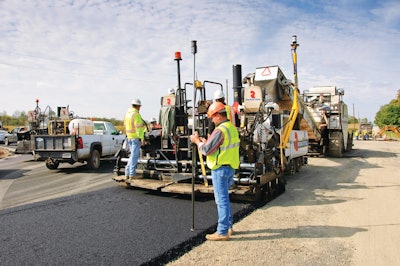
Being prepared directly applies to asphalt paving contractors, especially those intending to get maximum benefit from 3D paving and milling technology.
"Half the job of paving with 3D technology is done with proper preparation," says Jeroen Snoeck, paving segment manager for Trimble. "If the subsurface below the paver matches the design, the 3D paving operation is able to minimize asphalt usage and achieve the best smoothness.
"You need to get the site design right before setting up the 3D infrastructure and control points," he continues. "The machine will pave within millimeters of the design. Therefore, you don't want mistakes in the design which would be shown in the results."
Tight tolerances, time frames
Yates Construction Company of Stokesdale, N.C., completed a massive project with a stringent requirement of maintaining a 1% cross slope for surface drainage in the final laydown of the asphalt. Typical highway paving projects require a more forgiving 2% slope from centerline to shoulder.
The project was to construct the new Jacksonville Port Authority's Port TraPak Container Terminal at Dames Point in Jacksonville, Florida. Yates placed 254,000 tons of hot asphalt over a 125-acre container/trucking terminal in 9 1/2 months.
To accomplish the required surface tolerances within this tight time window, Yates equipped its Roadtec RP 185-10R paver with a Trimble PCS400 Paving Control System. This enabled asphalt to be placed on a sub-grade with a final grade within +/- 1/100th to slope specifications. International Underground Corp. of Jacksonville, Fla., completed earthwork using a motor grader equipped with a Trimble GCS900 Grade Control System with GPS and laser augmentation.
"It's extremely hard to hold that tight of tolerance accuracy on a paving project," states Paul Sowa, project engineer with Yates Construction. "Most contractors won't warranty a project that's under 2%. And on this project, we had some areas (around the drainage grates) where we had to maintain a .58% and .63% slope. But by using the GPS with the laser augmentation system on the grader and the paving control system during paving, we were able to deliver those tight specifications."
Stakeless process saves time and money
In Virginia, E.V. Williams of Norfolk was the principal contractor for the I-64 / Battlefield Boulevard Project in Chesapeake, a complex interchange rehab that included widening a heavily traveled two-mile stretch of interstate from six to 10 lanes and widening a cross-over bridge from one to three lanes in each direction. It also included adding five newly constructed bridges and new braided exit and on ramps.
"Our use of GPS grade control technology was major," says Kyle Myers, GPS manager, E.V. Williams. "It's unbelievable how much time and money it saves you when you go from at least a four-man crew, an operator and two workers pulling the string and one checking grade, to one guy on a machine, no stakes... Plus, the GPS system allowed us to work at all hours if needed. We were able to construct one area of our project, the eastbound extension, completely at night, using only a GPS grader. You couldn't have shot grades in the dark.
"It just made life extremely easy," he continues. "Here's another example: We had one of the on-ramp loops completed from virgin ground all the way to the point of blue-top stakes. There was one dozer operator."
After paving was completed, the Virginia DOT commented, "The readability is unmatched. When you come down the highway and hit that new section, it's completely silent in your vehicle; there are hardly any bumps. The sub-base is dead on."
Smooth results
The Ohio State University Airport in Athens, Ohio, is ranked one of the top five busiest airports in Ohio. The airfield's traffic comes from corporate and private traffic, as well as the University's own Department of Aviation.
Shelly and Sands, a Columbus-based highway and heavy construction contractor, completed the rehab of one of the four runways. Considering the amount of air traffic, the university needed the project completed quickly, while also satisfying the strict FAA quality requirements for grade and slope, accuracy and smoothness.
"We first had to mill the existing asphalt to a variable depth of zero to 5 inches in multiple passes on the 6,000-foot runway," states John Dowalter, survey manager for Shelly and Sands. A subcontractor for Shelly and Sands milled the old surface to a new design using the Trimble GCS900 3D system guided by a SPS930 robotic total station.
According to Dowalter, variable-depth milling is one of the biggest benefits he sees for 3D. "After milling off the surface, we went in and pulverized the remaining asphalt and sub-base to a 14-inch depth, then re-compacted and re-graded it," he says. "Then we cement-stabilized the pulverized material to the 14-inch depth and re-graded to sub-grade."
Between each of these processes, there was profile grading to match the specs of the provided plan. The runway and ramp areas both had variable cross-slopes. "The complex grading that was required was made simple with the help of [3D] technology on both of our motor graders," states Dowalter. "Both machines are equipped with Trimble GCS900 Grade Control Systems, allowing us to match the grading to the profile plan without errors or rework."
He adds, "Even though stringlines were spec'd into the project, we eliminated the need for literally miles of stringline and easily saved a week's worth of staking. The engineering firm that developed the specs was, I guess, more old school. They struggled at first to understand the technology and its benefits. Initially, they were trying to dictate how we were to re-build the runway, but we stuck to our guns as far as using the Trimble 3D systems and proved we could achieve the grade tolerances they required."
Understandably, the FAA is very strict in its requirements for the paved surfaces of airport runways. "We needed to hit the spec +/- 1/2 inch," states Dowalter. "On top of that, we were building a completely new profile grade for the runway that the engineers had created, which meant variable-depth milling. To meet this more complex profile, we couldn't just set up the milling machine to mill 4 inches and let it head down the runway. We might be milling a 1/2 inch at one point, get 500 feet down the runway and be milling 3 inches."
The Ohio State University Airport south runway rehab was completed in two phases and the ramp rehab project was completed in five production phases. The runway was paved in four 25-foot-wide passes. The University, FAA, and Shelly and Sands were pleased with the precise sub-grade, which allowed for the smooth paving required for the airstrip.