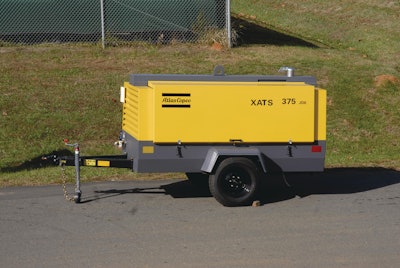
The latest evolution in towable compressors places an emphasis on efficient design as manufacturers begin to transition to Tier 4 engine technologies.
“As with many things these days, towable compressors are trying to become greener and more efficient as they evolve,” says Chance Chartters, sales manager, Mobilair, Kaeser Compressors. “Every compressor manufacturer is trying to design their air end, or the actual rotary screw portion of the compressor, as efficiently as possible to use less horsepower to make the same amount of air.”
Examine efficiency when comparing compressors. An efficient design will use less horsepower to deliver the same or more air. “Everybody is conscious of fuel these days. If the compressor can operate eight hours using six gallons of fuel as opposed to 10 gallons, that is a benefit,” notes Chartters. “Our Model M57, which delivers 210 cfm does that with an engine rated for less than 50 hp,” says Chartters. This compares to some units that require 60- to 70-hp at 185 cfm.
Kaeser typically accomplishes this efficiency by running the engines at a lower speed. This approach generally requires larger rotors on the air end. “So we use a larger air end and we turn it at a slower speed. The horsepower rating of the engines is generally less.” And slower engine speeds can also prolong the life expectancy.
Atlas Copco has also been busy developing new technology to make its compressors more efficient. One example is unique fuel saving system that electronically regulates the engine speed and the air inlet valve to optimize fuel consumption “Electronic regulation of the inlet valve has been a recent advancement,” says Blake Gearhart, product & business development manager for high pressure applications, Atlas Copco. The company also reports recent advancements in technology with improved rotor efficiencies. “Air Tech has made our elements more efficient, thus we can get more air with the same horsepower required. Therefore we are more efficient per CFM produced.”
Doosan Portable Power also reports increased efficiencies. “Some of our models have variable-speed cooling fans inside the enclosure,” says Warner. “They are thermostatically controlled, so they only spin when they need to cool and that saves quite a bit of horsepower and contributes to fuel efficiency.”
Life-cycle costs are a critical point of differentiation. “You have acquisition cost and then the cost to run it,” says Warner. “Your fuel economy plays into that.” Variable-speed clutches, thermostatically-controlled fans and more precise temperature control devices that optimize the temperature play an important role.
Impact of Tier 4
Tier 4 is going to add cost to all products. “We know that Tier 4 is expensive,” acknowledges Warner. “It is a government regulation. There is nothing anybody can do to change that. But there are ways we can turn this into an opportunity. There is technology, that if we choose to use it, makes your life better.”
He explains that the double-axle large compressors have witnessed most of the advancements with the move to Tier 4 interim engines. These advancements are tied to the amount of data that can now be accessed from the electronic engines through the CAN BUS. “On our new line of 750 cfm compressors we have a new control panel with a digital display to capture all of the data. There is too much data to put through mechanical gauges anymore. We have all of these different parameters that the operator can use to gain efficiency or look at the jobsite better.” Historical data regarding events or fault codes are also available.
This information is now also available remotely. “We are just launching Wi-Fi radio that is going to be standard on all of our large compressors,” says Warner. “It will broadcast data from the CAN BUS to a smart phone or a laptop. It will broadcast a local signal that authorized devices can pick up. If a fleet manager is in a trailer on a jobsite, he can review all the local machines by serial number and look at the hours, look at the fuel levels and relay that information.”
The next step will be integrating this technology with existing telematics solutions. “This technology is very easily portable so we can easily put it out via the internet and put it on a server relatively easily,” says Warner. “Contractors have been making investments in telematics and our systems will work seamlessly with those.”
Tier 4 has also focused attention on enclosure design. “The engines have a much higher heat rejection and that drives cooling,” says Warner. “So the radiators are larger, the fans are larger. Overall, that has created a larger footprint for a machine. We have been able to maintain our existing footprint on all of our machines, but it was a lot of work. The package is much more engineered primarily because we have a hotter engine and we have to make sure that the cabinet is cool enough for that engine to be optimized and the other internal components are not compromised. So air flow and cooling technologies have been critical.”
Nothing has been taken for granted. “With the EPA emission regulations, it helped us to look at just about every part of the way we engineer the packages and we found areas where we can improve the overall design,” says Gearhart. “Space, size and increased temperatures have helped us look for more efficient ways to exhaust and cool our equipment. In some cases it is more efficient coolers, in others we are looking at variable speed fans, etc.”
Other considerations
Noise and durability are also key design considerations.
“The noise end is very important,” notes Chartters. “Really, the air end isn’t loud. You are really looking at the diesel engine itself that is creating the noise. We tested one of the compressors at a lower rpm. If it is running at a lower rpm it usually doesn’t make quite as much noise.”
One of the advancements at Kaeser has been the introduction of a polyethylene rotomolded (PE) canopy that is lighter as well as scratch and dent resistant. “It is double walled so it has sound attenuation. We try to keep the noise inside the package. We try to make a unit that is really well enclosed, just letting air in and out for cooling,” says Chartters. “Obviously you have to have it open for airflow, but you are just trying to keep as much noise inside the package as possible.”