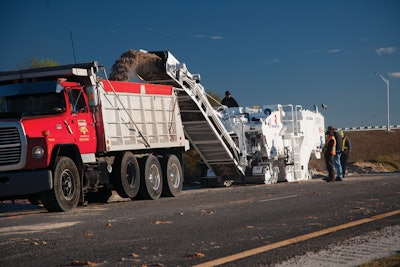
If you can improve machine availability by finding any problems quickly, that’s money in the bank. To that end, Roadtec recently introduced Guardian, a telematics system that permits you to quickly find virtually any possible machine problem through either the display screen on the milling machine or remotely from a laptop or personal computer. The Guardian system can also monitor machine performance and service requirements.
Guardian is first being offered on Roadtec’s new e-Series Tier 4 milling machines, including the new RX-600e, which will replace the RX-500. Guardian can provide machine operating data such as productivity and time to service intervals. And if there is a machine fault or engine fault, the system automatically sends an email to the owner or to Roadtec that a problem has developed with a specific system on the mill.
“For example, Roadtec received an email from a machine working in Florida stating that the signal from the left front pulse pickup was lost,” recalls Kyle Grathwol, owner of Grathwol Automation and author of the Guardian software. “A pulse pickup monitors the speed of the hydraulic motors that drive the tracks. On this particular machine, the left front track pulse pickup value showed zero and all other track pulse pickup values were normal.
“An engineer at Roadtec logged into that machine in Florida and confirmed the condition,” says Grathwol. The Roadtec engineer called the owner of the milling machine and told the customer the problem, and the customer quickly found a broken wire. “The problem was solved within 30 minutes of the time Roadtec got the email.”
Roadtec can remotely connect to any RX-600e milling machine in the world and examine all of its systems from a computer in Chattanooga, TN. The connection from the machine to the computer is wireless, with a cell booster to ensure that the machine has a strong signal, says Kyle Hammon, technical marketing coordinator.
Engine faults or machine faults will immediately trigger an email to the machine’s owner. An email will also tell the owner when the machine is due for service. If a fault occurs but no cell phone connection is available, the onboard computer stores faults until an Internet connection is restored, and then sends the fault email.
The Guardian system allows machine owners to monitor fuel consumption, engine codes, and other functional systems including alarms, starting circuit, cutter function, water, conveyor speeds, propel functions, load control, hydraulics and much more. For example, the system displays electrical circuits by showing inputs on the left, interlocks in the center, and outputs on the right. The circuits are basically displayed as a live schematic. If you look at cutter inputs, you might see the left cutter switch on.
Then look at the outputs, says Grathwol. Actual milliamps of current and desired milliamps are shown on the output side. If the desired output is 3 milliamps but the actual output shows zero, that means you have an open circuit.
“You can tell where your power flow stops and you can tell if it’s an open or shorted circuit,” says Grathwol. “A technician can see the whole schematic of the system – you can see the entire circuit from inputs to interlocks to outputs.”
Positive feedback
Steve Concannon is the operations manager at one of the country’s largest milling contractors, Pavement Recycling Systems, Mira Loma, CA. The company is one of the first to try out the RX-600e with the Guardian system aboard.
“We were able to get reports back on the operating performance of the machine,” says Concannon. “It was very beneficial for us to see what the fuel burn was and what the load on the engine was. That gave us some indication of the run time vs. the standby time. And we were able to evaluate all of that from the office.
“Another good thing is being able to make adjustments to the operating parameters of the machine," he continues. "We could call Roadtec to tell them a problem and have them make a machine adjustment through the computer immediately. It was fantastic to see the immediate benefits rather than to spend the money to have a mechanic come out and hunt for the problem.”
Concannon said his company worked with Roadtec to solve a problem with the calibration of the rear track steering. “It was off, and we were able to call in to Chattanooga to change the calibration,” he said. “We got that zeroed out and had it running perfectly in a matter of minutes.”
Concannon said he appreciates the onboard diagnostic capability of the Guardian system. “You don’t necessarily have to use remote diagnostics,” he said. “Just troubleshooting on the system itself is a big plus. The operator is able to search out the problem himself.”