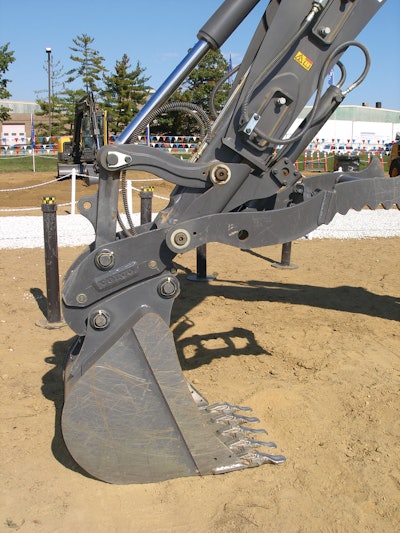
Customers always demand more performance out of their backhoe loader. “In North America, the backhoe end of the machine is used about 70% of the time the machine is operating, so it’s always been an area of focus for our product teams,” says Kevin Hershberger, BHL marketing, Caterpillar.
A few criteria define performance, including how much trench can you dig without repositioning the machine, and if you can see past the boom when it is in the trench as well as when it is swinging up and over a truck side. “The biggest complaint from the field is the size of the boom as operators have to look past them into the trench or over them when loading a truck,” says Jim Blower, JCB. The JCB boom is narrow in width and depth to address this issue.
“Consider performance specs such as digging depth, forward reach and lift height for truck loading, lift capacity and breakout forces,” says George MacIntyre, Global Product Marketing manager, Case Construction Equipment. “Other important characteristics include machine stability while roading, boom height for transport/working in confined spaces, overall machine dimensions and visibility.”
Then there is the issue of strength versus weight. “The boom has to be able to withstand all of the digging and lifting forces while being as light as possible to get the best performance,” says Blower.
A box-style design boom design can combine both rigidity and light weight. Consider the boom on the Volvo backhoes. “The boom is basically a box section with a forging on the bottom and the same forging on the top. It is enclosed,” explains Marcello Bargellini, backhoe product specialist, Volvo Construction Equipment.
“Strength is a very important attribute when designing the boom,” says Jamie Wright, product manager, Terex Construction Americas. “Terex uses 8mm thick steel tubular design with their booms, which adds considerable strength and durability to the product. Forged steel at each pivot point reduces wear on pins and bushings.”
Keeping hydraulic lines safe is a priority on any good backhoe design. For instance many manufacturers, including Volvo, route hydraulic lines inside the boom, where they are protected and pay special attention to areas where plumbing has to be exposed.“To the extent possible, we try to use tubes (vs. hoses) for longer life,” says Bargellini.
“Neat routing of hydraulic hoses increases visibility and reduces damage to hoses,” says Wright. “Visibility to both the loader and backhoe is important for overall efficient operation. A well-dimensioned boom and boom placement gives the operator an excellent view into the trench at any position.”
The over center boom
“One of the mainstays of the Case backhoe design is the over center boom,” says George MacIntyre, Global Product Marketing manager, Case Construction Equipment. “The over center design means that the boom ‘over centers’ from vertical and tilts forward (the boom cylinder is pinned rearward more than non-over-center designs.”
For the N-Series, Case maintained this design. “Advantages of the over center design include better balance and ride, lower transport height, steeper downward digging angles and uniform lift performance throughout the boom lifting heights,” says MacIntyre. “For an operator this means that the boom can lift, lower and reposition an object near the hydraulic capacity of the boom without degradation at deep depths. All backhoes on the market lift more at full boom raise but drop off when they are below grade. The Case over center design allows a very flat curve, meaning the design allows a backhoe to lift almost as much below grade as at full raise.” This is important when you are excavating below grade or setting pipe in the ground.
When Case introduced its latest N-Series backhoe, it unveiled Power Lift technology, which channels hydraulic power directly to the boom with the touch of a button. The company claims this feature can provide lift capabilities comparable to an eight-ton excavator. To handle this increased capability, Case redesigned its boom, resulting in the S boom. The traditionally all-cast backhoe boom has been replaced with a fabricated boom. Oversized panels are consistently assembled via robotic welds add strength to withstand Power Lift forces. The swing tower, bucket links and internal portion of the extendible dipper stick continue to be cast components.
“During the design of the N Series backhoe, engineering put great emphasis on making sure that any modifications to the boom design to improve performance would not interfere with the operator’s line of sight to the backhoe’s work area,” says MacIntyre. “Case engineering mapped the line-of-site visibility with new boom design concepts to better understand the impact to visibility with any potential changes to the boom design.”
The fabricated boom allows for internal hose routings for improved protection. “Some customers complain that the auxiliary hoses on the boom/dipper get snagged on branches or other obstructions when operating in woods or confined spaces,” says MacIntyre. “The N Series boom design helps to address these customer concerns. First, the hydraulic hoses are routed inside the boom for greater protection. Also, Case rerouted hoses and changed the bracket design where the hoses intersect between the boom and dipper to provide less chance of contact with low overhangs. This modification also provides the additional benefit of lower transport height.”
Check for attachment versatility
Backhoes can utilize a number of attachments, so hydraulic versatility can be an important consideration. “If you want to install any attachment, the Volvo machine is equipped with a single- and double-acting circuit,” says Bargellini. “So you can actually convert from single- to double-acting on the same machine. You can also adjust the flow for those circuits.”
Caterpillar offers similar hydraulic system versatility. “Caterpillar offers a combination function hydraulic line kit which allows use of one-way and two-way flow attachments from the same auxiliary lines,” says Hershberger.
“Machine performance is driven by many variables including hydraulic systems, pressures, flows, cylinder sizes and pin locations,” says Hershberger. “The shape of the boom factors into performance areas like visibility, truck loading performance and digging over foundation walls and other obstacles. All of these factors, and others such as hydraulic valve tuning combine to deliver backhoe performance.”
Geometery and hydraulic capabilities can differentiate one machine from another. Consider the revamped slew system on the Terex backhoes. “The TLB 840 is also designed with a new slew system that provides high torque for easy backfilling and slewing up hill,” says Wright.
Boom shape and geometry considerations
Some manufacturers of backhoe loaders have introduced curved boom designs. “This design aids in machine balance, especially when the machine is being driven at speed,” says Blower. “The curved boom aids in throwing the backhoe weight over the tractor and not having it hang out the back of the machine.”
“JCB has elected to stay with the straight boom open box design as cylinders, hoses, valves, etc. can be located inside the box, thus protected from site damage,” says Blower. “The balance of the tractor for roading purposes is achieved by moving other items within the tractor – engine, transmission, etc. – to get the optimum balance.”
“The shape of the boom has no reflection to the machine’s performance in terms of digging or lifting,” says Blower. “The geometery of the boom and dipper working together along with the hydraulic cylinders and pressure provides the power and productivity with in the backhoe, not the shape of the boom,” notes Blower.
“Geometry is important when talking about the overall performance of the backhoe,” says Wright. For instance, Terex uses a curved boom design, which combined with the large cylinders, increase digging performance. “The curved boom design also offers operators greater clearance to reach over obstacles and the ability to load closer into trucks for greater productivity.”
Many excavators, such as the Caterpillar E-Series feature an excavator-style boom. “Caterpillar launched the excavator style curved boom on our 446 in 1989, then carried it over to our B Series machines – 416, 426 and 436 in 1992,” says Hershberger. “At that time, and for years following, most competitors maintained a straight boom design. Today, many have added some curvature to their boom design, Since then, we’re added E-Sticks and improved versatility through hydraulics and available work tools.”
The curved design provides additional clearance over obstacles while digging a trench or truck loading. The narrow boom enhances the viewing area to the bucket and trench throughout the entire operating range. Caterpillar’s excavator-style boom features box section fabrication with thick wear plates for performance and durability.”
The Volvo backhoe boom design also employs an arched shape that is narrow and tall. Arch designs, which are inherently strong, have been traditionally used in bridge and building construction. The upper and power end caps on the boom are designed to carry the high stress loads from the pivot pins and distribute them smoothly and evenly through the boom structure.
Another key criteria determined by the design geometry is bucket rotation. “Bucket rotation is very important if you want to scrape or dig,” notes Bargellini. “Our bucket rotates 205 degrees, which is about the maximum industry standard.”
Similarly, a single-pin bucket linkage on the Caterpillar E Series allows 205 degrees of bucket rotation, while serrated edges on the stick provide improved material clamping for clearing and demolition applications.
Another component critical to performance is the backhoe swing casting. The casting on the Caterpillar E-Series features replaceable bushings for durability and service.
Volvo concentrated a lot of effort on the design of the swing pivot. “We are unique in the industry in that we place our swing cylinders on top,” says Bargellini. “So we get them away from the dirt and perhaps we get better seal life and cylinder life. We also have a yoke on the top and a yoke on the bottom. We have huge bushings, which means that we expect longer life from this swing casting.”
Even the design of the boom lock can differentiate the backhoes. “Our boom lock is spring applied and pressure released,” says Bargellini. “It is really easy to actuate.”
“Safety is always the first concern with Terex,” says Wright. “Our boom and swing locking system is unique to the industry by offering swing and boom lock with a touch of a button, and all from within the cab.