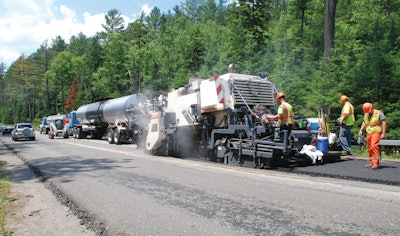
Cold-in-place recycling involving both a Wirtgen 3800 CR (with 12.5-ft. cutter) and a 2200 CR (with 8-ft. cutter) was the “green” choice for rebuilding a two-lane state highway in a mountainous, environmentally sensitive area of New York State’s Adirondack State Park.
These days nearly any project can be “environmentally sensitive,” but this work was more so, taking place within the confines of the state park, and adjacent to the ski resort town of Lake Placid, home to the U.S. Olympic Training Center, and site of the 1980 Winter Olympics.
Both the 3800 CR and 2200 CR from Wirtgen are unique in the industry as they can undertake cold-in-place recycling using emulsions, foamed asphalt or cement slurry, but with a few hours’ work – including addition of conveyors – can be converted into full-depth, 950 hp cold milling machines.
In early June 2012, the new 3800 CR was being used on its first-ever project. “This is our maiden voyage with it,” said Mike Haggerty, sales manager, Reclamation LLC, West Hurley, N.Y. “We love the machine, and its production is superior to any other reclamation machine on the market today.”
The larger 3800 CR will foam-stabilize about 10,000 feet per day, compared to about 6,000 feet per day with the 2200 CR it is teamed with, Haggerty said. “The 3800’s cut is wider and the machine is very powerful, as we hook up to a 9,000-gal. asphalt trailer and a 6,000-gal. water tanker, and push both as one unit.
Two Hamm HD 130 VV tandem vibratory rollers were used for initial and intermediate compaction, and a brand new GRW 280 pneumatic roller with 30 tons of weight was used for finish rolling. “It’s our second season with the GRW 280 and it’s a great follow-up roller,” Haggerty said. “It kneads the material together and polishes it off, providing a surface very similar to hot mix asphalt, depending on the material.” Traffic would use the recycled surface until a HMA overlay was placed on it a few weeks later.
The specification of foamed asphalt not only permits 100 percent recycling of an existing road into a stabilized road base, but actually extends the limited construction season in the mountainous Adirondacks.
“They are cold-in-place recycling a depth of 4-in. with foamed asphalt,” said Mike Marshall, director recycling products, at Wirtgen America Inc. “Two percent asphalt cement is being added by mass bulk of material. In addition, a nominal 3/4-in.-size stone is being added, pre-spread on the pavement, and mix it in with the existing pavement, and stabilize both with foam. The finished structure will be 4 in. thick.”
The “add-stone” is required by New York State specs, Marshall said. “The combination will be 85 percent existing materials, and 15 percent new. The add-stone acts as a leveling agent to fill dips and irregularities in the pavement, and the higher-quality virgin aggregate supplements the RAP in the pavement, making it stronger and better. It’s a winning formula that works very well for them.”
“The foamed asphalt will allow us to work late into the fall,” Haggerty said. “Plus, In Lake Placid, tourism is the No. 1 industry. Our traffic pattern is shorter, and on this very, very busy road we have very, very few complaints. The happier the public is, the happier the resident engineer and the community will be.”
With the average production rate for the 3800 CR on this project being 520 tons per hour, in-place recycling eliminated over 50 truck trips of materials per hour in this remote, mountain location.
And the 100 percent recycle is just another plus for Reclamation LLC and the New York State DOT. “Here in the Adirondacks that’s very important,” Haggerty said. “The folks up here are very environmentally conscious, and they smile at our operation.”