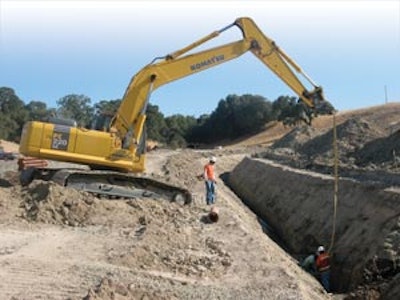
Last year saw diesel fuel prices reaching record highs, with prices spiking well above $3 a gal. in some parts of the country. And while fuel prices have eased over the past several weeks, global demand is almost guaranteed to push them back up as we approach the peak work season.
Given this scenario, cost control is even more crucial to ensure the continued profitability of your business. This includes making sure all of your equipment — including excavators — are operating at peak fuel efficiency.
Fortunately, manufacturers are making this easier via more fuel-efficient designs that deliver higher engine horsepower and improved hydraulic performance.
“Excavator manufacturers are continually trying to improve their machines to reduce operating costs and improve fuel efficiency,” says Mark Wall, product marketing manager - excavators, John Deere. A key focus has been getting maximum production out of the machine. “We always try to maximize cubic yards per hour. By moving more dirt per hour or helping to put more pipe in the ground in a day, we are improving the customer’s efficiency and lowering his cost of operation.”
More power, less fuel
“Individual owners have to look at all the manufacturers and pay particular attention to engineering,” advises Tony McGreavy, asset manager at D’Allessandro Corp., Avon, MA. D’Allessandro Corp. specializes in underground construction and site preparation. Its 22 excavators range from 10,000 to 100,000 lbs. and consist primarily of Komatsu units, plus Caterpillar, Deere and Volvo models. “Certain manufacturers are making big breakthroughs in fuel economy faster than others,” he adds.
Excavator technology is improving on an almost daily basis, says Dave Pooley at Hyundai. “With the introduction of Tier II EPA engine laws several years ago, engine manufacturers had to do some creative fuel design changes,” he explains. “The changes included electronic fuel delivery systems, which react much quicker in delivery, and governor control. The overall result is a more fuel-efficient engine that emits less pollution into the environment.”
“The EPA has led all manufacturers to really invest in R&D to meet the [emissions regulations],” agrees Peter Robson, hydraulic excavator product manager, Komatsu America. At the same time, his company had the goal to improve fuel economy even further. This led it to move away from mechanical fuel injection. “Now we have gone to the high-pressure common rail fuel injection system, which has fully electronically controlled injection timing.”
Advanced engine electronics have enabled manufacturers to introduce more fuel-saving features, such as the auto idle mode. “If an operator allows a machine to stand unused for a period of time, the engine will automatically go to low idle, and therefore use less fuel than if it were continuing to run at higher rpms,” says Lowell Stout, product manager for Terex excavators.
Changes in cooling system design are also contributing to better fuel economy. “These new systems use advanced technology in cooling core designs, along with high-performing fans that feature air foil blades,” says Wall. “These new fans use less energy than on prior models. This is energy that can be available to move dirt or to help improve fuel economy.”
These advancements combine to more economically deliver the same or more power. “They burn less fuel,” attests Calvin Thompson, a 30-year veteran equipment operator and owner of Thompson Grading, Dallas, GA. “For the rpms, you get more horsepower.”
This translates into greater productivity, while consuming less energy. “The biggest change I see in the excavators is the speed in which they dig,” says Thompson. “You have higher-output engines and you have higher-output hydraulic pumps. Time is so critical in this business. And it doesn’t take you as long to accomplish a project. ”
Improved modes of operation
Improvements in hydraulic systems are also playing a significant role in maximizing fuel economy.
According to Wall, load-sensing hydraulics have perhaps contributed the most toward improving excavator fuel efficiency. “They have less demand on the engine and therefore reduce fuel consumption,” he says.
Manufacturers are also incorporating more sophisticated hydraulic functions that allow the operator to adjust hydraulic flow to the application. For example, hydraulic upgrades on Hyundai’s latest models include selectable modes to optimize available hydraulic speed and power, plus a manual throttle dial to adjust engine speed and power as needed. “Or put it in the automatic modes and the computer will handle the rest,” says Pooley.
Many excavator designs incorporate an Economy mode. “By putting it in the Economy mode, you still have many of the same abilities as in Power mode,” says Robson of Komatsu excavators, “but fuel efficiency is going to be greatly increased. You can see anywhere up to 10%.”
Wall claims the fuel savings on Deere’s C-series can be even higher. “Tests conducted by Deere show that operating in E (Economy) mode can improve fuel economy by as much as 20%,” he states. The units also feature an Auto-Accel mode that varies engine rpm according to system pressure. “In light load applications, this mode can save the owner approximately 10% in fuel, reducing owning and operating costs.”
For its new Dash-8 models, Komatsu has incorporated an upgraded “multi-monitor” with an Eco gauge, initially available in the 220 size class. The gauge is essentially an energy-saving guidance system. “If it senses the machine is working light, it’s going to report that you’re in an Economy range,” Robson explains. “It’s monitoring the load factor on the engine and reporting it back graphically to the operator.”
Features that enable the operator to properly match engine and hydraulic performance to the job ultimately improve fuel efficiency by prioritizing functions, rather than trying to provide peak performance on every working function of the excavator, Wall points out.
Of course, it’s up to the operator to choose to utilize these features. “The work modes save fuel because the engine doesn’t have to work as hard,” says Jon D’Allessandro at D’Allessandro Corp. However, his operators use them only about 30% to 40% of the time. “If they’re doing some backfilling of trenches, pavement preparation or grading around a building, they’ll put it in a different mode where it’s a little more sensitive. It’s more responsive for them. But if they’re craning, they will run them wide open so they have the power and responsiveness they need.”
Beyond fuel efficiency
D’Allessandro feels it is important to review manufacturer statistics and compare fuel efficiency ratings between brands. However, he cautions that fuel efficiency is not the only criteria to consider. “I like to buy the machines that I know are tested and true, and I’m a big proponent of zero tailswing machines,” he states. “I’m getting my efficiencies and economics through other things, not just fuel.”
McGreavy agrees, adding, “It really comes down to the individual owner and what they’re looking for. Are they looking for pricing? Are they looking for fuel efficiency? Are they looking for operating cost over the lifespan of the machine? Or are they driven by brand loyalty? That’s the question a lot of people have to ask. You have to have an open mind and look at the entire picture.”