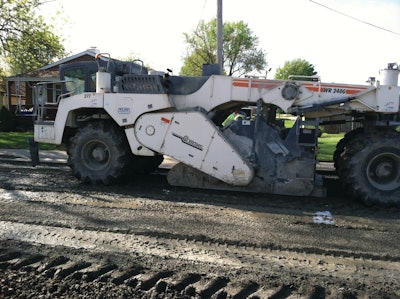
Contractors are continuously implementing environmentally friendly processes for asphalt repair to meet new standards and specs by cities and states. Regardless of the project, more communities are looking for ways to update their existing surfaces in both a cost-effective and green way.
In a recent project, Midwest Stabilization completed Full Depth Reclamation (FDR) of Maple Street located in Hartford, IL. Midwest Stabilization, located in St. Louis, MO, is a part of the Byrne and Jones umbrella, and it travels throughout the Continental U.S. with the reclaimer equipment to complete full depth reclamation projects.
"We sit with every client and look at how we can best serve their needs," says Brett Gaither, business development at Midwest Stabilization. "For this city street, they wanted a better surface than a chip and seal. The original bid was for removal and replacement of the existing road surface with hot mix asphalt. Midwest Stabilization priced that option along with FDR. FDR turned out to be a better solution, better price, and by adding the Portland cement it increased the streets stability."
The Maple Street project began April 2, 2012, and it was completed in eight days. The two-lane road ran 1,600 lineal feet east and west through Hartford crossing over a railroad tracks. The work was completed in two sections, east of the railroad tracks and west of the railroad tracks.
The existing surface had 2-3 inches of chip and seal with a sandy, dirt base. "The dirt and rock base was not stable resulting in base failures," Gaither says. "There were several potholes and utilities on the road resulting in a bumpy and hazardous ride for residents. The city was looking for a road that was more stable."
The first day crews milled 3-4 inches of the chip and seal surface. "There was a 3-4 percent crown in some areas, so we had to try and get it down to a 2-3 percent slope by milling off extra material," says Kevin Klette, project manager. "After that we hauled away the milled material."
On the second day, the manholes were raised and lowered. The project also had several monitoring wells used to monitor ground water. "We had to frame the monitoring wells and pour new concrete," Klette says. "We also poured two concrete handicap approaches. The crews ripped out the old concrete sidewalk and gutters installing new ones."
With some of the sidewalk work carried over to day three, crews also graded the road. The surface was re-graded to even the crown and slope.
After this work was complete, crews focused on the surface west of the railroad tracks. "First, we spread two loads of Portland cement," Klette says. "Then we took the Wirtgen 2400 reclaimer and tilled the cement into the surface. After that, we added water from a water truck while it was pulverized. Finally, we re-graded the road and compacted it with a smooth drum roller."
A SS1H asphalt emulsion tack coat was applied to the surface to preserve the Portland cement. "The fog seal locks in moisture and allows the Portland cement to cure," Klette says. "The western section of the project cured for 72 hours."
By the sixth day, crews moved to the eastern side of the railroad tracks completing the same stabilization process as the western side of the railroad tracks.
An extra day was given to allow the eastern section enough curing time. "The following day we paved the western section of the project," Klette says. "We applied 3 inches of asphalt in two lifts consisting of 1.5-inch binder mix and 1.5-inch surface mix. We completed both lifts on the western section of that day." The same paving work was completed the following day on the eastern side of the project.
As a result of using FDR, Midwest Stabilization was able to save the city 15 percent. The original bid for Maple Street was remove and replace, and would have required a removal of 12 inches of material with the replacement of 12 inches of material. "With FDR we only had to remove 4 inches of chip and seal surface," Klette says. "As a result, we were able to save money on trucking, material and labor. We completed the FDR in 8 days while the remove and replace would have taken 16 days."