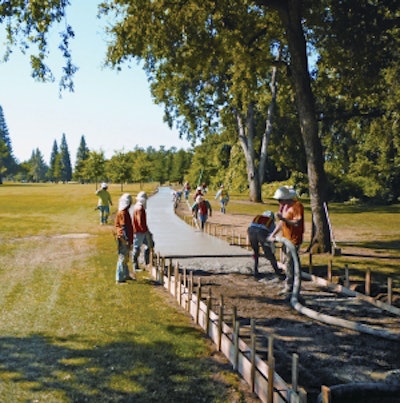
The Challenge:
Reconstruct a half-mile long cart path without closing a premier golf course during construction.
The Players:
Cedar Valley Concrete (CVC)
Western Ready Mix Concrete Co.
Bob's Concrete Pumping, Inc.
The Process:
The Butte Creek Country Club (BCCC) in Chico, Calif., is a private 18-hole championship golf course. The club has limited memberships to ensure golfers can play when they want. So when an old asphalt cart path on hole nine needed to be replaced with a new concrete one, the country club's board of directors voiced concern over closing the hole.
"We needed a strategic plan to complete the job in four days, without major interference with the golf course’s normal operating schedule and keep the area extremely clean throughout the construction process," said Cedar Valley Concrete (CVC) Regional Vice President Dave Carrick.
The 2,500-ft. golf cart path was long with sharp winding curves and no available access to the course for equipment setup. At a planning meeting, it was decided to remove asphalt one day and pump concrete from two staging areas the next two days. From the first staging area, concrete would travel through a delivery line system at a distance of 1,060 ft. with the remainder of the concrete path poured the following day, from the second staging area. Bob Bauman, owner of Bob’s Concrete Pumping, Inc. (Bob’s) in Chico, California, was contracted for the concrete pumping. He selected a Putzmeister BSA 120-D trailer-mounted concrete pump for the job.
Specifying a mix design was extremely important to effectively pump concrete the far distances required without plug-ups, yet still attain a set time requirement of 3,000 psi in 28 days. Vice President Craig Zelie of Orland, California-based Western Ready Mix Concrete Co. (Western) was called upon for his recommendation. The result was a special mix containing four major ingredients including: 1,529 lbs. 1-in. rock, 1,484 lbs. of sand and six sacks of cement. Sixteen ounces per cubic yard of V-MAR 3, a new generation liquid admixture designed to increase the cohesion and stability of extremely high workability concrete, was also added. V-MAR was used in conjunction with the superplasticiser ADVA Flow 300 to produce self-compacting concrete, which maintains self-compacting properties while preventing segregation. To prime the system, Western used 1 cu. yd. of four-sack sand slurry to help prevent plugging the system.
Since the cart path was not a straight line, the delivery line system had to curve with the direction of the meandering pour. The crew connected 180 ft. of 4-in. pipe, 680 ft. 4-in. hose and 200 ft. of 3-in. hose for delivering concrete during the first pour. Ready mix trucks were scheduled 15 minutes apart.
Concrete was placed at a maximum 5-in. slump. The BSA trailer pump, averaging 32 cu. yds. per hour while operating at a 3,700-psi hydraulic pressure, rapidly placed 130 cu. yds. of concrete in about four hours for the first pour, which was faster than planned. And it was accomplished without closing the ninth hole.
Adding 120 ft. of 3-in. hose to a similar setup as the day before, the trailer pump placed 156 cu. yds. of concrete at a maximum distance of 1,180 ft. the following day. "The BSA’s long-distance pumping capabilities meant we could quickly and cost-effectively place all the concrete in two days instead of three," Bauman says. The fourth day was reserved for form removal and final cleanup.