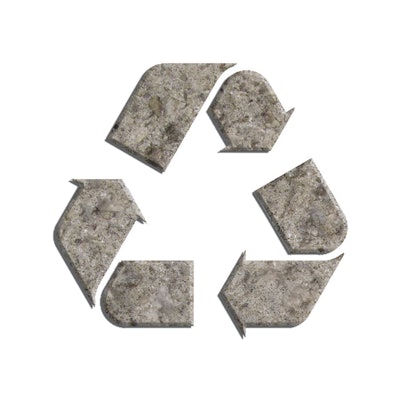
Producing concrete with a very low carbon footprint has become one of the major goals of the "green" movement. That requires minimizing the amount of portland cement used per cubic yard and using larger than normal amounts of supplementary cementitious materials including slag, fly ash and silica fume.
Some high profile structures have been successfully built using only a few hundred pounds of portland cement per cubic yard. But the success of some lean mixtures has also lead to one of the most prevalent misunderstandings: The belief that because some concrete producers can supply very lean concrete with acceptable properties in both the plastic and hardened states, all concrete producers can do it.
This is a fallacy. Concrete producer demographics affect the availability of supplementary cementitious materials, with high quality slag or fly ash not being economically available to all producers. The environment in which the concrete will be placed is another factor affecting performance.
Issues with high SCM mixes
In cool or cold weather regions, the combination of low cement contents and low temperatures increases setting times, which can delay finishing and increase finishing costs. Delays in early strength gain for these lean mixtures also have a highly critical effect on schedule, especially for precast/prestressed and post-tensioned structural members. Maximum use of the precasting beds requires stressing when the concrete is only a few hours old, and post-tensioning is often done when the concrete is two or three days old. Low-carbon-footprint concretes often need longer curing times to reach the strengths needed for stressing the tendons. Longer required curing and protection times also affect schedule.
The member type -- foundation, wall, column, slab -- affects the needed setting time and early strength gain as well. Slabs are the most vulnerable to problems associated with slow setting and strength gain. They must be left unprotected until the concrete is firm enough to be walked on, the result being greater exposure time to rain and cold weather effects.
A further effect is related to the manner in which the slow strength gain must be overcome. Some mixtures use very low water-to-cementitious materials ratios in order to overcome the slow strength gain. Making such concrete workable requires the use of high-range water-reducing admixtures and very low water contents. This has caused finishing difficulties due to a lack of bleedwater at the surface. Producing acceptable concrete with a low carbon footprint requires the right combination of several important variables.
Today's research
The authors of "Challenging the System" are now engaged in developing a Users' Guide to "Green" Concrete in Building Construction (Hereafter referred to as the Guide). This effort is supported by grants from the Charles Pankow Foundation, the American Concrete Institute's Concrete Research Council and the American Society of Concrete Contractors' Education, Research & Development Foundation.
The Guide will consist almost entirely of text presented, where possible, using a terse, bullet-point format that will make it an easy and compact read, while covering the essential points that members of the construction team need to be aware of. Such a guide will help owners, architects, engineers, contractors and other stakeholders in the concrete building sector to (a) understand the differences in properties between "green" concrete and traditional concrete mixtures for building construction and (b) apply the best practices for the use of "green" concrete in building design and construction.
We have already surveyed members of the American Concrete Institute, National Ready Mixed Concrete Association and American Society of Concrete Contractors for input on their experiences -- both good and bad -- with "green" concrete. Also, "green" concrete mixtures will be tested and the data presented in the Guide to provide information that is usually proprietary and not available to the industry or to the public. This data will supplement, support and be used to illustrate the construction challenges of "green" concrete. Companies contributing to this phase of the work and as an advisory team include U.S. Concrete (concrete producer), Tipping + Mar (structural engineer), Webcor Builders (contractor) and BASF (admixture manufacturer).
Look for updates as we follow this project through to completion.
Ward R. Malisch, technical director for the American Society of Concrete Contractors, can be reached at [email protected]. Bruce A. Suprenant, P.E., president of Concrete Engineering Services, can be reached at [email protected].This column is sponsored by the American Society of Concrete Contractors, but the views expressed are solely those of the authors.