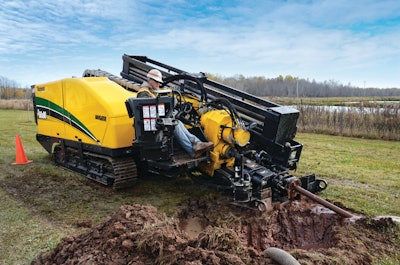
Attendees of the International Construction and Utility Equipment Exposition (ICUEE) last fall had the chance to check out Vermeer's new D60x90 Navigator horizontal directional drill and watch a live demonstration. But for Push Inc., a Wisconsin-based contractor specializing in underground utility, power, fiber optics, water and sewer installations, the demo started several weeks before the drill hit the market.
Push Inc. has a longstanding relationship with Vermeer. So when the new drill was being developed, the contractor was asked to evaluate the prototype. "I think the basic reason Vermeer let us use the machine is they know we will put it to its maximum test," says Russell Johnson, operations manager at Push. "They wanted us to see what we can wear out, or what does wear out, before they go into production."
A combination of speed and power
Push's sewer and water boring crew has been using the D60x90 for roughly three months on various projects. In addition, it has about a dozen Vermeer drills in its fleet, ranging from the 24x40 up to 100x120 size class.
Recently, Push was brought in as the directional drilling subcontractor on a project calling for installation of 15,000 ft. of 8-in. forced sewer main from Rudolph to Wisconsin Rapids. Directional drilling was selected due to the environmentally sensitive DNR wetlands situated between the communities.
Johnson chose to use the prototype machine on the project rather than one the company's other drills. "The reason we're using it because of the power it has and the length of the bore we can complete with it," he says. "It has better capabilities than our smaller drills, and it's easier to run than our bigger ones."
The D60x90 is powered by a 185-hp John Deere Tier4i diesel engine, which delivers 9,000 ft-lb of rotational torque and 60,000 lbs. of thrust/pullback. It comes with 10-ft. configurations of 2.875-in.-diameter Firestick drill rods to minimize the operational footprint, or 15-ft. rod lengths at 2.875-in.-diameter to maximize onboard drill rod carrying capacity.
The project is being completed in roughly 1,000-ft. shots. "We like to go farther, but the soil has prohibited us from getting farther. It's a kind of a sandy soil," Johnson notes. "We find 1,000-ft. increments are not a problem, and the pullback so far has been very successful. That shows some of the capabilities – how far out we're going with the machine length-wise."
The ability to quickly and easy load the drill rod has helped to speed up the drilling operation. "The quickness of the machine is a big item," says Johnson. "The loading of the rod into the drill chamber is very quick... It may only be a minute to a half a minute quicker than another machine, but that makes quite a bit of difference."
The drill is also available with quick-change rod boxes containing up to 300 ft. of drill rod each. They can be removed by releasing two pins and a single latch."You have to change the rod box about every 500 ft. or so," says Johnson, "and the rod box is designed very well."
The drill's compact size has proven very desirable, as well. "We like the small footprint," says Johnson. "It fits very nicely in the right-of-ways, and I don't need a lot of support equipment to move the machine around."
Quick response
As of late December, Push Inc. had completed approximately 8,000 ft. of the 15,000-ft. installation, with Vermeer closely monitoring the drill's performance every step of the way.
"They're up here and they've been talking to us all the time, getting data from the machine, getting information from the operators and how it works," says Johnson. "They've been doing that on a regular basis to see what we think of it.
"We've had different operators on it, so we have different opinions. We've had a few things that have had to be changed, things that didn't work as well and they've changed it around," he says. "They've been very responsive. They're keeping a very good eye on it."
Fortunately, Push's crews have had little to complain about. "It's actually been a high-performing machine," Johnson comments. "And even on the prototype, I can't find too much that's been wrong with it.
"Put it this way, if our operators don't like it," he states, "they will let us know."