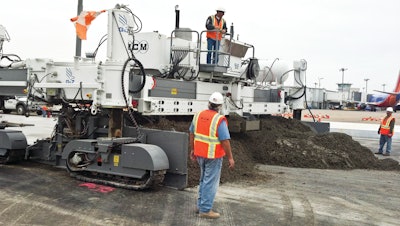
The Challenge:
Remove concrete, grade the subgrade and base, relocate utilities and place 298,000 square yards of concrete pavement at the Dallas Love Field Airport while allowing a number of gates to remain open during construction.
The Players:
MCM
The Process:
The $500 million-plus renovation project at the Dallas Love Field Airport is scheduled to take four years of construction wrapping up in 2015. MCM, a heavy civil and building contractor based in Miami but with divisions in Texas and Panama, has a $68 million contract on the project including removal of concrete, grading the subgrade and base, relocating utilities and placing 298,000 square yards of new concrete pavement.
Most of the concrete pavement is 17-inch jointed plain concrete with no steel, although smaller amounts of 15- and 8-inch concrete pavement will be needed. To tackle the paving, MCM bought a four-track S850 Guntert & Zimmerman slipform paver fitted with a Leica Geosystems stringless control package. MCM gains about 15 to 18 percent in production by using the stringless controls, compared to stringline since the stringless system eliminates the cost of line setting and the issues that go along with it.
"The biggest challenges are the small pieces of pavement and the phasing," said Luis Munilla, business operations manager for MCM in Texas. "Our average production days as we get into the largest segments of work are going to be in the area of 1,200 cubic yards per day."
"Many of our pavements out here are right on plan grade, or within 1/100 of an inch. The stringless controls really help trucking and production," Munilla said.
"Typically MCM paves either 25 or 30 feet wide and saws the pavement into 12.5-foot square panels or 15-foot panels," said Joe Roundtree, general superintendent for MCM’s Dallas Love Field Airport. "The Guntert & Zimmerman paver helps with placing small pieces because the tracks can turn 90 degrees under the paver at the end of a run."
And the stringless controls help with the small pieces, too. "We can set up the machine to do those pieces in the morning, and then we just move from one to the other, with no stringline," said Mark Vanness, the paving estimator for MCM in Texas. "The digital model is already programmed into the machine. You don’t have to worry about anything being in the way."
"One of the biggest advantages to stringless is that you create a 3D model," Munilla said. "Many people don’t consider this but that 3D model lets you check for flaws and problems that may not show up in any other way. When we build this model, we can actually look at the surface and check drainages and other things that keep us from running into bottlenecks and problems in the future."
With stringless controls, two robotic total stations utilize two prisms on the paver to "tell" the paver its precise location. A computer onboard the paver then computes the difference between the actual location of the paver pan and the design location in the 3D digital model. With that information, the onboard computer can automatically control the paver pan.
MCM has four robotic total stations on the project. "We have additional total stations out there so that we can check our depths and our pavement surface right behind the paver," Vanness said. "We have a man who stands on the rear catwalk of the paver when we get to the area where we need to check the height of the pavement. He uses a Leica rover and data collector to check the existing slab. That way we can move forward with confidence that we don’t have any issues with non-conforming pavement."
Quality control inspectors on the job "are thrilled" with the pavement edges produced by the Guntert & Zimmerman S850, Roundtree said. "The edges are sharp and clean, and this is a very big point of contention on airport jobs."