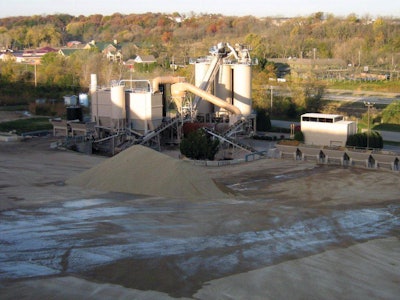
Payne & Dolan Inc., a professional asphalt production and construction services company, has served the needs of its customers for over 80 years. Headquartered in Waukesha, WI, the company is located throughout Northern Illinois, Wisconsin and into upper and lower Michigan. The company serves state, county and municipalities as well as private/commercial customers.
"We do everything from large highway projects to paving driveways," says John Bartoszek, a regional manager with Payne & Dolan.
Payne & Dolan is one of the largest producers of both hot and warm mix in the Midwest, and much of this includes recycled asphalt materials, including reclaimed asphalt pavement (RAP) and recycled asphalt shingles (RAS), which means they know a thing or two about how to best optimize an asphalt production facility.
"Sustainability and recycling is really important to us as a company as well as our industry," says Bartoszek. "As asphalt contractors, we're very dependent on the oil industry to supply our product. As energy prices continue rising, we need to optimize our production facilities to get the most fuel efficiency out of them. And as asphalt material prices go up, using recycled asphalt materials like RAP and RAS will become essential as a standard in our mixes."
The more efficient your asphalt plant, the more money goes to the bottom line. Here are a few tips from Bartoszek on how best optimize your asphalt production facility.
(subhead) Moisture control
As all asphalt producers know, to make a good quality mix, your aggregates must be dry. Because recycled materials like RAP and RAS have those additional oils in them, they're added to the mixing zone later in the drying process to save the oil from being overheated and burned off. Therefore, you must control the moisture in these materials before they enter the mixing zone because they typically get less drying opportunity in comparison with the virgin material.
The very nature of recycled asphalt materials can also tend to make them more susceptible to moisture. "For example, cellulose fibers in RAS can absorb water, and it will have a higher moisture content than virgin aggregates," says Bartoszek. "There are a couple of things you can do, however, to help control the moisture of your aggregates."
- Cover your RAP and RAS to reduce the amount of moisture in them as much as possible. "This is a crucial step, especially in climates like we operate in," says Bartoszek. Payne & Dolan uses storage structures, protecting its RAP and RAS from the elements.
- Remix the recycled material piles. "RAS can have a tendency to get a crust on it which can prevent further drying," says Bartoszek. Turning over – or "fluffing up" - the piles will aid in drying the material on site.
- Create paved, sloped stock pile areas. "Sloped drainage areas are very important," he says. "If they're not sloped, water may actually sit in the materials. In this situation, gravity is our friend, pulling moisture away from those piles."
"There is a direct correlation with moisture control and fuel efficiency," says Bartoszek. "The drier the material is going in, the less fuel you will use drying it, which translates into cost savings."
(subhead) Tracking temperature
Fuel efficiency can be controlled by keeping moisture in check, and it can also be controlled by continuously checking your burner as you produce mixes with recycled materials, says Bartoszek. "One way to optimize your asphalt plant is to make sure your materials are hot enough to achieve complete blending of the RAP and RAS but not too hot that you're wasting energy," he says.
Maximizing your burner flame can help keep your burner in check. "There are certain rules of thumb, such as how wide your flame is, that you learn over time and that vary with each plant," says Bartoszek. "And each mix you produce will need more or less heat – one size does not fit all when it comes to that."
For example, a coarse mix with a lower percentage of sands and fines will require less heat because it will have less moisture in comparison to a finer mix, which is dense employing higher amounts of sands and fines, therefore more moisture. "When you combine the mix type and increased recycled materials, which innately have higher amounts of moisture, you'll have to adjust your burner accordingly," says Bartoszek.
Once the burner is set, double-check the temperature of what your mixing is very close to what is getting loaded out. "The quickest correlation anyone can use to ensure that you don't have moisture in the mix is to check the temperature of the product you're shipping out," says Bartoszek.
For example, if you have a mix that is produced at 330 degrees, ensure the moisture is out of the mix and optimize the flame so you're not producing at 340 degrees. When the material is loaded in the truck, make sure there hasn't been a 15- to 20-degree drop. "If there's a large temperature drop between production and load out, you probably have moisture in your mix, your plant is not running efficiently or the materials are too wet," says Bartoszek. "You might have to slow the plant down. If it's running too fast or not hot enough, you'll have moisture in the mix and you'll see the change in the temperature."
Communication between plant operators and paving crews is another way to keep an eye on your mix temperature. "There are intangibles that happen out in the field, and there's no gauge we can put out there that says this material is dropping too fast," says Bartoszek. "That kind of temperature drop would mean there is a severe problem, but points out that paving crews and plant operators have to communicate effectively. Are the temperatures correct once the material arrives in the field? Constant communication is as critical to optimizing your plant as the components you're installing to ensure accuracy."
(subhead) Critical components
There are a few components and technologies that Bartoszek says are "must haves" when it comes to running an efficient asphalt plant.
RAP crushers. "Correct flow is crucial to an efficient production process," he says. "A lot of suppliers offer a RAP crusher or nugget cruncher that handles the oversize pieces that sometimes come from recycled materials."
RAP crushers crunch the material so there are no oversize pieces restricting or stopping material flow to the drum. Installing this type of component is a great process control technique, says Bartoszek.
"RAP crushers really ensure oversized or large pieces of conglomerate are not entering into the plant," he says. "If these pieces end up in the mix, it can really affect paving quality. Oversize chunks in RAP will create a bump in the mat, and smooth pavements are extremely important to paving contractors."
Bins are another component to pay close attention to. Multiple RAP bins help with versatility, and RAS bins should have steeper slopes and wider throats to ensure the material flows and isn't clumping during the feed production process.
Reverse weigh bridges. An asphalt plant can install load cells or a weigh bridge directly on the belt to make sure the weight is accurate. This also helps you receive real-time feedback that you have the correct amount of materials going into the process. "With recycled materials, you have a tighter tolerance than you would have with virgin aggregates, so the weigh bridge helps with accuracy," says Bartoszek.
Longer drums. Counter-flow drums with extended mixing zones is something the industry is moving toward, says Bartoszek, because of the increased amount of recycled products now being used. "For producers using high amounts of RAP and RAS, we're already seeing and using this trend at our plants," he says.
"We don't want to waste fuel by superheating aggregates," he explains. "Right now, we superheat the aggregate to aid in the drying of the RAP and RAS, but superheating those aggregates is wasting a certain amount of energy. By lengthening the drum, you don't have to superheat the aggregate as much because the materials have a longer drying time."
A longer drum can also give the plant better capacity. "When using high amounts of RAP and RAS, the plant usually – because of higher moisture in those products – reaches maximum production limits at much lower tonnage per hour. Aggregate product properties directly reflect plant production," Bartoszek says. "It takes a certain amount of energy to dry those products. Lengthening the drum increases drying efficiency."