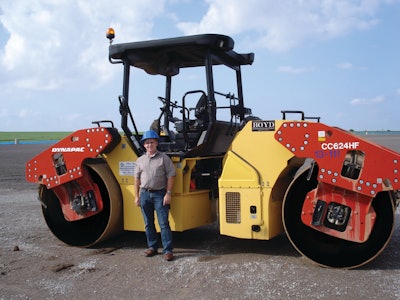
When Silver Star Construction Co. in Moore, OK, decided to add an 84-inch asphalt roller to its fleet, Craig Parker, executive vice president of Silver Star, knew he needed objective information before he made an investment. "I needed something more definitive in my hand to make the decision – not just other people's opinion," said Parker. I needed something I could hang my hat on, so I set up a roller demo."
Test Day
Parker invited recognized road construction equipment manufacturers and their local dealer representatives, including Dynapac and local dealer CL Boyd, a manufacturer of oscillatory rollers and another roller manufacturer with a vertical vibration system.
The next step was to put the rollers to the test. Parker, along with Jack Shannon, asphalt superintendent, and Jan Graham, asphalt foreman, arranged the demonstration to take place on a 2000-foot section of a longer 7-mile Oklahoma Department of Transportation (DOT) thin-lift overlay project. On May 18, 2011, the Silver Star team and representatives from the three roller manufacturers put them to work. An Oklahoma DOT inspector was also on site to ensure compliance with the project's specifications.
Parker went to great lengths to keep the demonstration fair for each participant.
- The 7-mile project allowed plenty of room for each roller to operate on its own 2000-foot test section within the same mile of each other.
- Silver Star set up the demonstration area in the middle of the 7-mile section to ensure the asphalt plant was fully calibrated and running a consistent mix prior to the demo.
- The weather on the chosen day was forecast to be excellent, which it was. This helped keep the temperatures of the mix consistent.
- An independent testing lab was on site to gather and analyze the data.
"I wanted to be as absolutely independent and accurate as possible. This was the only way I could get a fair analysis, and there couldn't be any arguments about possible differences in conditions," explained Parker.
Sitting in a vertical line approximately 2000 feet apart, each roller ran one at a time on its test section to have a consistent run. Each roller began in breakdown mode behind the paver. Technicians from the independent testing lab checked the roller patterns behind each roller from the time it got on the mat and then after each vibratory pass or breakdown pass. "We tested behind every pass each roller made to look at the compaction results each one achieved," said Parker.
Once the results were gathered from the breakdown mode, the demo roller moved to the back of the compaction train. A rubber-tired roller was used between the breakdown roller and the finish roller. The demo roller was tested as a finish roller in the next test section so it was tested in both areas.
As the demonstration progressed, the results were not immediately available, but Parker was careful not to rush the technicians. "The test lab can't always keep up with gathering the results as you're moving the train along," explained Parker. "It took until the end of the day for me to get the results in hand and analyze them."
Parker pointed out that prior to the demo, he was getting biased and conflicting information about the rollers he was comparing, so he was a bit surprised by what the results revealed.
Silver Star's crews had been familiar with oscillatory and vertical amplitude vibratory rollers from past projects. Going into the demo, they felt the 84-inch oscillatory roller would perform better.
Silver Star's crews also had experience with multiple size drums, but as Craig Parker pointed out, "Each drum size is going to compact differently on the job. Just because a 66-inch drum in one brand is better than another that may not be the case when you get to a different size. I knew what the test results showed on the 66-inch side of the equation, but on the 84-inch side it was something totally different."
Parker remained neutral. "I told my crew that we were going to look at whichever one did the best on the job, and then compare the prices. We were willing to spend more money if needed to get the roller that did the best job getting compaction. If you start having trouble with densities, you can run into several thousand dollars very quickly. If you can avoid that just by having the correct equipment on the job, it is money well spent."
Analyzing the Results
Compared to an oscillatory system, the Dynapac employs a standard or vertical compaction method. On the test section, the Dynapac 624 took half a pass more to get the same compaction density as the oscillatory roller. However, as Parker explained, "You still have to complete that half a pass. There are no savings on time or effort on that half a pass."
The Dynapac 624 also offered Silver Star more flexibility since it could be successfully used on thin-lift applications < 2 inches, such as the test section, or on thicker lift applications 2 inches. Because of Dynapac's use of traditional compaction with a higher amplitude setting, Silver Star can use the 624 on mainline operations where they are doing inlays.
"We just completed an inlay project on the Turner Turnpike," said Parker. "That operation was a 3-inch lift and a 2-inch lift. It was a mainline, high-production operation, and it performed very well."
Silver Star meets their tonnage-per-hour production goals with the Dynapac CC624HF. As Silver Star continues to put its new roller to work, it also continues to live up to the test results and performance expectations of the crew. Silver Star's crews, and especially asphalt superintendent Jack Shannon, also agree that the 624 was the clear choice.
"[Jack] and I had a very frank conversation, and if he had been very insistent on going with [the oscillatory roller], I would have listened to him," said Parker. "But once I showed him the test data and went over it with him, he was perfectly happy with the way we went, and has been happy with the machine ever since."