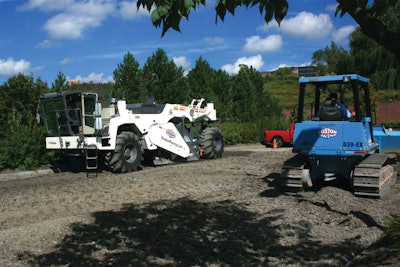
In the fall of 2009, Ruston Paving was approached by REIT Management and Research in Fairport, NY. REIT Management's Woodcliff Office Park had a 150,000 SF deteriorating parking lot, and Ruston Paving was asked to provide options for the repair and reconstruction of the area. The project was to be phased over 3 years to enable the active parking lot to remain in use.
During the first phase of reconstruction in the fall of 2010, Ruston Paving was contracted to mill and replace a portion of the parking area surface, as specified by a third party engineer’s design. Once the original surface had been removed and the underlying base evaluated, it was determined that it was necessary to remove, undercut and replace large areas of subgrade and install subsurface drainage in order to stabilize the area for final surfacing.
"Once we got down to the stone subbase, we found failures. 20% to 30% of the entire area had to be reconstructed," says Alex Marchese, project manager for Ruston Paving. "This resulted in more than anticipated expenditures and extended the work schedule significantly."
"Once we started doing the excavation and trying to remediate the core base condition, the areas with failures just kept growing and growing creating the need for deeper undercuts and drainage," says Lang Butler, vice president with Ruston Paving.
After the expensive lesson learned from the first phase of the parking lot reconstruction, REIT Management’s engineer suggested a full depth removal and replacement of the stone base and pavement for the next phase, which was to begin in the summer of 2011.
Ruston Paving then made the recommendation to REIT to consider full depth reclamation (FDR) with a Portland cement stabilization option.
"We realized it was something we should address over the whole area instead of just isolated areas," says Butler.
A quality fix
The FDR process reconstructs worn out asphalt pavement by recycling and modifying the existing material on site. The old asphalt and stone subbase are pulverized, blended and compacted to produce a strong, durable base for either an asphalt or concrete surface. In most cases, additives, such as Portland cement, are incorporated into the FDR process to enhance the stabilizing characteristics.
FDR uses the old asphalt and base material for the new pavement. There’s no need to haul in aggregate or haul out old material for disposal. Truck traffic is reduced, and there is little or no waste.
There are many advantages of the FDR process over the traditional method of full depth reconstruction, says Tim McConnell, pavement and soil specialist with Ruston Paving.
"You can get into a lot of unknowns with full depth reconstruction," says McConnell. "With FDR, it's a quality fix. You can repair the entire area at one time with no guesswork. You create a uniform area to start out with for your new pavement, which is always important. And you get away from all these little patching areas."
Repairing the entire area is one benefit of FDR; the other is the Portland cement, which helps stabilize the base and create a more uniform platform that is a more structurally competent base, says McConnell.
"Portland cement helps with moisture issues, which we had a lot of on this project," he says. "It also strengthens the materials you have in place to create a base that's structurally more superior to an aggregate base even if it's on fabric."
FDR also has the greatest bang for its buck, says Butler. "REIT was able to take advantage of a 30% to 40% cost savings while providing a better product and shortening the construction schedule on this project," he says.
As originally specified, the entire recycled area was then paved with two layers of hot mix asphalt, 3½" of binder and 1½" of top. The final phase of the project will be completed this year, again using FDR.
Moisture challenges
One challenge on the REIT project was "nasty soil and moisture problems," says Marchese. The parking lot sat on a 30-foot fill site. "10 or 15 years ago, they brought this area up just to build the parking lot," he says.
"Once we got into the subgrade, you could almost sink out of sight," he explains. "There were many borings done onsite that identified a lot of organic soil and a high water table below. We were on the side of a cliff – there was water running down the cliff and under the pavement. Just a lot of underground water issues to deal with."
The weather during the second phase of the project was also a challenge. "Had we gone the conventional remove-and-replace, the weather would have slowed us down. It just poured on us," says Butler. "If we had the parking lot opened up for remove-and-replace, and we boxed it out, and we got the rains that we got, that parking lot probably still wouldn't be paved. But with FDR, we were able to incorporate the Portland cement into the base as it poured rain on us.”
"Here we are on top of 30-foot fills with terrible material underneath and we were able to pave as scheduled," he continues. "Many times, if you're caught in the rain with a full box-out, it can shut your job right down."
Tighter areas
Ruston Paving has been performing the FDR process with its own equipment for the last 20 years. The company performs the process on both roadways and parking lots typically using a Wirtgen 2400 reclaimer, a Stoltz site spreader and complimentary compaction and grading equipment.
"Parking lots are more challenging, especially those with parking bays," says McConnell. "They're just tighter. We're used to paving and grading in those tight areas. There's actually a tremendous market for parking lots – we do a lot of FDR work that others wouldn't do because of the tight areas."
Ruston Paving usually concentrates on commercial work, not DOT jobs. It has used FDR on subdivision roads or city streets, which are fairly easy compared to parking lots, says McConnell. "For the really tight parking bay areas, we have a rear-drum machine that we use," he says. "We have the capabilities to do tight areas with our smaller equipment. That's what sets us apart."
Butler notes that the company has recently purchased more efficient equipment that is driving its efforts in expanding and doing more FDR and "green paving" work.
"Our new equipment is highly automated and computer-driven for adjusting the mixing depth or amount of material spread," he says. "Our site spreader has a dustless operation with a dust control measure to ensure the least amount of dust is produced."
The greatest challenge
The REIT parking lot project had several challenges, but the greatest challenge was educating the client about the advantages of FDR, says Marchese. "The hardest part was trying to get the owner to buy into FDR over the traditional method," he explains. "Other contractors will say, 'don't save it, pave it.' They'll haul it off site and rebuild the pavement. FDR is a sustainable process that keeps everything on site."
“Just in transportation costs, clients can save money,” says Marchese. “In traditional methods, like remove-and-replace, material has to be hauled off site and new aggregate is purchased and hauled back in. With FDR, existing material is used on site, eliminating unnecessary fuel, disposal and material costs. On average, clients can realize a 20% to 40% saving by using FDR.”
"It's a real learning process for the owners," says Marchese. "We had to educate them, and when they understood the benefits, they decided to take a shot and try FDR."
To educate REIT, Ruston Paving had several "lunch & learns" and spent a lot of time communicating with the client. "REIT had its own internal engineer that we spoke with, and once he was on board, we were good to go," he says.
In order for processes like FDR to become widely accepted, companies like Ruston Paving have to get the word out and get engineers and owners on board, says Don Barry, director of business development for Ruston Paving. "The success of this process relies on the acceptance and use of the process by property owners and developers as well as professionals in the construction industry," he says. "It takes a lot to get past the idea of, if it costs less, it can't be as good of a product.”
The growth of green paving
While it might take some effort to get engineers and owners to buy into FDR, Ruston Paving knows that green is on its side.
"Green paving is the wave of the future," says Butler. "It's becoming more prevalent and more of an issue. Owners and engineers will be required to support the green side going forward."
Butler says Ruston Paving has bought into this process – not only supporting the concept with new equipment but also promoting a process that saves the Earth for future generations.
"What most excites us about the FDR process is you can kill two birds with one stone," says Butler. "When compared to conventional rip-and-replace, not only are you able to save money, but you're saving the environment. That's just a great concept."