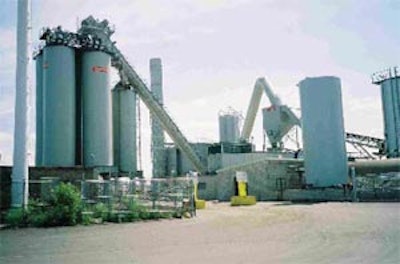
In the competitive Chicago market, having the best equipment is essential for the survival and growth of any asphalt producer, says Greg Rohlf, general superintendent of Plote Construction Inc. And when the City of Chicago acquired the company's Des Plaines' location to accommodate the expansion needs of nearby O'Hare International Airport, Plote used the relocation to Franklin Park (south of O'Hare) as an opportunity to replace its 15-year-old Bituma asphalt plant.
Plote owns six plants — a CMI, an Astec, three Gencors and a new Dillman DuoDrum — in the Chicago area, and as Rohlf, who has over 40 years of experience in the industry, put it: "We expect a lot out of our plants. When we invest in a plant, we expect to get 10 million tons of production out of it before we have to replace it."
The old Des Plaines' plant was a Cedarapids/Standard Havens, which Plote sold prior to finalizing the purchase of its new Dillman plant. With a good cross section of various plant brands, Rohlf and Plote had ample experience to determine what they wanted out of a new plant.
"When we were evaluating different plants on the market, we narrowed our decision to what we consider the heaviest (materials used to construct plant components) and highest production capabilities, and we decided we would either buy another Gencor or a Dillman," Rohlf says. "We've had good luck with our Gencors, but the Dillman offered more heavy iron (beefier construction), the fuel savings we were looking for, and we were able to get want we wanted at approximately 10 percent less than any other comparable system."
Plote finalized the purchase of its new plant in January 2005 and had the system up and running by the end of April.
"We wanted to increase production, have better control over the various mix designs we produce, lower our energy consumption with a system that allows us to burn waste oil along with natural gas, and lower the emissions produced," Rohlf says.
The plant
The Plote/Allied Dillman plant is not a standard off-the-shelf plant. It is customized to the demands the asphalt producer places on all its asphalt facilities.
The Dillman DuoDrum 600-plus tph counterflow plant Plote purchased not only includes the heavily-constructed components that are standard features, but added liners and beefier wear items to accommodate the production and reliability demands the plant will be subjected to in years to come. Equipment put in place includes:
- An eight-bin virgin cold feed system with a self-contained collector conveyor, a double-deck Deister Aggregate Screen and an aggregate scale conveyor.
- A two-bin reclaimed asphalt pavement (RAP) system with self-contained collector conveyor, double-deck Deister Recycle Screen and recycle scale conveyor.
- A 600-tph dryer system with trunion-driven aggregate dryer assembly and a Hauck EcoStar ESH-200 oil/gas burner.
- A DuoDrum mixing system with Dillman's exclusive Rotovator and Safety Guards.
- Pollution control equipment featuring a 140,000 cfm heavy duty pulse jet baghouse.
- Dust handling equipment featuring a Mel Pod dust auger, a skid-mounted surge pod, an 18-inch rotary airlock with AC Drive, a 50-hp air blower, a 2,800-cubic-foot atmospheric silo, a vane feeder and dust delivery auger to DuoDrum.
- A two-room split control module that houses the DEI Innovative Controls' blending control system.
- Mix handling equipment that includes five 300-ton storage silos, a 600-tph main slat conveyor with reject chute, a 600-tph three-way horizontal transfer conveyor, a 600-tph two-way horizontal transfer conveyor, and a 600 tph two-way horizontal crossover conveyor.
- AC tanks and heaters that include two 30,000-gallon vertical single compartment AC tanks, a 2,000-gallon Meeker Equipment liquid additive tank, a 1,000-gallon vertical calibration tank, and a Meeker Equipment HV-160-CMC 2.0 BTU heater.
First season evaluation
With only one season under its belt, the jury is still out on whether or not Plote achieved everything it hoped to with its new plant, but Rohlf is pretty confident it will produce a lot of mix for years to come.
" We ran between 300,000 and 400,000 tons through the plant the first year and we were pleased with how the plant performed," he says. "The counterflow aggregate drying system is designed so that the RAP can be added in the back end of the drum, which allows for more time to heat up the material with the virgin aggregate before moving it into the mixing drum.
And with the mixing drum rotating faster than the drying drum, the system seems to produce a very good quality of mix."
Rohlf also likes the capability of burning two different fuel sources. The dual burner operates off a natural gas pilot, with a dual waste oil burner that provides the main heat source for drying and mixing.
"We can run both burners in the morning to get the system up to operating temperatures and we can also run both burners whenever the aggregate has extra moisture content, and at the end of the shift we can just switch over to the waste oil burner exclusively (which helps keep the burner lines clean)," Rohlf says. "I also like the longer mixing drum because it seems to do a better job of isolating gases and burning off those gases. Environmental requirements are getting tighter all the time, and with the 100-foot stack we have on this plant, we had no complaints from our neighbors regarding blue smoke or odor. We were concerned about that issue and that's why we oversized our baghouse."
With much of the mix produced at the plant sold to independent contractors, it's not uncommon to produce five or six different mix designs during the day. The plant is equipped with five 300-ton customized silos and an additional 200-ton silo, and it was designed to accommodate additional storage silos if production demands warrant it.
Everything about the plant is oversized or overbuilt for reliability and to deliver more production down the road.
The 600-tph drum capacity is really built to produce 660 tph. Plote operated the plant at 550 tph this past paving season. Heavier liners in the cold feed and RAP bins, as well as heavier liners and flighting in the drying and mixing drums were added for production reliability. Modifications were also made to beef up the slat conveyor system and the liners in the storage silos. The plant is also designed to accommodate up to 50-percent RAP in the mix designs produced in the DuoDrum system
"There's a lot of recycled asphalt generated in refurbishing streets and other paving structures throughout the city, and we're allowed to use a fair amount of that recycled material in the new construction of those projects. If you grind up two inches of old asphalt, 35 percent of that material goes back into the new mix. So, having a plant that can handle various RAP requirements is a must," he says.
And while the final numbers on fuel savings haven't been identified, Rohlf says the first year of operation generated at least a 5-percent savings in fuel required to produce the same tonnage with the old plant.
With three Plote plants producing similar annual tonnages, the new Dillman is the first to operate with a waste oil burner, and Rohlf says time will tell how the plant stacks up with Plote's other workhorses.
"It was a sizable investment for us, but we look at it as a 20-year investment," Rohlf says. "We're used to getting 10 million tons out of plant, so that's the thought process that went into selecting this plant and making the modifications we made for long serviceability. I think we bought a good chunk of iron."