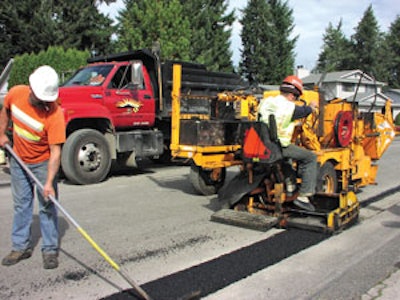
Of all the various pavement maintenance technologies, the one that has arguably seen the greatest innovation in recent years is repair of potholes and repair of utility cuts. While research indicates that the strongest repair is still a saw-cut remove-and-replace patch, developments on both the equipment side and the material side have resulted in cost-effective alternatives that are reliable and that enable even more contractors to offer these repairs to their clients.
Contractors looking to test the pothole repair market can get involved for the low cost of some basic hand tools and a 5-gallon bucket of proprietary cold mix. But contractors looking to get involved in pothole repair, general repair of pavement defects, and repair of utility cuts on a larger scale – working contracts with cities, counties, and those who handle multiple large-scale parking lots – can also add equipment to their fleet.
The key for adding equipment is production. If you're going to invest in equipment you have to keep it busy enough to justify its cost. So contractors with clients who provide work on large areas of pavement can consider machines that are designed specifically to repair potholes and utility cuts. Contractors who don't have as many potholes to fix or steady contracts with utility companies to repair their cuts might consider other types of equipment that is more versatile, such as asphalt maintainers or infrared machines.
John Alcorn, vice president and co-owner of AA Asphalting Inc., Sumner, WA, banks on repairing utility cuts as part of his company's steady work. The contractor operates from four Washington locations, employs 90 people, and runs seven asphalt crews and three concrete crews. Much of the company's work involves utility cut repairs, and Alcorn says 60% of all utility repairs are for the gas company.
To keep its utility repair work on schedule the company relies on two Leeboy 1200 S asphalt maintainer/patchers, which Alcorn says keep production up and costs down. Alcorn says he and Jeff Jewett, president, started their business in 1978 and bought their first of two asphalt maintainers in 1988. They've become an integral part of the AA Asphalting fleet ever since.
The maintainer/patchers are unique machines that incorporate a number of pavement repair or maintenance features into a single piece of equipment. The towable 1200 S includes a 24-inch rotary grinder, a paving screed that telescopes from 38 inches to 62 inches, a shoulder-building attachment that extends from 28 inches to 42 inches, and a 100-gallon tack tank.
Alcorn says the grinder can be raised and lowered, which enables the crews to remove material from the cuts when necessary as well as to grind up existing fill and place it right back in the repair. He says the screed can also be modified to pave a strip as narrow as 2 inches to 24 inches wide.
"That's a great advantage when repairing utility cuts, especially when we are repairing trenches," Alcorn says.
The unit operates much like a paver in that dump trucks deposit hot mix into the maintainer's 2 ½-ton hopper as it moves along the job. The mix flows to the screed or shoulder extension, enabling the operator to fill utility cuts. The same process also is effective for shoulder reconstruction and for road widening.
"If there's a ditch and it needs two feet of gravel on the edge of the road for several miles, this is the machine to use for that," Alcorn says. "So if you're doing anything alongside the fog line of the road, such as putting a rock mix to the right of the tires, you can drive on the hard surface and fill the shoulder or other area off the hard surface. You simply line up your trucking, you set the maintainer up with its wheels on the hard pavement surface, and you move on down the road."
If a repair is on the opposite side of the road they simply turn the machine around and work the opposite direction.
He says utilities in the state have been hard at work replacing network cables and power conduits in continuous trenches that are 18 inches wide. The utilities immediately fill the completed repair with a sandy concrete so the roads can be opened to traffic. He says state law in Washington requires some construction or repair work on main roads to be done at night, so it's especially important that AA Asphalting's crews be as productive as possible during the restricted work times.
"We follow the utility companies and whatever they rip up, we replace," Alcorn says. "We come in with the maintainer and grind down 3 inches and 18 inches wide and we just keep moving on the repair. We can do anywhere from 1,000 to 1,500 lineal feet a day."
Alcorn says that while it's difficult to say when the asphalt maintainer will or will not be used on a job, a job with a 2-foot-wide trench running 300 or more feet long would almost certainly benefit from a maintainer.
"We would bring it in on something like that for sure," he says. "Doing it by hand would be so much slower. We can do 1,000 feet in four hours with the maintainer."
He says the maintainer is also valuable when utility cuts are deep enough to require two or more lifts of mix. Without the machine smaller patches would have to be constructed, but because the maintainer can deliver mix at a higher rate of speed, larger patches can be completed each time out, making the job more profitable for the contractor and making the utility and the driving public even happier.
"This is a production machine, it's too much trouble for smaller patches," Alcorn says.
Versatile spray patchers
Another approach to higher production pavement repairs is spray-injection patching, which is available from several manufacturers in a variety of trailer and truck-mounted units. While the machines have their differences, they operate on variations of the same theme: the equipment cleans the pavement to be repaired, applies an emulsion tack coat, and stone is fed into the hopper from an aggregate holder. The stone is coated with a proprietary emulsion, and the coated stone is sprayed into a pothole or onto a repair with a high degree of force. This high air velocity provides compaction and density.
"This is not necessarily the ultimate or optimum repair, but it is a very quick and effective pavement repair," says Mark Manning, vice president of Crafco Inc. "Contractors selling this repair have to know exactly what they're repairing and why."
Crafco, for example, manufactures three spray patching units: the Magnum, an auger-fed higher-tech, higher production machine and the smaller air-fed AirStream and AirStream Truck-Mounted units. The towed AirStream can place 4 ½ tons per hour while the truck-mounted unit can place more than 5 tons per hour and the Magnum 7 tons per hour. Manning says the auger-fed Magnum moves roughly 50% more material than the AirStreams, though all models can be used for most types of general spot repairs, including potholes, failed chip seals, skin patches, repair of alligatored areas, sunken areas, and repair of crumbled shoulders.
"To determine whether or not buy a spray patching machine contractors need to take a good look at the type of work they're doing and are likely to do," Manning says. "The profitability of the machine depends on the applications it's going to be used for."
He says contractors also need to determine an hourly rate for running the equipment, and then they need to realistically apply that rate to their expected production.
"A rate per hour, regardless of what it is, only indicates what a piece of equipment will produce for the hour it's working, but you can't necessarily project that out across a full day," Manning says. "If you're repairing potholes on a roadway, for example, all the potholes are not in one place. So you fill one, then drive down the road to the next, and you might only have one pothole every mile or so. And while the unit is moving from pothole to pothole it is essentially not being productive."
But he says the versatility of spray patching machines is what can make them so valuable to contractors and agencies alike.
"This type of repair equipment is ideal for cities and counties and for contractors who do a good amount of work for cities and counties," he says. "It's not a piece of equipment that does only one thing or that can be used on only one type of repair."
He says counties are big buyers of the spray patching units "because they can take it out on the road and repair virtually any defect they encounter along the way. It's not ideal for an interstate," Manning says. "They are much better suited for low-volume roads and on off road, parking lot repairs."
But he adds that it would be difficult for a contractor to justify its purchase filling only potholes in parking lot pavements. He says contractors considering buying a spray patching unit should be sure they have repair contracts for a large number of parking lots and probably some low-volume roads to make sure to keep it busy.
"It's too expensive to take out of the yard only once in a while," Manning says. "You need to keep it busy and that's why contractors who are involved in repairing roads are ideal candidates for this type of equipment."
Infrared repair
Contractors have also recognized the value and versatility of infrared repair equipment, originally introduced years ago to make surface repairs to alligatored pavement and potholes. But as infrared equipment becomes more common in contractors' fleets, contractors are finding more uses for it.
"Contractors are starting to become more aware of what infrared can do," says Wes VanVelsor, president of Raytech Infrared. "I have customers who have never done a pothole with it. They focus on things that nothing but infrared can do."
He says that among the repairs infrared is now used for are tripping hazards where asphalt meets concrete and around manholes where the lip meets the grade, removing asphalt from concrete, and repairing birdbaths in newly paved jobs.
"There are things you can do with infrared that you can't do with anything else, and birdbaths are a good example," VanVelsor says. "You can't really repair them any other way because you can't feather hot mix asphalt. It just chips off."
He says that not only are pavement repair contractors putting infrared machines to effective use, but paving contractors of just about every size are buying infrared machines to repair their own mistakes.
"Comparatively it's not an expensive piece of equipment so it's a tool that they can buy so they have it when they need it and it's very effective," VanVelsor says. "And it pays for itself very quickly. They might not use it every day but when you do it pays for itself."
He says infrared equipment also can be effective when repairing utility cuts. He says that whether the utility contractors make temporary or permanent patches, infrared can be used to improve the finished result.
"Most gas companies will make a repair and then fill the area back with a temporary cold patch. If that's the approach contractors can go in, remove the temporary patch, and install a permanent patch," VanVelsor says. "In that case, once the temporary material has been removed, through the use of a reflection, we can heat both sides of the asphalt pavement. It is then scarified, base material placed, compacted and finished in the normal way."
He says in the cases where the utility itself constructs a permanent patch the contractor should make sure the utility constructs the patch at least 3/8 inch below the pavement surface.
"That's so we have room for new mix. Some utilities only want contractors to come in with infrared and repair the joints because that's what people have the most problems with, but we can improve the repair even more with infrared if we can add fresh material."
VanVelsor says that along with an infrared machine contractors also need to use a hot box, which keeps extra mix hot for use in repairs. Hot boxes are sold separately but also are available with infrared in combination units.
"You can't use cold mix out of the back of a truck when making these repairs. You need to keep it at about 280-300 F which is what you're heating it to with infrared," VanVelsor says. "The new material being the same temperature allows it to flow with the existing material for a proper patch."