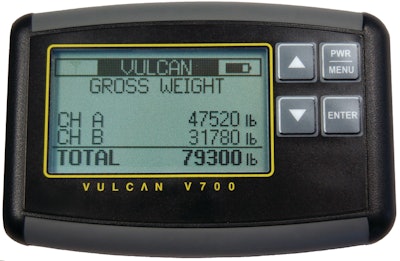
Nobody wants tickets for overloaded trucks, yet you can't afford to let under-loaded trucks leave the jobsite. Onboard weighing systems provide the solution. You can maximize your legal load, and save time loading, weighing and reloading. These systems also eliminate maintenance and liability issues due to overloading.
Eric Elefson, director of marketing and sales, Vulcan On-Board Truck Scales, explains that truckers using onboard scales reap benefits far beyond just monitoring gross vehicle weight (GVW) to avoid overweight fines. "Given the high cost of time and equipment, onboard scales dramatically impact the efficiency and profitability of operating a truck," he states. "For instance, you reduce fuel usage by hauling at capacity for fewer trips."
Adventure Trucking LLC, Clackamas, OR, has a long history with onboard scales and made the switch to its current LoadMan system in 1995. The company owns seven of its own trucks and contracts another 40 to 50 dump trucks, including trucks and pups and a couple of semi end dumps. "All of the trucks and trailers have the system," reports Brock Chandler. "I am not going to run anybody who does not have [the onboard scales]."
The benefits are immediate. "A 3,000-lb. overload ticket costs $4,000," says Chandler. "You get a couple of tickets annually, it is going to easily pay for that set of scales. For the most part, we don't get any more than one or two tickets a year and we go over state scales every day."
The productivity jumps by getting the load right the first time. Many pits will not let you leave if you exceed maximum GVW. "Then you waste time going back to dump some," says Chandler. "If you have to run back and forth, you can blow 20 minutes pretty easily." With the onboard scales, you get the load right. "Not to mention you are increasing the amount of load you are hauling in less time. They are probably the best investment there is for a truck."
Carefully tracking weights is important to Adventure Trucking, especially since it operates in several states with different weight limits. "We run all of Oregon, Washington, Idaho, Montana and Utah," says Chandler. "We have been to Wyoming. None of the states are the same." In Oregon, trucks are limited to 105,500 lbs. "We go to Utah and run 112,000 lbs." These systems allow the company to maximize its payload wherever it goes.
"Onboard scales allow for loading to desired capacity at any time and nearly anywhere," says John Riley, senior manager, SI Onboard. "Weight can be observed at the point of loading. Therefore, the additional time and effort required to seek out the nearest ground scale becomes an inconvenience no longer experienced."
The more accurate the scale, the more productive you can be. "With onboard scales similar to what we have at TruckWeight, you can typically load to within 1% of maximum payload," says Peter Panagapko, president, TruckWeight. "That will translate to about $10,000 to $20,000 per year in increased revenue considering that most loads run between 5% and 8% under weight of maximum legal GVW. The savings apply to fuel and other expenses related to operating the vehicle. These are significant gains in productivity and it improves the overall efficiency, providing real and significant improvement to the bottom line."
Stationary scales do not improve loading efficiency. "Even when dump trucks load in quarries where there are platform scales, they don't get loaded on platforms," explains Alan Housley, LoadMan. "Therefore, if they are under loaded, they simply leave. If they are overloaded, they pull off to one side and tip material out, then get back in line to be re-weighed ."
There are many circumstances where an onboard scale benefits the operator even when stationary scales are present. "For example, when loading in a pit that has an in-ground scale, but not at the loader, you maximize your payload prior to reaching the scale, avoiding a situation where you have to get back in line to top up or go back and dump some out due to an overweight event," says Panagapko. "Operators can increase the number of loads in a day and increase the per trip payload with an onboard scale that computes the weight right at the loading area."
It is just as important to get the load distribution correct. "Onboard scales have the ability to provide axle group weights, as well as the total vehicle weight," notes Riley. "Therefore, the axle groups weights can be used to assist in load distribution."
It usually does not take long for the onboard scale to pay for itself. "ROI is variable between applications," says Riley. "It is usually reached in a time frame that justifies the allocation - sometimes in as little as a few weeks."
Systems vary in cost and features. "A typical cost to scale an over-the-road dump truck is roughly $4,000," says Housley. "Contractors realize their return on investment by maximizing payloads no matter what they load, eliminating out of route travel to jump scales."
"Our TruckWeight Smart Scale ranges from $900 to $2,400 to outfit a commercial rig with mechanical or air suspension," says Panagapko. "Operators who are paid by the ton realize a return on investment in less than three months for most operations. If they are paid by the mile, the return on investment is less than one year for most operations."
Coordination with Loading Tool
Careful communication between the truck driver and loading tool operator yields maximum payloads with minimum effort. For instance, the loading operators know Adventure Trucking has these systems on board. The drivers will use CB radios and hand signals to increase loading efficiency.
"They know to watch us," says Chandler. "We hold up one finger for 1,000 lbs. or three fingers for 3,000 lbs. If the loader operators are close, within a few thousand pounds, then they slow down quite a bit." And if the truck gets slightly overloaded, the driver doesn't have to drive to the scale to find out. "We just back up to the pile and trickle a little bit off."
Some systems allow the loader operator to carefully monitor the load. Housley reports the LoadMan allows the loader operator to easily assess the load on a given truck. "After getting the first shovel/bucket load, they raise their dump bed to the weighing position, then with each additional scoop, it takes 2 to 3 seconds for the LoadMan system to display the added weight by axle groups. These weights can be displayed in the cab, on a large scoreboard display or even on a remote Android smartphone."
Other manufacturers offer similar devices. "SI Onboard offers a hand-held remote display for the loading operator to monitor the weight distribution in the vehicle being loaded," says Riley.
Vulcan On-Board Scales also offers a monitor for the loader operator. "The person running the loader can monitor the amount of material being loaded through a wireless hand-held device, which displays the same weight data as the display in the truck," says Elefson.
Increased Accuracy Pays
Do some research and understand what is available before purchase. "Some units only provide load weight, while others offer per axle weight," says Panagapko. "Our wireless Smart Scale gives the operator per axle weights."
After Adventure Trucking sets up critical truck parameters in its LoadMan systems, it can track all critical load information. "It tells you what the steer axle weighs," says Chandler. It tells you what the drive axles weigh. "It tells you what your gross weight is. It tells you what your trailer weighs. It tells you everything that you want to know. I think we are within 1% to 2% accuracy."
Don't forget to leave a safety margin to prevent overloading. "A safety margin should be factored in to ensure that the maximum legal payload is not exceeded," says Panagapko. "Scales range in accuracy from 0.3% up to 3% depending on the loading environment."
Elefson adds, "A load cell-based on-board scale system measures typically within 1% of GVW, and often better than that. The more accurate the system, the less weight you have to allow for a safety margin. The safety margin depends on what leeway is allowed in a particular application. However, always aiming at 1% under is a safe loading target to stay legal.
"Systems that measure suspension deflection or do not measure all load paths create a wider accuracy bandwidth, and therefore the safe load target is lower," Elefson explains. "That is why a system that uses the most accurate and repeatable technology provides the most reliable payback."
"Typically, the LoadMan system can provide less than 1% error," notes Housley. "The same accuracy is also provided on individual axle group weights. "
Systems Prove Reliable
Adventure Trucking reports that its LoadMan Systems have proven reliable. "We really don't have a lot of problems with anything," says Chandler. The company might replace a couple of load sensors a year. "Our biggest problem is drivers that start pushing too many buttons."
"Typically maintenance is very low, with calibration recommended annually," says Housley.
"Maintaining an onboard system will vary between applications, but typically consists of ensuring that the load cells/transducers do not become bound up with debris and that the components remain tight," says Riley. "All SI Onboard systems are completely self diagnostic with regard to component monitoring. Periodic calibration is usually not necessary. The frequency of re-calibration is a factor of the application, as well."
Many systems will not need recalibration once properly installed. "With our systems, there is a one-time calibration," says Panagapko. "The initial calibration does not have to change unless something in the suspension system is changed. Our scales also maintain accuracy through temperature extremes."
"Maintaining a load cell-based on-board scale system is not much different than normal dump truck maintenance," says Elefson. "The hinge points should be greased like they are during normal dump truck maintenance. Also, the wiring should be protected so that it is not snagged or cut during normal operation."
A load cell based system often does not require re-calibration unless the truck configuration itself changes. A secondary suspension deflection-type system requires more maintenance and calibration as the components and technology are more susceptible to the rigors of operation.