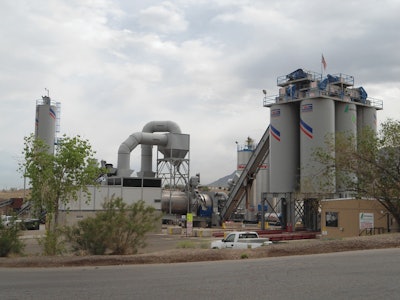
While asphalt plants continue to operate at lower production rates, it has become even more crucial to maintain the market share to survive the current economy. Lafarge of New Mexico has found success through the introduction of materials and mixes initially unavailable in the New Mexico market. Warm mix asphalt (WMA) and recycled asphalt shingles (RAS) are two products Lafarge introduced to the Albuquerque market to maintain a step-up on its competitors.
There are three Lafarge plants in operation in New Mexico including plants in Albuquerque, Bernalillo and Santa Fe. Currently, the three facilities have the capability to produce over 1.5 million tons a year. All of the facilities produce hot mix asphalt using between 15-35 percent reclaimed asphalt pavement (RAP). Every facility also has the capabilities to produce mixes with RAS, and the Albuquerque facility is the only plant capable of producing WMA.
The Albuquerque plant was acquired by Lafarge in 1997 from Redland PLC. Originally, the Albuquerque plant was a 350 ton per hour batch plant; however, updates were made to the plant in 2010 including the addition of WMA production. "The 350 ton per hour batch plant was extremely old, and it was time to update it," Kugler says. "We purchased a Gencor 500 stationary drum plant to replace the original batch plant at the Albuquerque location. The plant we ordered had foaming capabilities, and we felt we could utilize it to become the first in our market area to offer our customers an innovative product. "
Lafarge chose the foaming system due to the several environmental benefits. "Environmentally it was the right thing to do because it requires less energy to produce the material, and the additives associated with producing WMA increase the cost of the binder," Kugler says. "We wanted to offer our customers an innovative product without increasing their cost over hot mix asphalt."
Most of the Albuquerque plant's business is generated through governmental projects followed by the commercial and residential markets with an increased crossover in segments due to the economy. The customer base spans small C.O.D. to the New Mexico Department of Transportation.
New materials, new opportunities
As with most producers in the industry, the economy has been the biggest struggle Kugler notes for the Lafarge plants. Despite these struggles, the plants have been able to hold strong in their markets. "Innovation, the ability to adjust to a declining market and our people has allowed us to remain a leader in our industry and market area," Kugler says. "The biggest innovation we have used is warm mix asphalt. We were the first plant in the Albuquerque area to offer and produce warm mix asphalt, and we've helped establish it in the market area."
Prior to producing WMA for the market area, Lafarge teamed up with one of its paving customers to pave an area around the plant with a comparison patch of HMA and WMA. Several tests were also completed on the test patches. "We had an independent laboratory pull samples and cores from both areas for testing with the idea of making any corrections to the warm mix," Kugler says. "From the first ton produced, we've encountered no problems with the warm mix."
After installing the new plant in 2010, Lafarge took additional steps to reach out and discuss WMA, a product new to the area, with the local paving industry. "In early 2010 we held a seminar on warm mix and how it was produced through our plant," Kugler says. "The room was full with paving contractors and representatives from city, county and state agencies. The product was well received, and within a month we started to produce it for commercial projects throughout the state."
The production upgrades don't stop there. This past May, Lafarge took steps to store and produce mixes containing recycled asphalt shingles (RAS). To accommodate the new materials at the plant, one storage bin was converted from storing RAP to RAS. "We are getting a stock pile of shingles at the plant to crush them," Kugler says. "We will start using it soon. It [RAS] will be used in specific commercial mixes to start until we get a feel for it and see how it works."
One challenge of producing RAS is the limited availability of shingles in the Albuquerque area as well as the lack of a local shingle factory. As a result, Lafarge has sought to create a relationship with roofing contractors. "We have an exclusive relationship with two roofing contractors who can dump shingles at the Albuquerque plant," Kugler says. "Part of that process is only including shingles without asbestos. The roofing contractors have been bringing shingles since May 1."
While the Albuquerque plant has recently received the most upgrades, Lafarge is currently installing a natural gas line in Santa Fe. "We are working on putting in a natural gas line for the burner so we aren't use burner fuel," Kugler says.
Through updates and upgrades to the plants Lafarge has continued to maintain a firm position in the New Mexico market. By expanding production into other materials, Lafarge has been able to utilize the innovation achieving success.