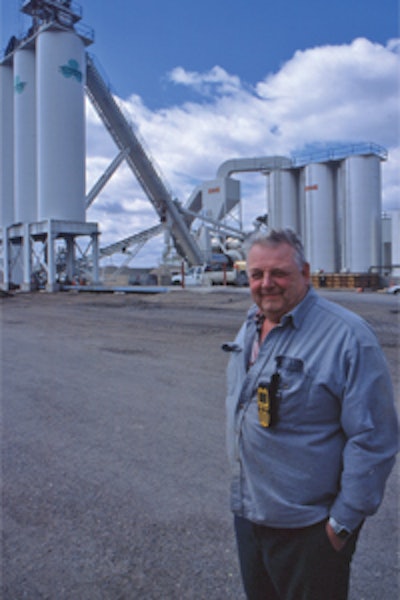
Veteran hot mix asphalt producer Lloyd Vivant has used his knowledge and experience to get the most out McNamara Contracting Inc.'s HMA plant located south of Minneapolis. In fact, Vivant's preventive maintenance approach was featured in a January 2004 article in Asphalt Contractor. At the time, Vivant was operating a 32-year-old Barber-Green batch plant, which had been converted to a continuous flow process, along with numerous other upgrades over the years. But a decision had been made to replace the plant when the company moved operations in order to make way for a new residential development.
Vivant's knowledge of HMA production and research of existing HMA technology both played an important role in his final selection of a Dillman DuoDrum plant.
"I really didn't like the way RAP (reclaimed asphalt pavement) is added to the mix on most plants that are out there," Vivant says. "I like the Dillman DuoDrum's separate mixing drum design because it gives you more time to add your RAP to the virgin aggregate."
Along with the mixing drum design, Vivant also liked the construction of the Dillman plant and what he considered a good price for the way the plant was constructed.
Other considerations, like the DuoDrum's high production capability of 600 tph, rugged construction, reduced maintenance and fuel costs, low emissions and low stack temperatures, ability to run high RAP percentages, handle Superpave and other specialty mixes, and its portability also played in McNamara's decision to buy a Dillman.
"I really like the separate drum design, with the first drum dedicated to drying the virgin aggregate and adding RAP, and the second for mixing the asphalt cement to the mix," Vivant says.
With one full season of production using the new plant completed, Vivant notes favorable results with the exceptions of a few glitches that occurred during startup, along with a few other minor maintenance items that needed to be addressed.
"We did have some loose bolts that needed to be replaced and took a little while to get used to the heating time of the new plant. On the first day I had no idea how hot the burner should be. With our old plant it took about two minutes to see a temperature change. With this plant, it takes about six minutes, and that's due primarily to the fact that this plant has a longer drum," he says.
Some adjustments were required to the software used in the control room to synchronize temperature and other plant functions, but once the adjustments were made most of the initial glitches were addressed.
"When you add 50 degree RAP to 400-degree virgin aggregate, you get an initial explosion when the moisture is released and evaporates from the RAP. It takes about 80 seconds for the RAP to be brought up to the temperature of the virgin before it can be dumped into the second drum and the AC can be added," Vivant says.
"That took a little getting used to on my part. I was trying to adjust the temperature when I noticed that it dropped after the RAP was added, but then it was too hot when the AC was added," he continues. "So, I just needed to let the plant do what it was designed to do in heating up the RAP and not make adjustments to the temperature. Now I just watch the stack temperature and make adjustments based on the temperature coming out of the stack.
"We had a lot of little problems during the first month, and most required minor adjustments in the software we're using," Vivant adds. "We had problems with wet batches (too much AC) and we'd make adjustments, not see a problem for week or so and then it would show up two or three times in one day. We corrected the problem by switching our AC control from automatic to manual. We found out in the automatic mode that the system was overcompensating (adding too much AC) whenever it took a reading on a large clump of aggregate. Now our computer system is set up to add AC only if the required change last longer than 10 seconds."
Vivant and his plant crew also had to work out a few glitches with the scale load out system and surge system which controls the flow of dust from the baghouse back into the drum.
"The scale load out problem required a computer programming change that would process information faster and the surge problem required us to speed up the vertical auger to prevent clogging," he says.
More efficient
With a 600-tph production capacity, compared to McNamara's old 450-tph plant, the larger plant is more efficient than the one it replaced for several reasons. The Dillman plant has a larger baghouse which facilitates better airflow through the plant.
"We don't need the capacity now, but we bought the larger plant based on future growth objectives, and after operating for a year we realize it's more efficient to run," Vivant says. "With our old plant we were operating at about 250 to 275 tph and with the new plant we're running at about 350 tph. What that meant for us last year was that we did not have to run the plant as many hours to produce the same amount of mix we produced in the previous years. That efficiency resulted in lower fuel costs and lower labor costs to operate the plant. The net result was a lower cost per ton to produce the mixes we turned out."
The other significant cost savings achieved with the new plant is the result of switching from a natural gas fired operation to a heating oil fired operation. The plant uses a combination of #6 heating oil and natural gas to dry aggregate. Normally the plant burns 90 percent heating oil and 10 percent natural gas, unless the aggregate has higher moisture content. Then Vivant backs off on the heating oil and increases the natural gas.
"There are more BTUs in heating oil, but the combination allows us to maintain a more consistent burner temperature, and when the aggregate is wetter, we can increase the natural gas for a dryer heat," Vivant says.
The combination burner does require a little more maintenance in the way of daily inspections to make sure there's no oil residue buildup to clog the burner and the system does have temperature monitors on the burner to detect any possible problems. Vivant would like to add some TV monitors to facilitate an easier visual inspection of the burner.
The only other added maintenance Vivant has noticed with the new plant is additional inspections required to make sure the chutes and drums are clear of clogs.
"The drums have a tendency to clog up a little more often, and I'm not sure why. It may be the way the flights are designed. It's not a big issue, just something we have to make sure we check on a regular basis," he says.
Additional efficiencies have been gained with three 300-ton storage silos to accommodate various mix designs and an automatic ticket dispenser for truck drivers after they've been loaded.
"It allows us to keep the truck drivers in their trucks and move them in an out of the plant a lot quicker," Vivant says.
Eight cold feed bins for virgin aggregate and two cold feed bins for RAP have also improved the overall efficiency of the plant. Ninety-five percent of what McNamara produces at the plant is used to support its two paving crews working on state, county and new city development projects.
Although final cost comparisons of what the company has saved on fuel and labor with the new efficient plant have yet to be compiled, Vivant is confident those numbers should be significant and provide a good projection of what the company can expect to save in the years ahead. Overall maintenance costs should remain low for the first few years of operation since the plant is new, but Vivant is making a few upgrades to accommodate the abrasive nature of the granite river rock used in McNamara's HMA production.
"We're beefing up some of the liners in the chute where the aggregate enters the drum and we're going to add some inspection doors to make it easier to get at some components, but that's about all we're planning to do at this time," Vivant says. "I think this is the plant that will serve our needs for a long time to come. With our old plant we would spend five to six weeks a year to maintain it. I think we should be able to take care of all our maintenance needs in two to three weeks for the foreseeable future. We hope to produce a lot of mix with this plant."