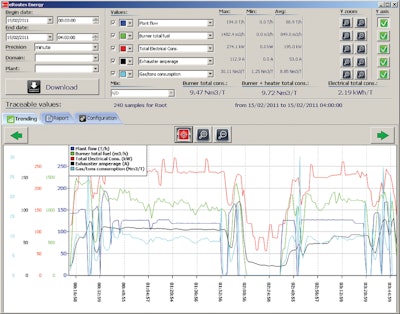
Reducing energy loss factor in hot mix heating and drying process saves producers dollars and ultimately benefits the environment. While traditional methods of energy monitoring typically involve manual calculations of utility bill data or extraction of production data from the control systems, the information is often stale and cannot be viewed instantly.
A heavy highway contractor in the Midwest chose to employ a real-time system for immediate feedback on the energy usage at one of its plants. The system acquires electrical and gas consumption in real-time and delivers the information over the internet for remote access to plant efficiency information. In addition, other information is available such as production data such as mix temperature, tons per hour, ticket data by using the eRoutes web portal and eRoutes Energy PC application.
Reporting is available to give percentage of production out of tolerance or tons produced versus tons scaled. Compatible with all plant manufacturers, eRoutes Energy provides real-time monitoring of gas, electricity, mix temperature, moisture and other production related information.
eRoutes Energy combines production data from the existing control system with acquired signals from external sensors and delivered over the Internet to the MINDS eRoutes portal and accessible via a Windows based application.
Personnel have remote access to real-time data to monitor plant efficiency right from the desktop. The operator even has access to a dashboard for instant data.
Easy installation
The system was installed and configured within a few weeks with no interruption to the plant production. The asphalt producer uses the MINDS Drumtronic control system too and the MINDS products are designed to work seamlessly with each other.
The eRoutes Energy System can be retrofitted onto any asphalt plant by means of installing external sensors for data acquisition of the sources. Secondly, by installing a capture (print-up box) device at the control house to intercept logged production data or a eRoutes gateway software that resides on the blending control PC to intercept and push relevant production data to the MINDS data center by using the available internet connectivity.
Non-renewable fossil fuels such as diesel or natural gas is a large part of the total cost of operation at a plant. At a rate of approximately 8 liters of fuel to heat 1 ton (230 cu. Ft./ton) of aggregates, the costs can quickly add up.
The next generation of eRoutes Energy will involve a tablet PC device in the control house and connect to an industrial embedded PC via WiFi for instant energy consumption feedback to the plant operator so they can make adjustments or corrections to the plant controls. A dashboard application will run on the tablet to enable a quick overview of the current usages.
“The eRoutes Energy system is a great visibility tool especially when managing multiple plants remotely,” says Gaetan Nantel, senior automation specialist at MINDS Inc.