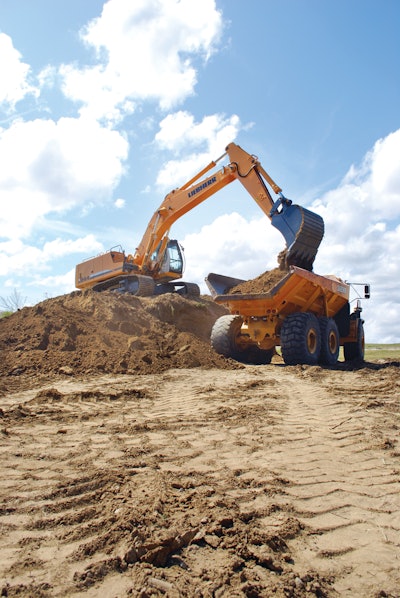
Improper operation of an excavator while trenching, sloping or benching can have a big impact on productivity and can potentially place both people and equipment at risk. Oftentimes, it's the result of poor or inadequate training. In other cases, it stems from bad habits, misconceptions about how a particular process should be completed or lack of planning.
"The most common mistakes that I see made by operators are a failure to plan the approach to the excavation," says Matthew Hendry, product consultant, hydraulic excavators, John Deere Construction & Forestry. "Beginning work without a complete plan, they unwittingly create 'bottlenecks' — for example, intersecting trenches or an access ramp in the way. Bottlenecks often require moving material several more times than necessary, significantly increasing job costs.
"Properly planning the dig will help to minimize those chances," he continues. "Plan where you will put the spoil pile... where you will stage your pipe and bedding material. Plan where you will cross existing utilities and if you may need additional shoring around those locations."
"Visualize what [the project] is going to look like when it's finished and how it's going to progress before you do," advises Chris Cannon, an on-site trainer for VISTA Training. "A lot of times, operators can get boxed in. They may put the spoil in a certain [area] and realize later that it's a tight site and they can't get out. They will have to climb over the pile, or they've created an obstruction for themselves."
"Prior planning will prevent poor permance, minimize the chances of accidents and maximize your chance for productivity," Hendry asserts.
Start with the right tools
As with most equipment applications, productivity and efficiency depend on selecting the right tools for the job.
"The first mistake — even before operating the machine — would be to work with a tool/attachment that is sized incorrectly based on machine reach, configuration and the material to be moved," says Jeff Powell, general product manager - earthmoving equipment, Liebherr Construction Equipment Co. "The incorrect attachment may be too heavy and would influence the machine's stability and performance."
Selection of an excavator and attachment should be based on the production needs of the project. For example, Hendry cites, "Trenching 18 ft. deep and pulling two trench boxes will dictate a 35- to 45-ton machine configured with the right length arm to reach your depth, but also with the lifting capacity to handle lifting the boxes."
Powell agrees, noting, "An application that requires a maximum reach of 40 ft. should not be done with a machine that can only reach 30 ft. Otherwise, you are trying to compensate for the missing 10 ft. with some 'dangerous' ideas — stick extensions, working on uneven slopes and even in loose materials, etc.
"Ensure that the right attachment for the machine is chosen, adapted to the material density, reach and machine configuration," he emphasizes. "The machine itself has to be adapted to these long-reach applications [with] additional counterweight, wider undercarriage."
Using excavators specifically designed for longer reach applications does require some additional precautions, however. "Super Long Front excavators (SLF) require very detailed project planning," Hendry states. "[They are very different machines as far as operating characteristics go.
"The long boom and arm configuration changes the balance and center of gravity significantly," he explains. "Just walking an SLF through the project requires planning. Unlike a regular excavator that can use the boom and arm to lift and maneuver the excavator, the SLF can't use the boom and arm in this manner."
As a result, advance planning and proper site setup are doubly important with these machines.
Ensure a stable base
Providing a stable platform for the excavator is an essential element of site setup. "The machine has to be on even ground and the ground has to be stable," says Powell. "If the machine is already standing on a slight slope, this will affect all of the machine's movements and its stability."
"A rocking excavator is not a productive excavator," Hendry comments. "As the excavator rocks forward on its idlers, it is putting added ground pressure on the banks of the trench. This can contribute to cave-ins. OSHA requires operators to be sure the excavator is at least 2 ft. back of the end of the trench."
The weight of an excavator extends out an angle in more of a pyramid shape, rather than straight under the tracks. "If you have an excavator that's sitting right next to the edge of the trench, that weight distribution goes out at an angle, so you're really resting on a couple of inches of support," Cannon states. "As you're digging, you're creating vibration and the machine itself is vibrating, so you create instability, especially if the material has been worked before."
As such, it's critical to maintain a safe distance from the edge based on soil type. "If it's not rock, you're safe always assuming that it's Type C soil," Cannon says. "That requires that you be back the length of distance from the edge as you are height wise, so that you have a 1:1 to ratio of support."
Position the machine at a productive height for loading material. "The bench height should be about the height of the haul unit dump box sideboards," says Hendry. "Set up for the trucks to come down the left side of the excavator, which is best for loading angle and visibility."
Avoid digging from the bottom up. "This wastes time and fuel and can lead to under cutting the excavator," says Hendry.
"You want to start out with the top layer, which is a marking path," says Cannon. "Dig the teeth in just enough to mark the direction of the trench so it's in alignment. Then, you can start gradually going down layer by layer, taking more out as you go down. That does a couple of things. It keeps the trench from becoming too large, and it also makes your efficiency better. You don't have to go down to the bottom of the trench each time to pull material out."
Long reach excavators require added caution. "When using long-reach booms/sticks on excavators, the operator needs to be aware that it is easier to dig the material out from under the spot where the excavator is sitting without knowing," says Powell.
"The SLF operator has to be very skilled and patient," adds Hendry. "If your operator gets in a hurry or loses focus, he/she will damage the machine. Each move of the boom/arm and bucket has to be deliberate. If your operator swings the house before the bucket is clear of the excavation, damage to the boom/arm will result."
Don't slide on slopes
Working on slopes presents some specific challenges. "There are always risks when working on slopes," says Hendry. "Improper positioning and operation of the machine can lead to tipover."
It's important to take the right approach to the job. "The height and degree of the slope will dictate how you use the excavator," says Hendry. "If the slope is tall, you will need to crawl up to the top and pull your grade down to the toe. Cutting a bench across the face for the excavator to sit on and pulling the grade from the top of the slope down to the bench is another option. The operator can reach down below the bench and grade the slope up to the bench."
If the project requires working on the face of a hill, it's important to consult the equipment operator's manual to determine the safe operating ratios. "It's very important not to exceed that," Cannon stresses.
Position the tracks of the excavator straight up and down the hill. "You should never have your tracks going parallel to the slope, because if you start to slide, once the edge catches, it's going to tip the machine over," Cannon explains. "If the tracks are going up and down the slope, if something catches, you're just going to roll over it."
The excavator should also be equipped with tracks suited to the task. "You need to focus on traction," says Cannon. "Traction is created through intense and focused weight distribution, where you have higher pounds per square inch. That typically requires thinner tracks and less grouser contacting the ground. So ideally, you want track with single grousers."
If possible, cut a terrace or bench to act as a platform for the machine. "Once you create a bench, you want to have your sprockets, which are the heaviest part of the track, inside so they're next to the hill," says Cannon.
Cannon also recommends using the smallest machine practical. "Center of gravity is such a critical concept at all times," he notes. "You're going to be more stable with a smaller machine on a slope."
The optimal choice is a compact excavator. "A lot of small excavators have a dozer blade on the front. This is a great tool for a slope because you can lower the blade below you on the slope and it will help to stabilize the footing," says Cannon.
Some compact excavators also have frames that enable tracks to be adjusted to uneven footing. "The angle of the track can usually be adjusted up to 15°, so you can actually sit on the slope and have the top of the machine level," says Cannon. "That's a huge advantage."
Another essential element of slope work is operator experience and knowledge of the machine. "Use your most experienced operator and be sure you have the right type of excavator for working on slopes," Hendry advises. "Be sure the operator understands the excavator."
This will help to ensure smooth, controlled movement of the machine. "When you're slewing material, you want to always keep the bucket and the stick close to the machine and to the ground," says Cannon. "As you're bringing it around, you want to control your speed because momentum on a slope can be a dangerous thing."
The steeper the slope, the more care required. "If you're on a slope, as the machine rotates, that material is going downhill and you're using the swing motor to lower the material," Cannon explains. "In an extreme condition where you have maybe a 1:1 slope, that swing motor — which is the weakest part of the machine, is working double duty. It won't be able to handle a full bucket of material safely if you're moving it too quickly." In some cases, it may actually be more productive to move smaller bucket loads.
Many of today's excavators are equipped with operating modes specifically targeted to slower, more precise operations such as fine grading. "Most machines have automatic settings where you can adjust the speed of the engine and still have full hydraulic pressure," says Cannon. "When you're doing grading of trenches or slope work, it helps if you're able to slow down and still have full hydraulic pressure."
However, he cautions against "imitating" this function by turning down the throttle. "That's really a bad solution," he states, "because you need to have the efficiency of the machine in case of an emergency. By lowering [engine speed] with the settings, you can do more precise work."
Precision and careful planning required
As boom and stick length increase, so does the importance of operator experience with the machine.
Reviewing and adhering to load charts is critical. "With a long-reach excavators, you get into the realm of more of a crane," Cannon states. "You have to be a lot more cognizant of the load charts and the parameters that you can safely work under."
Slow, steady movement of the boom and bucket are also a must. "The operator has to be more careful/sensitive with [the excavator's] movements and the speed of the joystick movements," says Powell. "Due to the long reach, the speed needs to be reduced to maintain machine stability."
He notes that Liebherr excavators fitted with long-reach attachments are equipped with an "oil flow limitation" device, which reduces oil flow from the hydraulic pumps to the hydraulic cylinders of the working attachment. "This is in order to reduce the equipment's moving speed due to the longer working radius, which results in smoother operation and reduced risk of instability," Powell explains.
"Super Long Front excavators have the digging forces turned down so they won't damage the boom and arm by applying heavy forces through the structures," Hendry adds. "Even the heaviest duty Long Fronts have reduced digging forces."
Also essential to long-reach operation is patience. "SLF excavator operation is patient, deliberate, methodical and planned. Use pull and push movements only and absolutely no side sweeping of the bucket," Hendry states.
"SLFs can be used for slope grading," he adds, "if the machine is sitting flat on the ground and the operator can pull the grade to him."