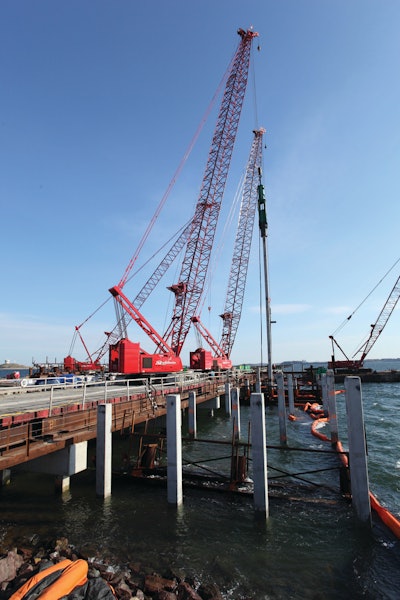
The Challenge:
Building a pier into Boston Harbor to lengthen one of Logan International Airport's longest runways
The Players:
J.F. White Contracting Co.
Baldwin Crane
Sterling Equipment
The Process:
Four Manitowoc crawler cranes are working on an expansion project at Logan International Airport in Boston to lengthen the airport’s longest west-to-east runway by building a 600-foot by 300-foot pier out into Boston Harbor.
Three Manitowoc 999s and a barge-mounted Manitowoc 2250 are helping the contractor meet the project’s demanding schedule. The Manitowoc 999s are being used in all aspects of the operation from driving 18-inch square precast piles and setting the precast concrete pile caps, to placing specially designed precast concrete beams, called NEXT (Northeast Extreme Tee) beams.
The Manitowoc 2250 is doing the bulk of the marine work from a 54-foot by 180 -foot barge. J. F. White Contracting Co., the project’s general contractor, is renting the cranes from Baldwin Crane and Sterling Equipment.
Jim Beach, project manager at J.F. White, said the greatest challenge has been the tight timeline and the constraints of working on a major runway within a busy, operating international airport.
“The schedule has been really challenging, especially since October, at which point we had to return the runway back to airport control for use at night,” said Beach. “We knew the 999s would be a good fit on this project because they have the capacity and reach coupled with the speed and mobility to efficiently move on and off the pier.”
To meet the demands of the schedule and to ensure the airport has unrestricted access to the runway at night, the cranes move off the pier to a staging area more than 700 feet from the jobsite every evening.
Moving the cranes takes approximately 80 minutes at the start and end of each day. To move the cranes rapidly on and off the narrow pier, J.F. White constructed a 35-foot by 35-foot rotating platform between the pier and the land to enable the cranes to handle the vertical disparity between the two working elevations. Each morning, after maneuvering on to the platform, the platform rotates 90 degrees so the cranes pull off the platform onto the pier. The same process takes place in reverse every evening. This has saved the time and space that would be otherwise required to move three 999s on and off the deck.
A streamlined process has ensured the cranes are on the jobsite as quickly as possible, and has allowed the project, which began in July 2011, to break for winter on November 20.
The 275-ton-capacity Manitowoc 999s are configured with 190 feet of main boom, and the 330-ton-capacity Manitowoc 2250 is configured with 160 feet of main boom. The heaviest elements in the construction of the pier are the concrete NEXT beams, which are 10 feet wide by 40 feet long and weigh approximately 50 tons each.
The extension of the runway, once complete, will enable Logan Airport to land larger jets such as 747s and 777s on the runway when other airports are forced to close due to inclement weather. The expansion is part of an FAA mandated safety improvement project and is expected to be complete by November 2012.