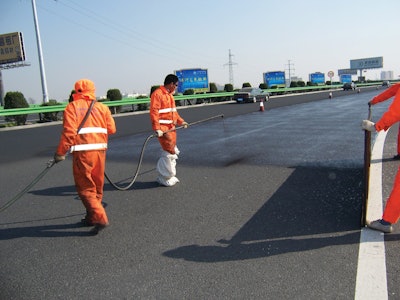
Sealcoating professionals perennially encounter a "good problem" every fall when they are under the gun to finish the projects on their books before the snowflakes start flying. The purpose of this article is to elaborate on the factors that change with ambient conditions for which proper adjustments have to be made in order to achieve the optimum sealcoating performance. Rushing through the jobs in the zeal to satisfy the pent up demands, may adversely affect your reputation and business.
Most of the sealcoatings are water-based coatings, either based on refined tar (RTS) or asphalt Emulsion (AE), which are used for the protection and preservation of asphalt surfaces. Commonly sealcoatings are supplied as concentrates, containing, typically 60% water (volume). For application, additional water is added along with sand and additives, according to the mix designs suggested by the manufacturer. The final mix typically contains 70% water by volume. Even if you don't care to remember these numbers, just remember that water has the largest proportion in the sealer mix.
Sealcoatings dry and cure by releasing all the water to the ambient, from top to bottom, in successive layers. The escape of water becomes progressively difficult from the bottom layers as the film dries. Sealcoating appearing dry on the surface may still hold moisture in the bottom layers. For the optimum performance, it is essential that all the water and the volatiles be released from the applied sealer film. Even a trace amount of water left in the film may freeze and damage the film (possibly causing disbonding and peeling) if the temperatures dip below freezing in the night. Additionally, sealcoatings are very likely to fail prematurely, if not allowed to cure sufficiently.
The critical factors in the dry and full cure of sealcoatings are:
Temperature- Ambient and the pavement; high temperature favors the water evaporation from the film while low temperature retards impedes it.
Relative Humidity (R.H.) or Humidity- the capacity of the ambient atmosphere to hold water. e.g. 50% R,H, will mean that 50% of the capacity is still available to hold water, coming out of the sealer film. Conversely 90% R.H. means that only 10% of the capacity is available, therefore the drying of the sealer will be retarded. Conclusion-Low humidity facilitates the water removal whereas high humidity significantly retards it.
Wind Velocity is another factor that helps remove the water vapors from the immediate ambient vicinity.
All the factors, especially temperature and humidity work in tandem. High temperature and low humidity accelerate the water evaporation. Conversely, low temperature and high humidity are poor cure conditions, under which sealer films take significantly longer time for cure. The differences are staggering, e.g. a drop in temperature by 20º F will increase the drying time by 2 times while 35 º F drop will increase the drying time by 3 times. These temperature changes are typical for pavement from highs to lows during the day or under the shade or sun.
Similarly, a sealer film will take 3 times longer to dry if the humidity jumps from 40% to 80%. Based on the foregoing facts, it is understandable why sealer takes so much longer to dry and cure under adverse drying conditions; temperature, humidity or a combination of both. In the early spring and late fall we encounter unfavorable conditions, which must be taken into consideration. Here are some suggestions that you may find helpful.
- Sunlight and weather considerations- Observe the sun pattern and the sun cycle. Sunlight is a very important factor. Sealer will take much longer to dry in the shade than in the direct sunlight. The temperature difference between the shaded and sunny areas could be easily 20-30 degrees. Northern exposure shall be considered due to the fact that such areas do not get much sunlight. Avoid heavy coats application. Thick applications shall be spread out evenly.
- Be prepared to wait for a while for the morning fog (nearly 100% humidity) to lift and pavement warm up before the start of sealcoating. Both fog and cold temperatures in the morning work against the drying of the sealer.
- Use specialty additives that accelerate the drying and cure process. The fast evaporating solvents contained in such additives mix with the water in the sealer and create a mixture of volatiles that evaporates much faster than water. Use the manufacturer's recommendation for the additive type and quality in the mix design.
- In the mix design use 5% less water than normally used.
- Allow extra drying time (4-6 hrs.) in between the coats.
- Consider that you will be getting shorter days, therefore, plan to get all sealcoating done by early afternoon (1-2 pm). The sealer will still have 3-4 hrs of sunlight for good drying.
- For multiple coats, you may have to schedule the job over 2 days. Don't rush the job. Barricade the sealcoated jobs if not sufficiently dry to take foot traffic by the time you leave.
- In the late fall, make absolutely sure that the temperature does not dip below freezing overnight. Even a trace amount of water left in the film will freeze and may cause peeling and disbonding of the sealer from the pavement. The sealcoating must have 8 hours of drying before any threat of freezing.
- Make sure that the pavement is dry. Damp pavements really inhibit the drying of the sealcoating.
- Be prepared to frequently remove the falling leaves on the freshly sealcoated lots, even touch ups if they drop in the wet sealer coat.
SUMMARY
Sealcoatings being water based, cure by releasing all the water from their applied films. Sealcoating applications done in the late fall or early spring require special considerations for allowing the sealer to dry and cure, optimally. Sealcoating window is often narrow, thus delaying the whole process which professional sealcoaters endure. Avoid the temptation to rush; sealcoatings cured under improper conditions are liable to have inferior performance characteristics.
Girish C. Dubey is president STAR Inc., Columbus, OH (www.starseal.com). He sincerely acknowledges the help of colleagues Greg Lucas, general manager, McConnell and Associates, and Ed Miller, president of Star Seal Of Pennsylvania, for their invaluable suggestions.