors and a host of safety features.
Streamlining support
According to Johns, all the innovation in the world is pointless if there is no support for a large-scale asphalt system such as theirs. She says she was pleased to find out that ADM more than met her expectations in that regard as well.
"In this business it's inevitable that some of the high-wear areas will need replacement, and we wanted to make certain that parts would be readily available," she says. "Many of the components in the ADM Milemaker plant can be ordered from sources other than the manufacturer. As a result, we get a good deal of our replacement parts and components locally, which helps minimize downtime, and we can have a local technician perform much of the work, another nice plus for us."
Anticipating bigger things
With an eye to the future and an awareness that growth in the region will continue for decades to come, Johns and Hipp Construction designed the new plant to offer options and did so with eventual expansion in mind.
"The new system is extremely versatile in every sense of the word," says Johns. "By nature of the design and the components we selected, we can make a range of mixes available at any time. We have six heavy-duty feed bins which allow us to choose between different types, sizes and sources of aggregate. We also installed a pair of 200-ton silos which allows us to make two different mixes available simultaneously. And the plant itself is so user-friendly that we can be running a Superpave 12.5 for a crew, load one silo with that mix, then switch on the fly and provide a Superpave 9.5 for another crew."
That versatility, says Johns, extends to their ability to ensure easy expansion down the line. "Some would say we overbuilt this facility, but we don't feel that's the case at all. As the years go by, we are going to need to continue to increase capacities, and by designing it in this way, it will be very easy for us to add silos, bins, tanks, and so on, as we need them to ramp up production. We already have more than enough burner and baghouse capacity so we can be ready for almost anything. We've really been pleased both with how far we've come and with what lies ahead."