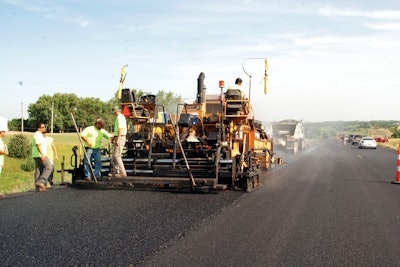
South Dakota’s Department of Transportation has designed a flexible, high rock-content asphalt mix called Class S that’s well suited to the state’s heat and cold extremes. Class S eliminates rutting, extends surface life and provides skid resistance in winter driving conditions. The mix design includes a large volume of rock, and high polymer binder to bond the rock together. SDDOT Asphalt Mix Design Engineer Jim Costello says his department first used Class S about 25 years ago in the western part of South Dakota.
“Because of the high rock content of Class S, oil tends to drain right through the mix unless something is used to stop that drain down. In western South Dakota, we used limestone, which is plentiful in that part of the state,” Costello notes. “We began using Class S there in the late 1980s and early 90s. Rock in the mix is sized between ¾-inch and ¼-inch. The basis for the mix came out of Germany in the 1980s. They called it SMA, Stone Matrix Asphalt, which basically uses stone-on-stone content, which means the aggregate itself carries the traffic load.”
Because Class S was performing so well on high traffic areas in western South Dakota, SDDOT began considering how they could use it on high traffic roadways in the east where limestone wasn’t readily available. Eastern South Dakota quarries hold quartzite and granite, both high quality aggregates suitable for Class S. However, both quartzite and granite would require high binder contents and result in high drain down of the binder. In order to use quartzite and granite in the mix, SDDOT determined something was needed to prevent drain down from occurring.
“The resource we identified that was economic and effective is cellulose fiber,” Costello explains. “It’s like insulation you’d blow into your home. It’s recycled paper, grey in color. The fiber is blown into the drum while the mix heats. It’s been used in asphalt mix outside South Dakota for a number of years.”
The company who supplied cellulose fiber for the Highway 81 project was Hi-Tech Asphalt Solutions, based in Virginia. The cellulose fiber their company produces is made of recycled newspaper that’s ground and mixed with lime and other additives. Once ingredients are combined, the fiber is dried, baled and shipped to consumers.
Highway 81 project
SDDOT’s most recent project using Class S in eastern South Dakota was an overlay of 10 miles of US Highway 81 north of Yankton. The project, NH 0081(84)6, PCN 01BX Yankton County, began in June 2011 and was completed September 30, 2011. The project objective was to resurface the section of the roadway that was rutted, had faulted joints and areas of oxidation.
“Highway 81 was established in 1954 with a 4.5-inch gravel base and 8-inch concrete mesh PCC pavement,” Kevin Heiman, PE, Yankton Area DOT says. “In 1980, SDDOT completed a 1/2-inch Class D overlay in this same area, and in 1995, two lifts of recycled hot asphalt pavement were put down. The first lift was 2.5 inches; second was 1.5 inches. In 1996 the roadway was crack sealed. In 1997 a 3/8-inch asphalt treatment was laid. In 2003 a 3/8-inch asphalt surface treatment was applied.”
In preparing the roadway for the Class S overlay, 1.5-inches of the existing surface was cold milled. A total of 15,075 tons of Q3R in a 1.5-inch mat were laid under 8,075 tons of Class S 1.25-inch mat.
Commercial Asphalt, based in Mitchell, SD, used a Caterpillar AP1055 to lay both mats in the project. Two of their four rollers are Caterpillar CB64s, one is a Caterpillar CB634C and one a Caterpillar PS360C. Their haul trucks are all Freightliners pulling belly dumps. The asphalt plant they used is an Astec double barrel 400-tph system.
Neil Waldera, commercial asphalt division manager, says use of Class S was a new experience for their business, which is owned by Spencer Quarries Inc.
“For the most part the project went pretty well,” Waldera notes. “There were a few things we had to get used to. The only modification we made to our plant was installing a vent in our drum to blow the cellulose fiber into it. The blower was leased from Hi-Tech Asphalt Solutions. The fiber is pretty much engulfed by the oil when it enters the drum. We used flyash as an added filler to meet SDDOT Class S gradation. The flyash slowed our production because of the high volume of dust it brings to the baghouse. We ran at about 60 percent of our normal hourly output.”
Hi-Tech’s fiber machine was fully compatible with the Commercial Asphalt plant computer and operated as part of the plant. The blower device operates on a gravimetric principle, dispensing fiber based on weight depletion from a known weight. The machine breaks down and fluffs the baled fiber in six distinct phases.
Fiber requires hotter temperature
Drum temperature for producing Class S ran between 325 and 350 degrees, slightly hotter than the typical 300 degrees of a standard asphalt mix. Waldera explains that Class S has to be hotter in order to keep the mix pliable between the time it leaves the plant and gets to the paver.
“This mix really hardens once it cools,” Waldera says. “There’s a narrower window for getting it transported while it’s hot enough. If it cools too much before it’s compacted, it’s almost unworkable.”
Because Class S hardens so quickly, SDDOT enforces a seasonal limit on producing the mix, stipulating it can only be used between June 1 and September 15. Ambient temperatures must be at least 60 degrees farenheit before the mix can be used.
“If it’s hauled too far, that becomes an issue too,” Costello points out. “Even when it’s hot, Class S is really sticky, what I call nasty. The nastier the mix is, the better quality the end product is. But it isn’t easy to do handwork with it. Think of it like a Rice Krispie bar, that’s the kind of texture you have. It’s pliable when it’s hot, but once it cools it’s very unforgiving.”
Cost is weighed against benefits
Before his company secured the Highway 81 project, they had some knowledge of Class S and what they would be required to do in order to produce the mix. They used Internet research as well as SDDOT expertise to learn more about Class S and what to expect during the project.
“We’ll probably see more Class S on some of South Dakota’s high traffic areas,” Waldera says. “The biggest adjustment for us was productivity. Our baghouse was the limiting factor. But we won’t hesitate to pursue another project that utilizes Class S.”
High polymer oils, such as those used in Class S, are becoming more common in asphalt mixes. Jebro, Inc. in Sioux City, IA, provided the high polymer oil blended into the Class S mix.
“The oil’s rubber-band-like qualities have proven to extend the life of all types of asphalt surfaces,” Noel Schulz, Jebro Marketing Manager, says. “Polymer oil is very common in asphalt mixes used on roads. We’re seeing more city, county and state government agencies using polymer modified liquid asphalt binders.”
An added benefit of Class S is the residual effect of liquid deicing products when it's applied to Class S roadways.
“Pores in the Class S hold the chemical. It doesn’t run off like it would on a standard asphalt surface,” Costello tells. “There’s also no need to chip seal Class S surfaces. The open nature of Class S is something we want to retain.”
While South Dakota’s DOT enjoys numerous benefits of Class S, Costello says the cost of producing and applying the mix is carefully considered in every state road project.
“It’s our premium mix,” Costello says. “We started using Class S in the eastern part of the state in 2004. We learned a lot on that first project, what worked and what didn’t. We tried to tailor the mix design to obtain the best possible effective and economic product. We’re fortunate to have high quality aggregate in both the eastern and western part of South Dakota. We don’t have to do anything special to make Class S work. With our freeze/thaw cycles, which affect the entire state, cracking road surfaces is probably our biggest challenge. We’re using Class S as a wearing course on interstate and high traffic roadways. We haven’t used a mat thicker than 1.25 inches and we haven’t used the mix long enough to draw conclusions about its overall longevity.
“Based on how Class S has performed so far, we’re likely to use it on more high traffic areas off the interstate,” Costello adds. “We’ve done a good job in designing our dense graded asphalt mix used on the majority of our road projects. Since 1998 we’ve had a QC/QA program for most of our asphalt mixes. We’ve overcome some issues we had prior to that. We’re always striving to balance the effect of 100-degree to minus-20 degree temperature swings. That’s just part of our South Dakota climate.”