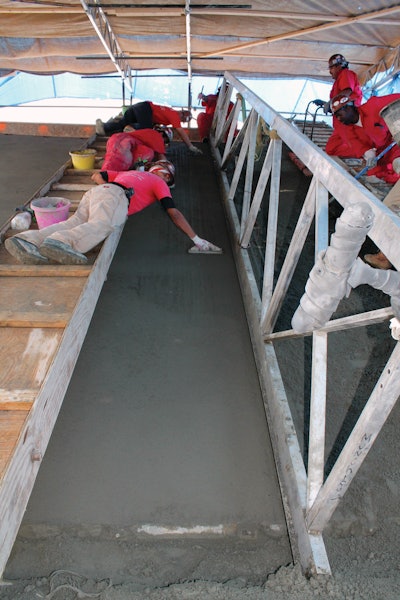
In an industry where contractors are feeling pressure to produce precise floors for tighter margins on shorter schedules, most concrete companies have adopted technologies and new equipment as a means to increase production. At Carolina Floors, technology is an integral part of the company's concrete placing and finishing business, but hand work and craftsmanship is the company's core.
Only a crew of talented concrete craftsmen could have pulled off the work Carolina Floors performed at the Giordana Velodrome, an Olympic-style bicycle racing facility in Rock Hill, S.C. The concrete track, which will host the 2012 and 2013 USA Cycling International Omnium Track National Championship, boasts a 42 degree bank turn and an engineered convex cup, requiring Carolina Floors crews to hand finish the project with the precision of a superflat floor.
Smart growth
In 1985, Jeff Rogers started Carolina Floors with $5,000 and three employees. He built his company's reputation and client list by bidding the less profitable, "leftover" concrete work that other companies didn't want to do, like dumpster pads, walkways and equipment pads. Today the company, headquartered in Rock Hill, S.C., employs 30 concrete masons and performs more than 4,000,000 square feet of concrete floors annually in a three-state region.
Carolina Floors' growth was steady but never more than the company could handle. "I have seen many companies fail because they had too much work and too many commitments," Rogers says. "One thing we have tried and have been successful at is we have maintained moderate growth and achieved a wide diversity of projects we are able to do. We count that as our success for being in this business this long."
A high standard for quality
Central to Rogers' theory on diversification is having knowledge on staff to successfully complete any concrete project that Carolina Floors takes on. "Over the years we have accumulated folks who have the knowledge to compete in all phases of concrete construction, whether it is superflat floors, laser screed floors, tilt-wall construction, concrete paving, power plants, you name it. No matter what the project is, if it is concrete we have acquired the knowledge to be a successful place and finish contractor in that arena," Rogers says.
While admixtures and equipment technologies have helped improve the industry and allow contractors to more easily perform certain types of construction, Carolina Floors included, Rogers also sees a downside. "You can never replace craftsmanship with technology or equipment," he says. "During the boom up to 2009, we had guys apply to work for us and tell us straight off the bat they could run a rider and a laser screed but didn't use hand tools. This leads me to believe there are companies out there that allow employees to only ride a trowel machine, and if they can't get close to a wall or piece of pipe that area of the floor just remains rough and unsightly. That's something we would never do."
A few core beliefs help Rogers differentiate from the competition. For one, there are the "little things," like cleaning up around the jobsite, having a clean vehicle and employee uniforms. "We've learned no matter what technology comes down the pike, those little things will never be replaced," he says.
Another belief his father passed on to him. "My father told me when I was young that your handwork sells your job," Roger explains. "The average customer can't walk your floor and tell if it has high or low spots or a dip or bump, but he can recognize edges that weren't leveled or a crooked saw joint. It's those small things that sell your work, year in and year out."
The other thing Rogers says sells your work and makes a company stand out above the competition — how you take care of your mistakes. "In the concrete business, like any other good business, when everything is going as planned we are all the same," Rogers says. "But how our customers gauge us is how we handle things when a job doesn't go as planned. Periodically we all make mistakes, and how we handle mistakes separates the good companies from the companies that are no longer in business."
Project profile: Giordana Velodrome
The Giordana Velodrome project exemplifies Carolina Floors' commitment to quality and craftsmanship. Not all concrete contractors could have finished this job. In fact, the plans alone scared away most of the companies looking to bid the project. When the Rock Hill Parks, Recreation and Tourism Department announced the construction of the velodrome, it was the largest concrete job in a 150-mile radius and created a buzz among concrete contractors in the area.
"Then the plans came out with a 45-page method statement from the architect on how the job was to be constructed," Rogers says. "Upon most of the people looking at the plans and reading the method statement, the excitement on the street changed to 'We don't want to fool with this.' That narrowed the competition. In the end there were only four bidders."
Rogers says a few things attracted him to the velodrome project. First, the site is only three miles from Carolina Floors headquarters. Second, it was a highly complex project. "The thing that intrigued us from the start is this work, in the finishing stages, is all by hand. There is no mechanical equipment used in the finishing aspect of this track," Rogers says. It was the kind of project that required a talented team of concrete craftsmen.
Carolina Floors won the bid for the concrete work. The general contractor on the project was Leitner Construction, Rock Hill, S.C., and the formwork and rebar contractor was Kempf Contracting, Indian Trail, N.C. German firm Schuermann Architects built the design; the company has been designing wood and concrete velodromes around the world since 1926. The general contractor also hired an onsite engineer who shot thousands of points with a total station over the course of the project.
The velodrome is an 820-foot (250-meter) oval-shaped track. Its banks rise as the track curves into a turn and lower coming out of a turn. One slope rises to a pitch of 42 degrees, making it the steepest outdoor velodrome in the United States. In addition to the sloped walls, the design also incorporates a convex cup that allows racers to achieve higher speeds than they could achieve on a flat track. The bikes that race on this track can travel up to 44 miles/hour.
The track was constructed in a series of 50 17-foot-wide panels, 27 feet long. Each panel included a 5,000 psi 4-inch base slab with a 2-inch max slump, poured at a rate of five panels a day. Once the base slab was in place, the rebar and formwork contractor placed double mat No. 4 rebar 4 inches on center and put in the edge forms. Working at a rate of one panel a day, Carolina Floors crews placed a 10-inch-thick, 5,000 psi concrete with a 2-inch max slump with crane and bucket, vibrated the slab and struck off. A rolling tent kept the sun from drying out each slab so crews could then place a 1.5-inch grout topping wear surface on top of the 10-inch slab in a wet on wet application.
The grout application was unique and a challenge for Carolina Floors. Each batch of grout mixture consisted of 188 pounds of cement, 575 pounds of sand and only 6.5 gallons of water. The German architect called it "earth damp." And Carolina Floors crews mixed and placed 14 batches of the grout each day via a "bucket brigade" — a line of men that handed off the grout from the mixer up the panel with 5-gallon buckets. Once they placed the grout, crew members screeded the topping with a German-designed aluminum screed and hand finished with wooden hand floats. Crews spent roughly two hours a day placing the 10-inch subbase and six hours a day placing and finishing the 1.5-inch wear surface.
The grout topping is the key to the track. The texture, which feels like something between a 200- and 300-grit sandpaper, helps keep the bikes in place as they circle the track. But that feature was not easy to accomplish. "In Europe, contractors use sand from ancient riverbeds to achieve the texture; we don't have ancient river beds like that here," Rogers says. Instead, Carolina Floors spent two and a half months testing sands and grouts and mailing test panels to Germany where the architect would run his hand over them and tell Carolina Floors if they were close. "The entire time I'm thinking, 'Oh my, what did we get ourselves into?!' I couldn't sleep, I lost weight ... I was extremely worried," Rogers recalls. It took 25 test batches to finally achieve the correct texture, which turned out to be a mixture of manufactured sandblast sand and local sand.
Challenges aside, the final velodrome project was a success. Carolina Floors finished a labor intensive, highly precise, handcrafted floor with the tools it holds in the highest regard – the talent, craftsmanship and quality mindset of its employees.
And Rogers says it will be a project everyone involved will remember. "The superintendent on this project, company vice president Joe Briggs, created a comradary among our men, the gc's men, the ready mix producer and the architect and engineers. Each member of this team will talk about this project as one, if not the highlight, of their careers," he says.
Company Summary
Carolina Floors, Inc.
Rock Hill, S.C.
www.CarolinaFloors.com
Founded: 1985
Owner: Jeff Rogers
Number of employees: 30
Affiliations: ASCC, ACI, local NRMCA chapter
Services offered: Concrete placing and finishing, including superflat floors, tilt-up walls and pervious concrete
Key products & equipment: Somero S240 Laser Screed, Wacker ride-on trowels, Multiquip walk-behind trowels, Terex-Morrison material spreaders, Wacker vibratory screeds, Spectra Physics laser equipment, iPads, Exaktime