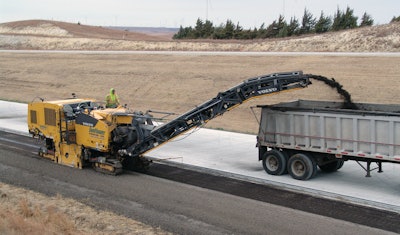
Sunflower Paving Inc., a full-service paving company with locations in Lawrence, Topeka, and Kansas City, was originally founded as a flatwork company 30 years ago. Gradually, Sunflower Paving expanded its concrete division into other facets of commercial concrete, including everything related to horizontal concrete, such as public and private work on curbs, sidewalks, paving and handicap ramps.
In 2009, the company purchased Asphalt Improvement Corporation to form its asphalt division, specializing in county highways, municipal street overlays, parking lots and asphalt patching.
The expansion into asphalt spurred Sunflower Paving to form a new milling division just a year later to help crews keep up with an increased workload.
"We started the milling division because while we were doing asphalt work, we were waiting on milling subcontractors to arrive and get the work done on time," says Jeff Engroff, president of the Lawrence-based company. "We decided to bring the milling in house to do milling operations on our own jobs and for other contractors."
Finding the right machine
A milling machine is obviously a significant investment, so Engroff and Travis Burris, director of the asphalt and milling divisions at Sunflower Paving, made sure to do their homework.
"Before we buy a new piece of equipment, we determine what the guys in the field want — not only what they're used to, but what they want to use," Engroff explains. "We research the brand in terms of its quality and the service the dealer will provide. Then we try to make the best judgment possible to acquire the highest quality machine and the best service we can get for the price."
After careful consideration of all equipment alternatives, Sunflower Paving decided to purchase the Volvo MT2000 milling machine.
"The Volvo MT2000 was a new machine and the company went out of its way assure us they would stand behind the machine," Engroff adds. Sunflower Paving's experience, results and success with the new machine affirm the company's decision.
"Adding the capability of a new milling machine not only allowed us to satisfy our jobsite needs, but it also allowed us to be more flexible in our work scheduling," Burris adds. "It was 'hit or miss' when we were waiting for subcontractors. Now, having our own milling machine allows us to take care of the work more quickly, easily and more efficiently."
Sunflower Paving purchased the machine from The G.W. Van Keppel Company, Kansas' full-line Volvo dealer headquartered in Kansas City, KS. "We work with both the Topeka and Kansas City branches of G.W. Van Keppel. They provide us with the training that we need to operate the equipment efficiently. They are quick to help us with our service and support needs," Engroff says.
New services provided
Sunflower Paving's milling crew, which consists of Foreman Lee Torneden and two to five crew members depending on the application, uses the new milling machine on asphalt projects, including full-depth patching on streets, city street milling and overlay projects, and county and state highway milling and overlays. They also perform concrete milling on road and bridge projects.
Powered by a Cummins QSX-15 6-cylinder engine, the unit with a 78.75-inch drum handles milling depths up to 14 inches and has three distinct cutting speeds to allow the operator to match productivity and fuel consumption and meet sound level restrictions for each individual project.
Advanced technology aboard the milling machine provides clear communication regarding the milling operation along with operator convenience, including multiple diagnostic screens with easy-to-read messages displayed for quicker diagnostics and troubleshooting. And the load control technology keeps track speed from exceeding the parameters for conveyor capacity and engine speed for improved productivity. Its stability control system has a dedicated sensor that monitors the cross slope of the machine and automatically adjusts the support legs back into balance if the machine begins to operate outside the acceptable balanced range.
For ease of service and reduced downtime, all key components of the milling machine — the engine, hydraulics, fan and coolers — are within easy reach in the protected environment of a walk-in service compartment.
"The biggest difference is that it has the ability to go out and mill 10 or 12 or 14 inches of asphalt in one sweep," Engroff says. "It's just a real hog and can do whatever we ask of it."
More power = more efficiency
That power, says Torneden — who operates the machine and performs routine daily maintenance — helps the crew complete a variety of projects much more efficiently.
"We've done several large patch jobs that would have taken us a couple of days before, using other equipment in our fleet. Now, we can bring the new milling machine in and get the job done in a matter of hours," Torneden says. "We recently completed a county job that had 12 miles of paving and included 3,500 tons of patching. It was full-depth, 6-inch patching, ranging from 50 feet long up to 300 feet long. What we did in just four days would have taken weeks.
"Milling 6 inches deep, we easily can get out 30 tons in about 10 minutes. Then it takes the lay-down crew about half an hour to fill it back in. Increasing our production rate is what helps us get the work," he says.
Torneden says the crew's biggest production day with the MT2000 has been 8,000 tons in 12 hours.
"On that day we just happened to have a good, mile-long strip about 7 inches deep, and we had all the trucks we needed to run all day," Torneden says. "We've had a lot of people comment on how fast we can load trucks with this unit."
In addition to power and production, Torneden says he appreciates the design of the MT2000 and the operator's station.
"The design is very centered. I can steer the machine with my right hand, the middle control moves the conveyor left, right and up and down, and the pistol grip on the left controls forward, reverse and speed. Then there are seven different screens I can view on the monitor in front of me to see how the machine is operating. If something isn't right, it will identify the problem. That technology is really nice in a lot of ways."
The bottom line, Torneden says, is that the MT2000 is one of the key factors in the success of Sunflower Paving's new milling division. "Acquiring a milling machine has given us more opportunity to do more jobs — jobs we couldn't have completed without it."